Shot blasting machine, not powered by compressed air, but by electro-mechanical blasting turbines, the use shot blasting machine throwing high-speed projectiles to clean or strengthen the surface of the metal workpiece equipment. A shot blasting machine can clean the metal workpiece surface of various residues, and can be castings for sand, core removal, cleaning, etc. Shot blasting is to rely on the impeller high-speed rotation, the abrasive in the center of the impeller, through the regulator and impeller pre-acceleration, sent into the blade area, and then the abrasive high-speed throwing, speed can exceed 100m / s, due to shot blasting coverage is large, so do not need to use air pressure, energy efficiency is much higher than sandblasting. The impeller is the heart of the blast machine, driven directly or indirectly by an electric motor, and each impeller manufacturer has a unique design, mainly divided into single-disc and double-disc impellers. Shot blasting machine, using the blast turbine throwing high-speed projectiles to clean or strengthen the surface of casting parts. Shot blasting machines can simultaneously drop sand, core removal, and cleaning castings. The main use of the high-speed rotation of the impeller is to throw the shot sand, and high-speed impact on the surface of the parts to achieve the surface treatment requirements.
Application range of shot blasting machine
1, metal surface cleaning shot blasting equipment is first applied to the casting industry cast steel, cast iron parts of the surface of the sticky sand, and oxide skin removal. Almost all cast steel parts, gray castings, steel parts, ductile iron