Unlock the Ultimate Cleaning Weapon: The Rise of Automatic Shot Blasting Machines
Discover how automatic shot blasting machines are revolutionizing the cleaning industry. Learn about their benefits and applications.
By Mathew Lee| Updated: March 11, 2024
Cleaning and preparing surfaces for a variety of industrial applications is a crucial process that demands accuracy. Automatic shot blasting devices have revolutionized the surface cleaning and preparation industry in recent years. These devices provide a potent and efficient method for removing contaminants, rust, coatings, and surface flaws from a variety of substrates. This article will examine the advantages and applications of automatic shot blasting machines, casting light on their significance in the industrial cleaning industry.
Outline
Get A Strong Partner at Your Side Now!
BlastKing’s ability to improve your business profitability is based on more than 40 years’ experience and a spirit of innovation.
1. Introduction
In the realm of industrial cleaning, the elimination of contaminants and the preparation of the surface are essential for optimal results. Traditional techniques such as scraping by hand, sanding, and chemical cleansing have limitations in terms of speed, efficiency, and consistency. However, the introduction of automatic shot blasting equipment has revolutionized the cleaning and preparation process, making it more advanced and efficient.
2. What is an Automatic Shot Blasting Machine?
A mechanical device, an automatic blasting machine propels abrasive particulates at high velocities to clean and prepare surfaces. This technology utilizes the abrasion principle to eliminate contaminants, corrosion, scale, and old coatings from various materials. By bombarding the surface with minuscule steel balls or grit, the machine ensures uniform cleaning and creates an ideal surface for subsequent treatment or coating.
3. The Evolution of Shot Blasting Machines
Since their inception, shot blasting devices have undergone significant development. The evolution from manual portable devices to large-scale automatic systems has been driven by the need for greater productivity, improved surface quality, and enhanced safety. Modern shot blasting machines include advanced features such as variable speed control, automated material management, and precise shot flow regulation, making them highly efficient and user-friendly.
