1. What Is A Wet Blast Cabinet
A wet blast cabinet is fundamentally a specialized enclosure crafted for surface treatment using a slurry mixture of water, abrasive media, and pressurized air. Unlike conventional dry blasting methods, wet blasting minimizes dust emissions, offering a more controlled and precise approach to surface preparation.
Importance of Wet Blast Cabinets in Various Industries:
Industries globally have recognized the pivotal role of wet blast cabinets in achieving optimal surface finishes while addressing environmental and health concerns. The versatility of these cabinets renders them indispensable in a spectrum of tasks, ranging from paint removal to delicate restoration projects.
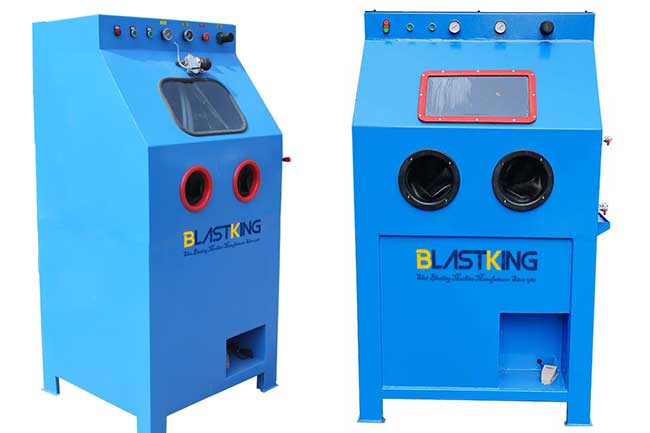
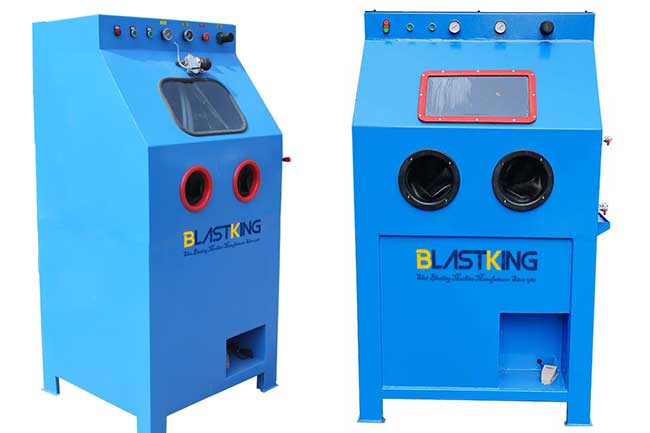
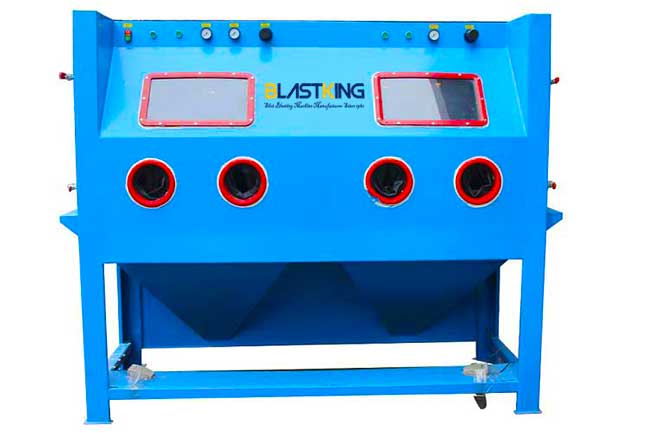