parts, etc. are subject to shot blasting treatment. This is not only to remove the casting surface oxidation and sticky sand but also casting quality inspection before the indispensable preparation process, such as large gas turbine casing in the nondestructive testing must be carried out before the strict shot blasting cleaning to ensure the reliability of the flaw detection results. In the production of general castings, shot blasting cleaning is an indispensable process for finding surface defects in castings such as subcutaneous porosity, slag holes, sticky sand, cold compartments, skin, etc.. Non-ferrous metal castings, such as aluminum alloys, copper alloys, and other surface cleaning, in addition to the removal of oxide, the discovery of surface defects in castings, the main purpose is to blast shot blasting to remove burrs and die casting surface quality with decorative significance, to obtain a comprehensive effect.
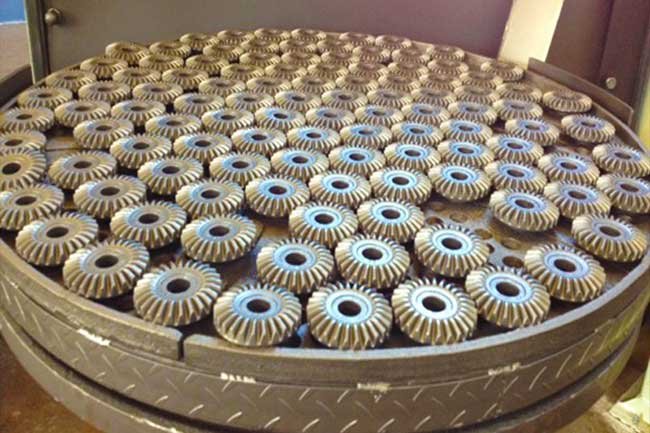
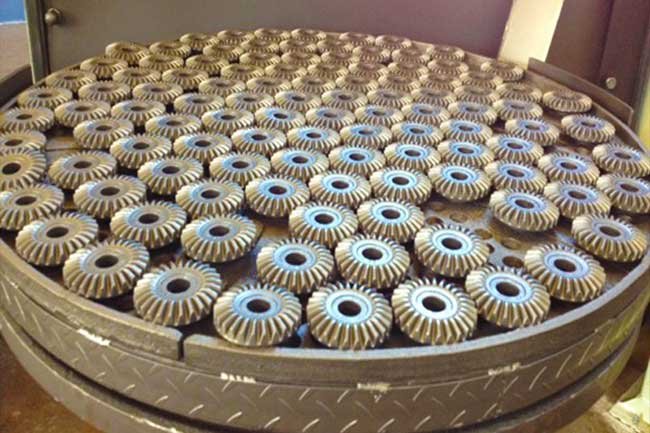
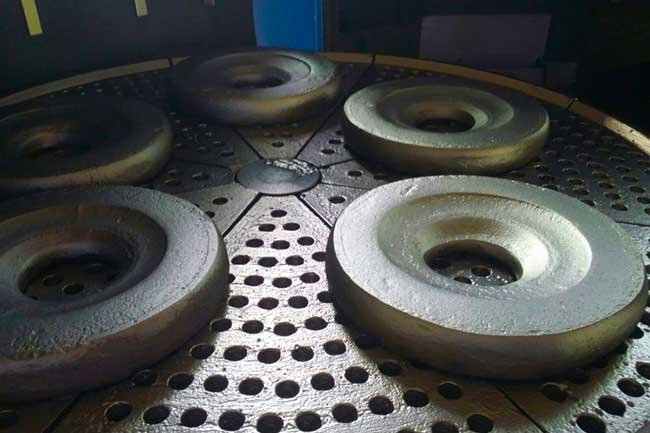
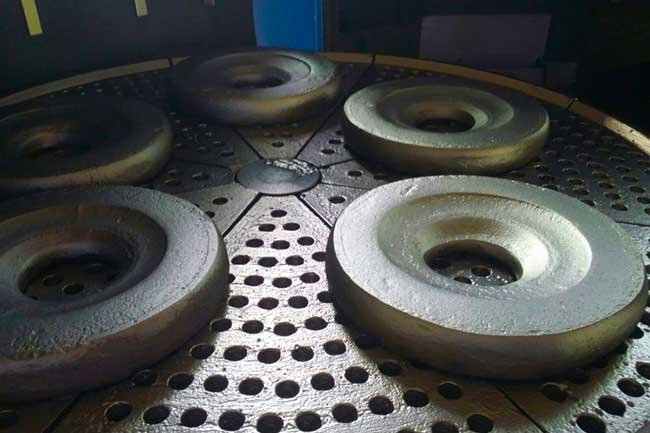
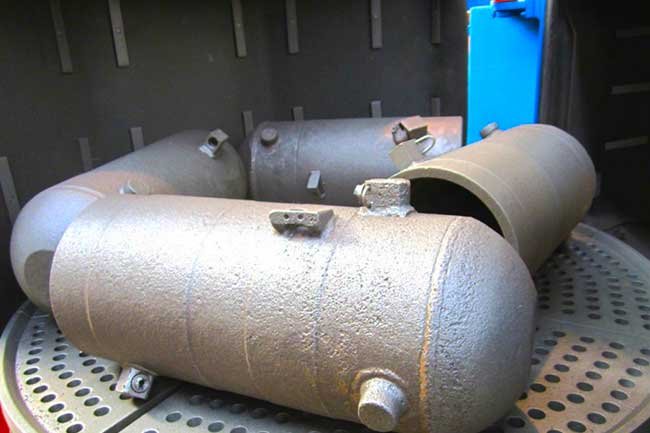
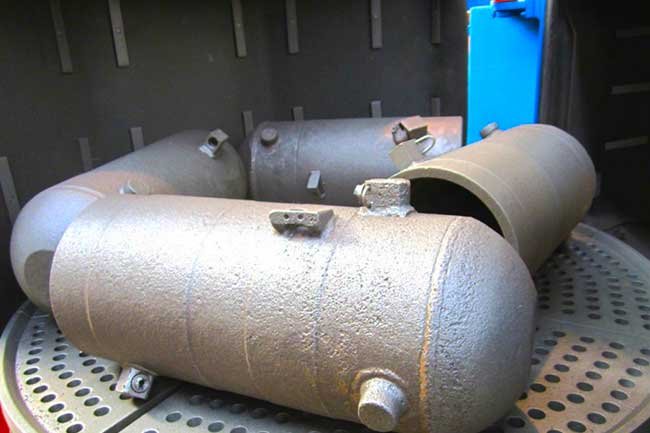
Metallurgical steel production shot blasting – pickling is a combined surface preparation technology, which is to ensure that the large steel production obtains high productivity on the removal of phosphorus skin. Silicon steel sheet, stainless steel sheet, and other alloy steel plate, strip production, in the process of cold rolling process must be annealed with a shot blasting a pickling treatment to ensure the surface roughness and thickness accuracy of cold-rolled steel.