4. The Working Principle of Automatic Shot Blasting Machines
Automatic shot blasting machines adhere to a clearly defined procedure for optimal surface preparation. Here is a detailed explanation of their operating principle:
4.1 Positioning and Loading:
The item of work is placed on a conveyor system or inside a chamber.
The machine assures proper alignment and secure fixation for efficient cleaning.
4.2 Destructive Propulsion
The device activates a high-speed impeller, which propels abrasive projectiles or grits towards the surface.
The abrasive particles strike the surface with controlled force, removing contaminants and producing a profile with a textured appearance.
4.3 Dust Collection
During the blasting procedure, a substantial quantity of dust and debris is produced.
To maintain a clean working environment and safeguard the operators, automatic shot blasting devices are outfitted with robust dust extraction systems.
4.4 Abrasive Recuperation
These machines integrate an abrasive recovery system to reduce waste and enhance cost-effectiveness.
The system accumulates used abrasive particles, separates them from debris, and reuses them.
4.4 Surface Examination
After the blasting procedure is complete, the surface is inspected thoroughly.
Any remaining contaminants or flaws are identified and appropriately addressed.
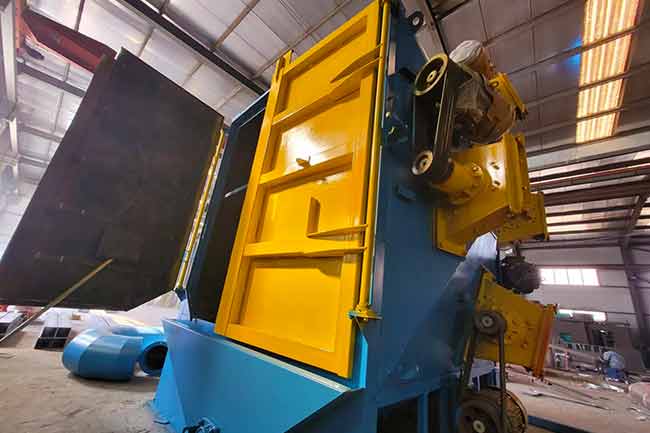
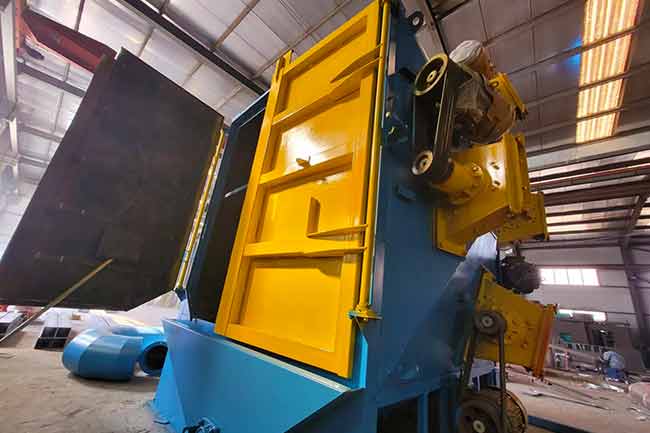
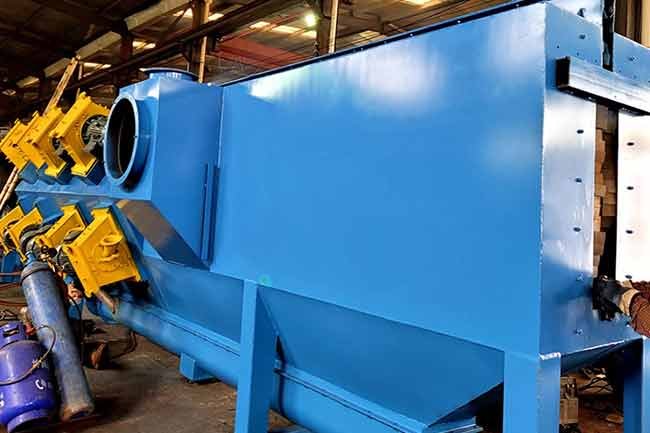
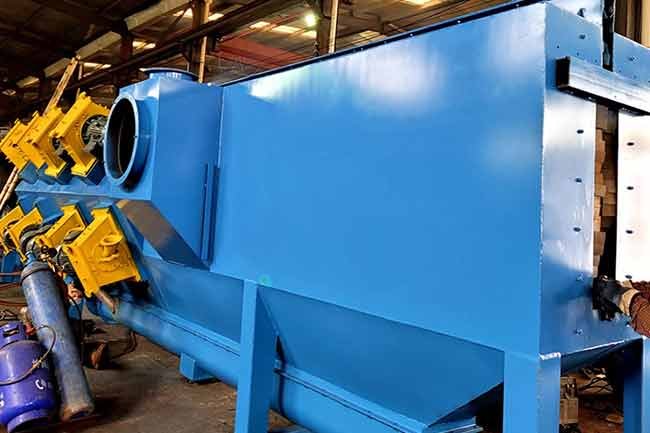
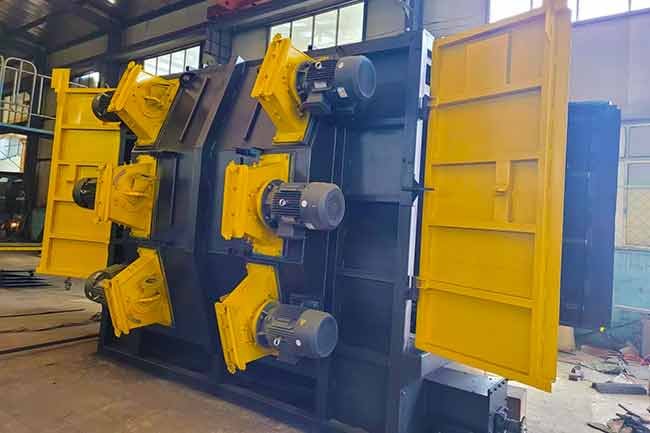
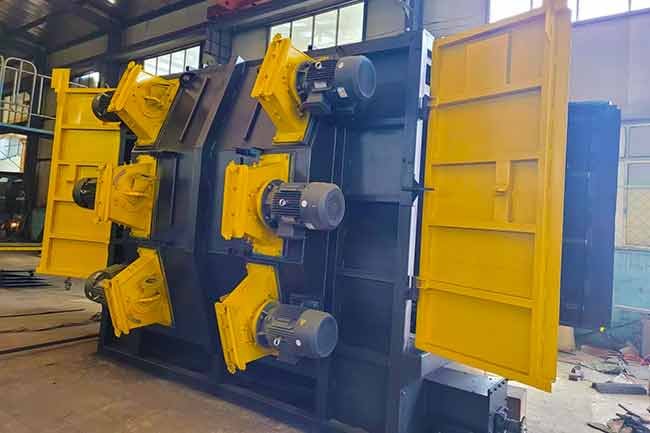
5. Applications of Automatic Shot Blasting Machines
Automated shot blasting machines have applicability in a number of industries and markets. These devices are utilized to prepare concrete surfaces, remove epoxy coatings, and clean steel structures in the construction industry. In the automotive industry, shot blasting is used to clean engine components, prepare car bodies for painting, and eliminate paint and corrosion from chassis. In addition, shot blasting devices are also utilized in the aerospace, foundry, steel plate shot blasting, and shipbuilding industries.