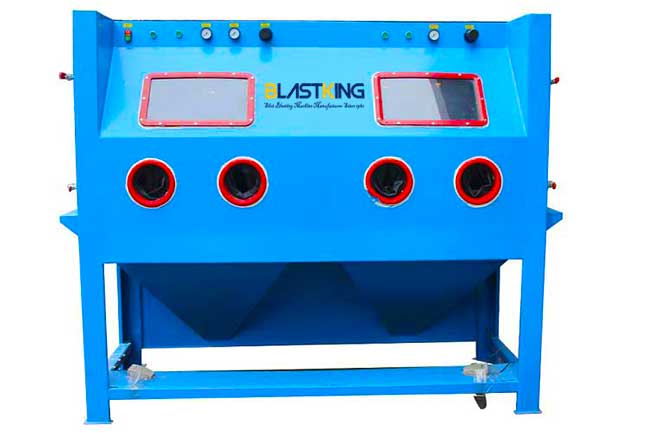
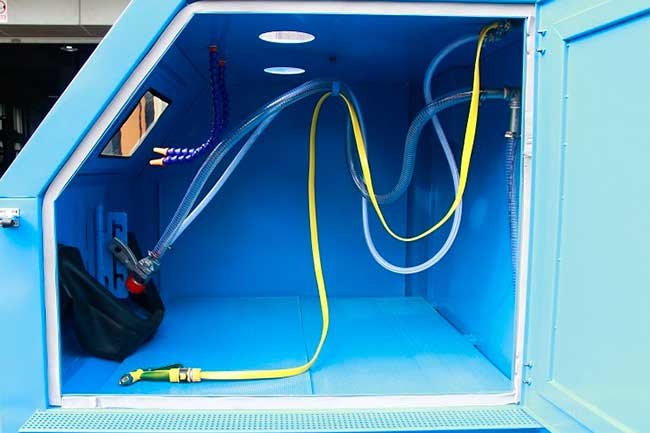
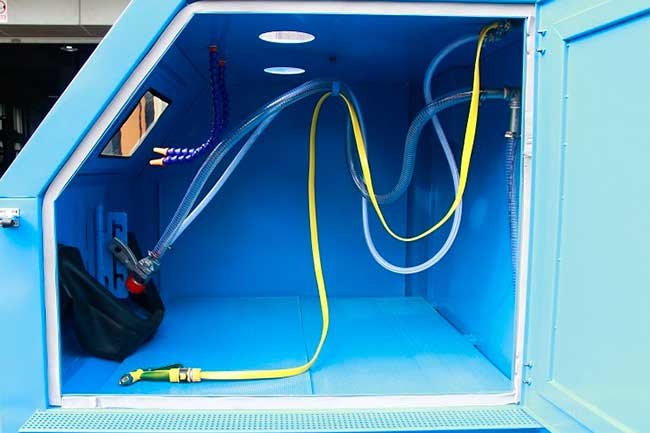
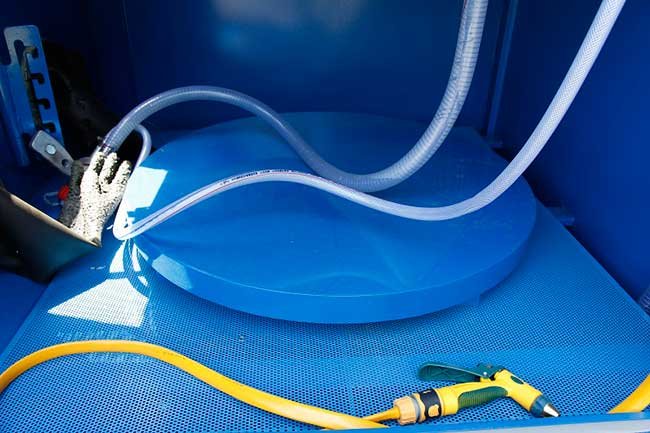
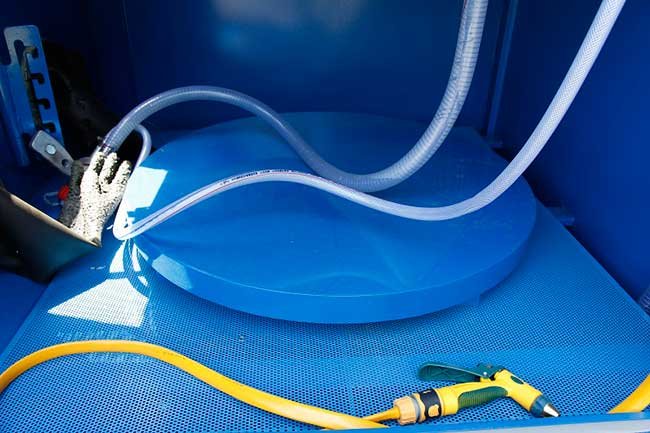
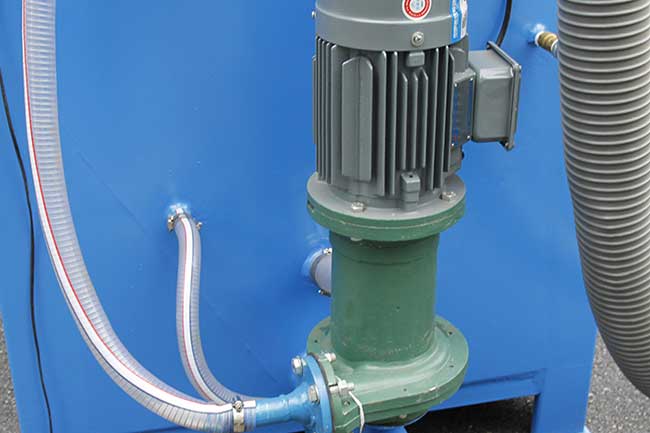
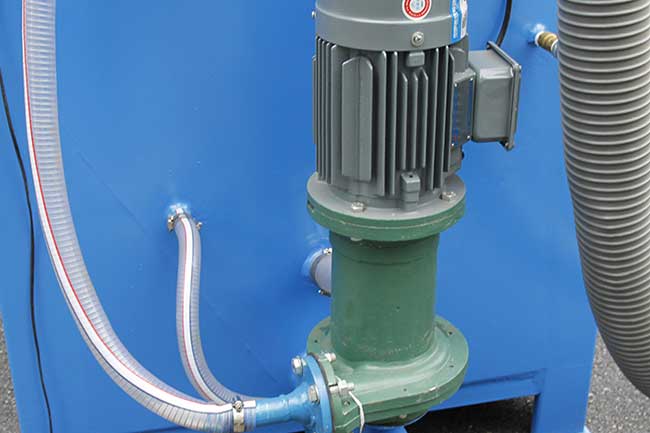
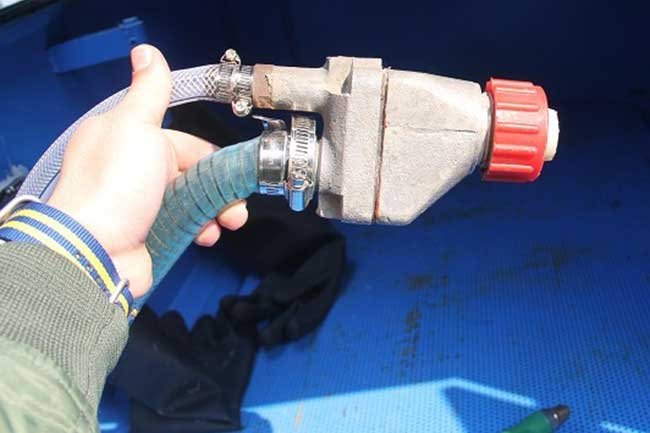
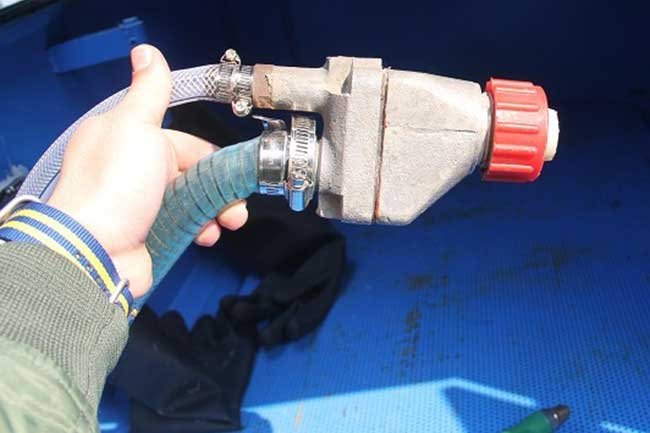
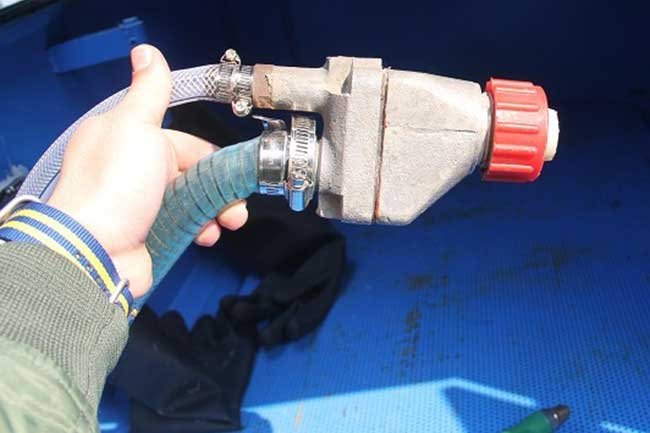
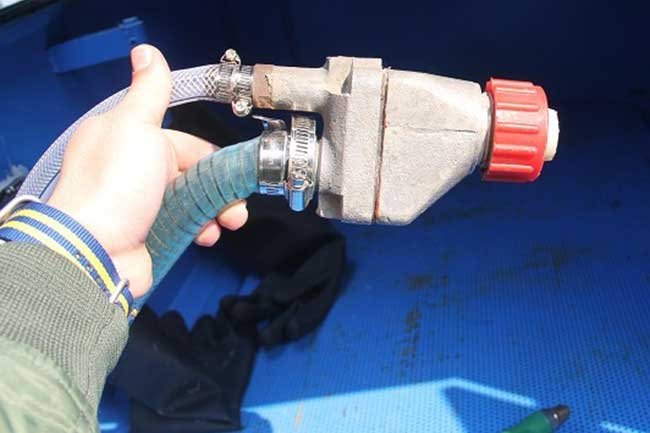