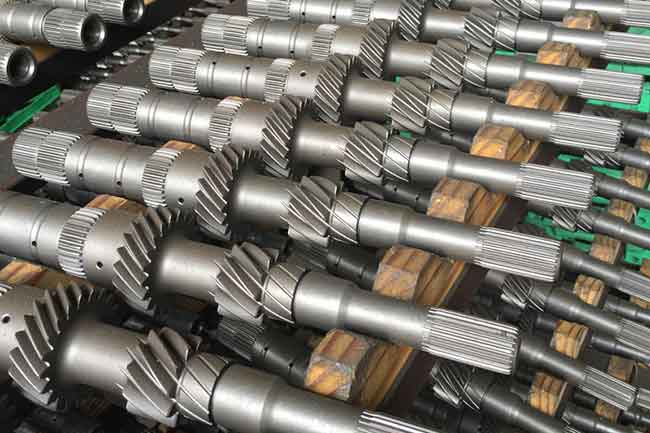
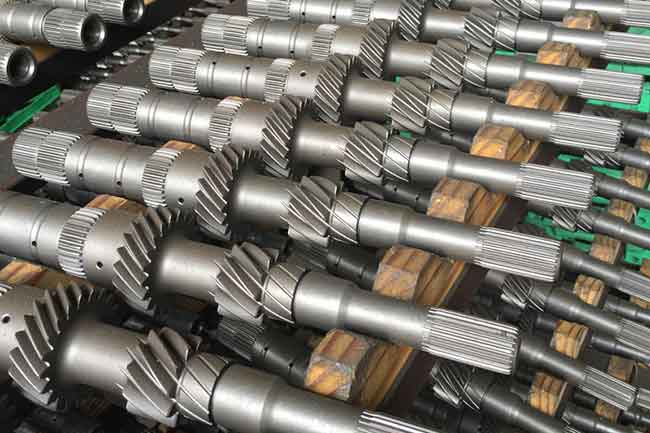
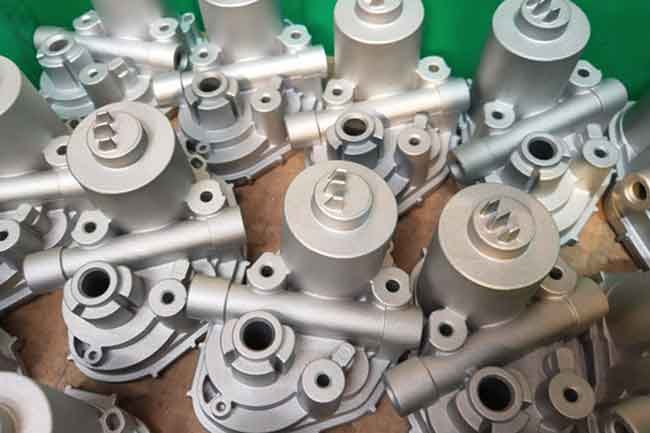
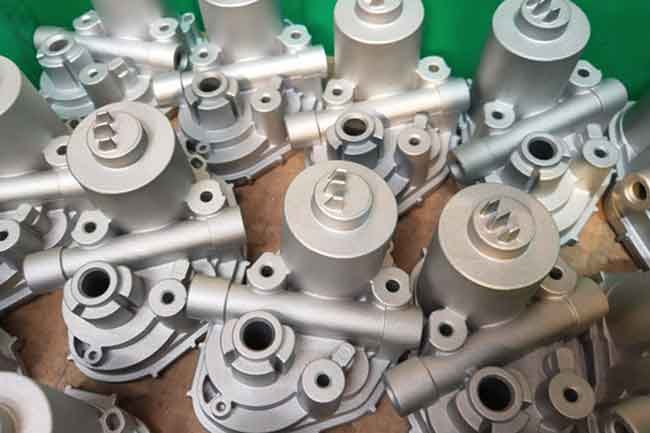
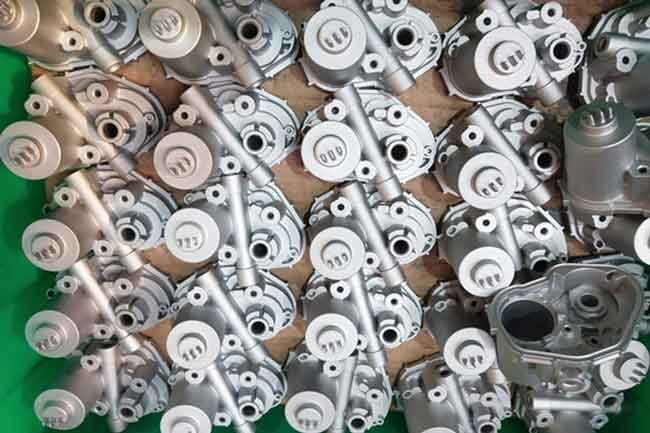
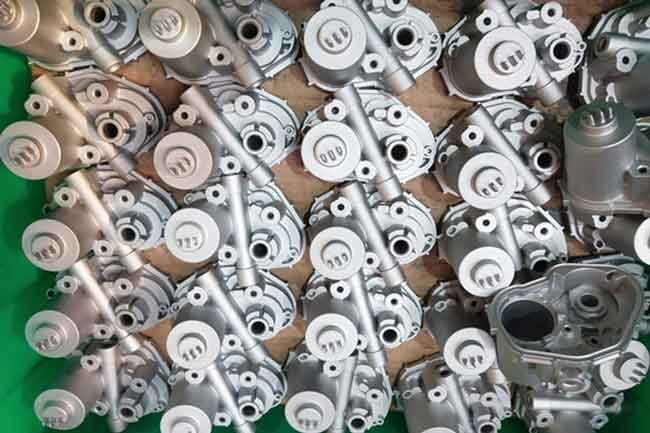
2 Strengthening of metal workpieces
According to modern metal strength theory, increasing the dislocation density inside the metal is the main direction to improve the strength of the metal. The practice has proved that shot blasting is a proven process method to increase the dislocation structure of metals. This is very important for some metals that cannot be hardened by phase transformation (such as martensitic punching, etc.) or on the basis of phase transformation hardening and require further strengthening of the workpiece. Aviation, aerospace industry, automobiles, tractors, and other parts require lightweight, but the reliability requirements are increasingly high, the important process is the use of shot blasting process to improve the strength and fatigue strength of the components.
Shot Peening and Hardening Application – Shot Peening Principle
Shot blasting relies on the high-speed rotation of the impeller, the abrasive in the center of the impeller, through the Regulator and Impeller pre-acceleration, sent into the blade area and then the abrasive high-speed throwing, speed can exceed 100m / s, due to the blasting coverage of a large area, so do not need to use air pressure, energy efficiency is much higher than sandblasting.
Shot peening is used to improve the fatigue strength of workpieces subjected to high and alternating stresses. Shot peening has replaced other time-consuming and expensive processes on a large scale, enabling the design of lower cost, lighter weight components; it has played a significant role in improving the physical properties of workpieces.