6. Benefits of Automatic Shot Blasting Machines
Numerous advantages make automatic shot blasting machines the preferred option for surface preparation in a variety of industries. Let’s explore some important benefits:
- Enhanced Productivity and Efficiency:
Automatic shot blasting devices are capable of processing a high volume of workpieces in a shorter amount of time.
Their automated operation reduces manual labor and increases productivity significantly.
- Uniform and Consistent Cleaning:
These machines assure consistent and uniform surface cleaning, leaving no untreated areas.
The controlled abrasive propulsion ensures a uniformly textured and smooth profile.
- Preparation of the Surface for Coating:
Automatic shot blasting machines prepare surfaces for effective coating adhesion by removing contaminants and producing an ideal surface profile.
This increases the durability and longevity of coatings, reducing the frequency with which they must be maintained.
- Versatility:
Automatic shot blasting devices can process a variety of materials, such as metals, concrete, and stone, among others.
This adaptability qualifies them for a variety of applications in industries such as automotive, aerospace, construction, and shipbuilding.
- Cost-effectiveness:
Automatic shot blasting devices help reduce material waste through their efficient operation and abrasive recovery systems.
As a result, they are a cost-effective option for surface preparation duties.
FAQs
FAQ 1: How does an automatic shot blasting machine differ from manual blasting methods?
Compared to manual blasting methods, an automatic shot blasting machine offers a greater degree of efficacy and consistency. It can produce a greater quantity of workpieces in a shorter amount of time, ensuring uniform cleaning and preparation. In addition, automatic machines include sophisticated features such as dust extraction and abrasive recovery systems, which increase productivity and decrease material waste.
FAQ 2: Can automatic shot blasting machines handle delicate materials?
Yes, by modifying the operating parameters, automatic shot blasting devices can manage delicate materials. Customization of the machine’s parameters, including blast pressure, speed, and choice of abrasive media, ensures gentle treatment of sensitive surfaces. This adaptability makes them appropriate for a vast array of materials, from sturdy metals to delicate glass.
FAQ 3: Are automatic shot blasting machines environmentally friendly?
Environmental sustainability is prioritized by automatic shot blasting devices in a number of ways. Their dust extraction systems efficiently capture and contain hazardous particles, minimizing the emission of air pollutants. Moreover, the incorporation of abrasive recovery systems reduces material waste and promotes resource efficiency, rendering them environmentally favorable surface preparation options.
FAQ 4: What safety measures are necessary when operating an automatic shot blasting machine?
Strict safety protocols must be followed when operating an automatic shot launching machine. The following are some crucial safety measures:
Utilizing personal protective equipment (PPE) such as safety glasses, gloves, and protective apparel.
Ensuring proper ventilation and respiratory protection in order to minimize exposure to dust and pollutants.
Regular inspection and upkeep of the machine to identify any potential dangers or malfunctions.
Training operators in the safe operation and emergency procedures of machinery.
FAQ 5: Can an automatic shot blasting machine remove old paint from surfaces?
Yes, shot blasting devices are extremely effective at removing old paint from surfaces. The paint layers are removed by the high-velocity abrasive particles, revealing a pristine surface beneath. This procedure is faster and more effective than manual paint removal techniques such as scraping and sanding.
FAQ 6: Can an automatic shot blasting machine be used for surface roughening?
Absolutely. Surface roughening is an application where automatic shot blasting devices excel. By modifying the blast pressure and type of abrasive media, they can generate the desired surface profiles for enhanced coating or treatment adhesion. In industries such as construction, where concrete surfaces must be properly prepared prior to applications such as waterproofing and resurfacing, surface roughening is particularly essential.
7. Conclusion
The efficacy, versatility, and steadfastness of automated shot blasting apparatus have revolutionized the domain of surface preparation. From manufacturing facilities to construction sites, these mechanisms have become indispensable across a myriad of industries. Automated shot blasting machines play a pivotal role in upholding the caliber and endurance of end products, owing to their ability to expunge contaminants, fortify surfaces, and prime them for coatings.
Whether engaged in the restoration of antiquated machinery, preparing surfaces for painting, or enhancing the resilience of concrete edifices, an automated shot blasting machine stands as the optimal choice.
However, for those involved in coating services, tasked with managing a diverse array of components varying in size, shape, and weight, a blast room emerges as the superlative alternative for handling such projects. The production cost of the blast room hinges on the workforce within, diverging from auto blasting machines, where the overall power consumption remains substantial even when cleansing diminutive components is the sole requirement.
However, for those involved in coating services, tasked with managing a diverse array of components varying in size, shape, and weight, a blast room emerges as the superlative alternative for handling such projects. The production cost of the blast room hinges on the workforce within, diverging from auto blasting machines, where the overall power consumption remains substantial even when cleansing diminutive components is the sole requirement.