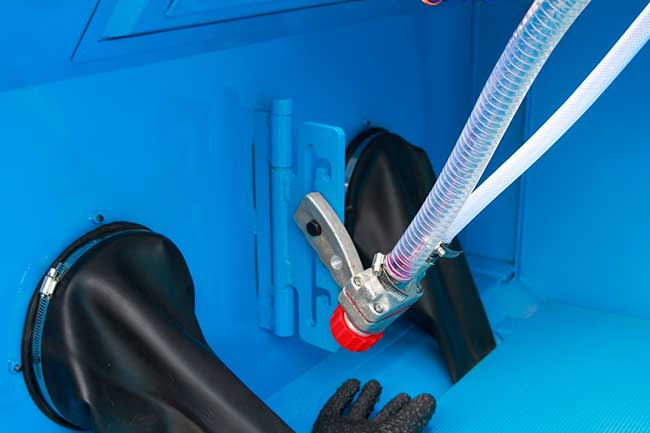
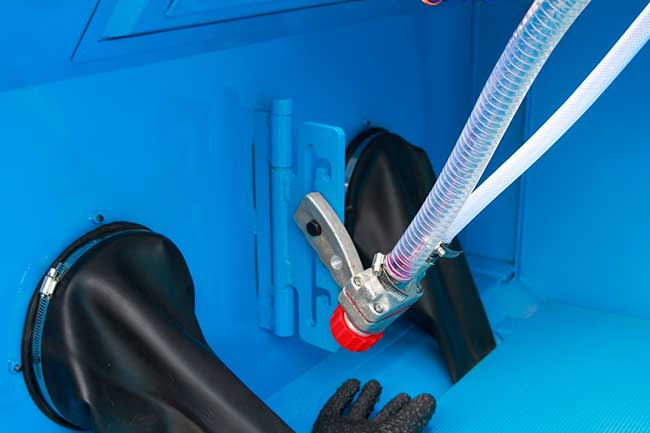
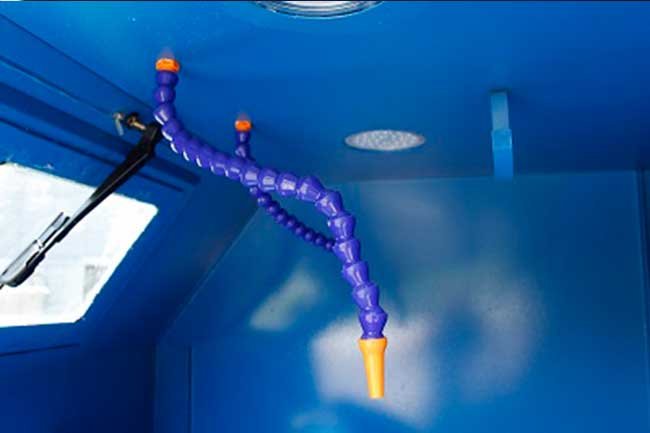
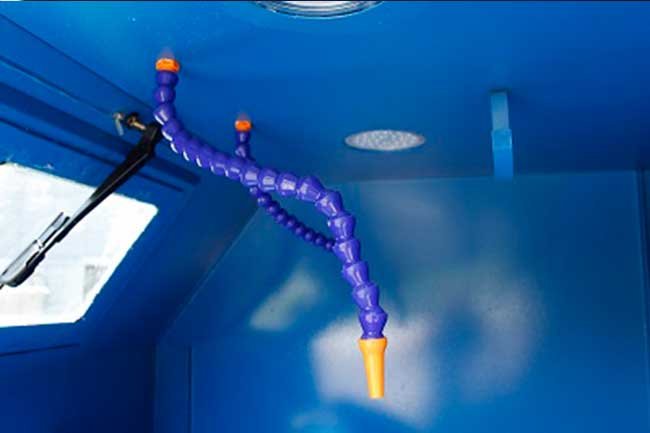
2. Wet Blast Machine Features
1. Low Noise Levels: Operates with minimal noise, providing a quieter working environment.
2. Robust, Stainless Steel Construction: Built with durable stainless steel, ensuring a sturdy and long-lasting structure.