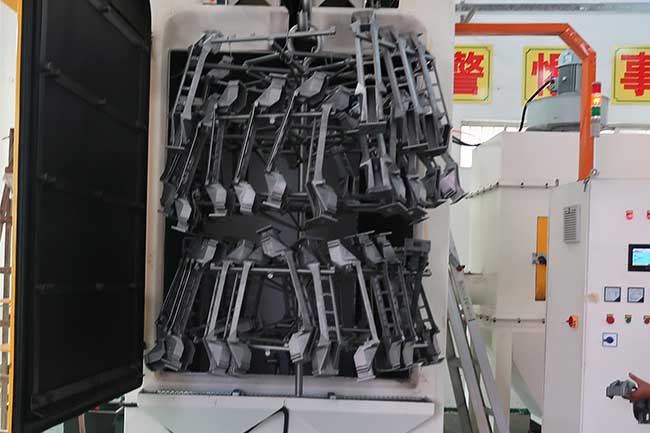
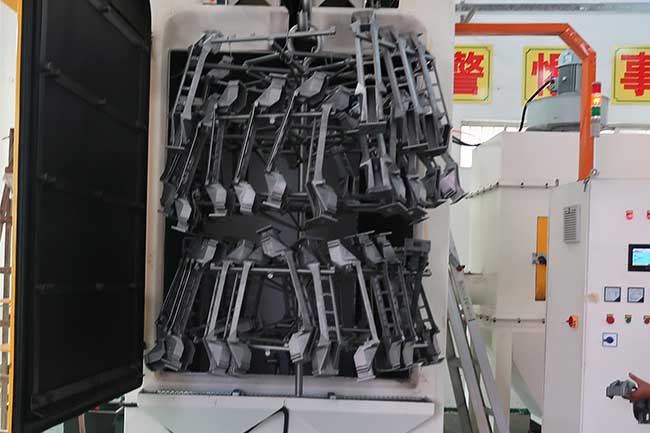
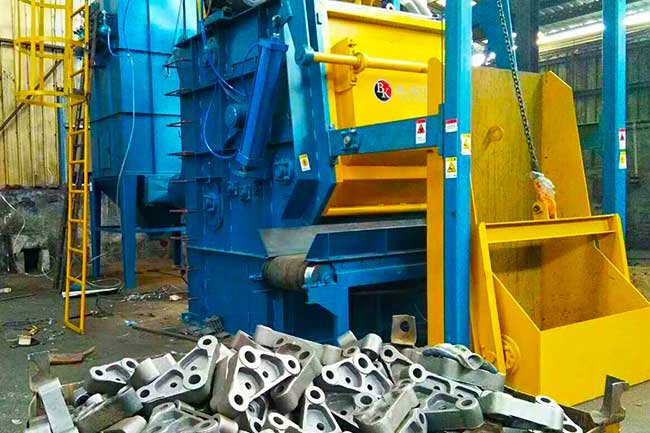
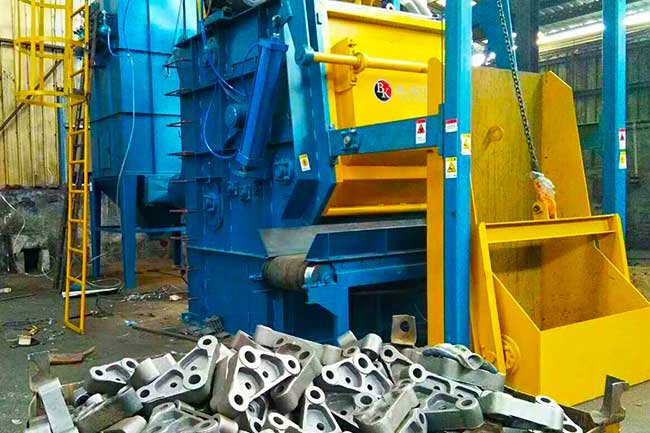
Shot peening features
The steel shot is shot onto the surface of the workpiece without compressive and tensile stresses, obtaining a regional distribution of pressure and tension. By surface peening, the stresses can be made uniform. Shot peening is particularly effective in continuous peening where the surface tension is reduced, which is why shot peening increases the fatigue strength of metals.
Shot-hardening and application areas aircraft components, compressor shafts, shafts, gear shafts, brake parts, cams, camshafts, chain bolts, links, clutch springs, round springs, compressor blades, connecting rods, machine shafts, gearbox components, gears, leaf springs, milling cutters, drills, cutting tools, piston rods, pushrods, wheels, rock chisels, springs, stabilizer rods, suspension springs, synchronous pro-joining springs, tension springs, tools, torsion bar springs, turbine wheels and blades, valved springs, valves, wheel perseverance, steering wheels.
Applicable materials; hard metal, cast steel, aluminum, magnesium, bronze, ductile ink casting. Shot Peening Pretreatment – Refurbishment and Retrofit
In the painting industry, shot blasting machines are used for the pretreatment of workpiece surfaces, such as for radiators, gas cylinders, steel drums, containers, barrels, tubes, drums, etc., to ensure perfect adhesion of paint to the workpiece.
The shot blasting process also removes old paint before a new paint job. Alternatively, large cleaning chambers with wheels and blasting units can be used to mechanically remove or refurbish large workpieces such as welded steel structures, wagons, ship plates, and railroad cars.