3. Large Viewing Window with Water Spray and Wiper: Equipped with a spacious viewing window featuring water spray and a wiper for enhanced visibility during the blasting process.
4. Integral Turntable, Tumble Belt, etc., for Easy Component Handling: Includes integral features like a turntable or tumble belt for convenient handling of components.
5. Closed-Loop Recirculation System: Utilizes a closed-loop system that filters and recirculates the abrasive media and water mixture, promoting efficiency and sustainability.
6. Interlocked Door: Features an interlocked door for safety and controlled access.
7. Simple Hands-Free Pump Controls: Offers user-friendly, hands-free controls for pump operation.
8. Water Level Control: Equipped with a water level control system to maintain a consistent water level in the cabinet.
9. High-Performance Wear-Resistant Pump and Process Gun: Utilizes a high-performance pump and process gun with wear-resistant features for efficient operation.
10. Efficiently Removable Pump and Motor: Allows for easy removal of the pump and motor without the need for machine emptying.
11. Adjustable Nozzle and Pressure Settings: Features an adjustable nozzle and pressure settings, providing operators control over the flow and pressure of the abrasive media and water mixture. This adaptability allows customization of blasting parameters based on the application and workpiece.
3. Key Benefits
4. The Wet Abrasive Blasting Machine Application
The Wet Blast process offers a comprehensive solution for component cleaning, scratch removal, degreasing, and finishing in a single operation. In comparison to dry blasting, it is less aggressive, eliminates dust generation, allows safe processing of materials like titanium without the risk of explosion, reduces media consumption, and results in a cleaner and brighter surface finish.
Applications of Wet Blast Process:
The versatility of the Wet Blast process makes it suitable for various applications, including:
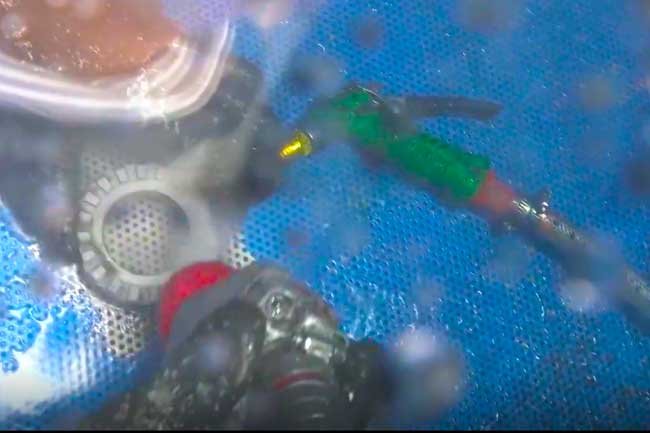
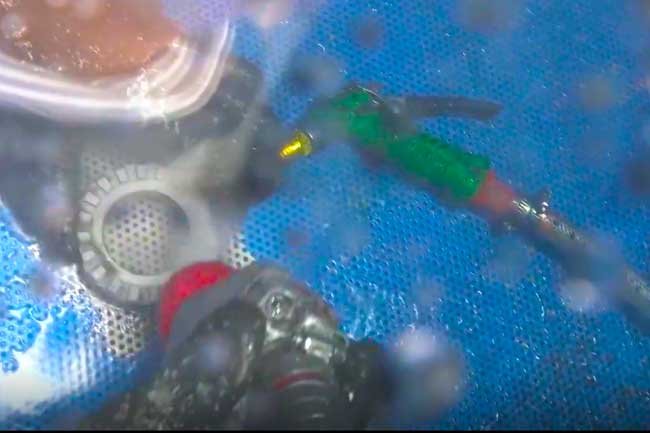
Repair and Remanufacture: Efficient for repairing and remanufacturing components.
Peening: Used for peening applications to enhance material properties.
Preparation for Bonding and Plating: Ideal for preparing surfaces for bonding and plating processes.
Cosmetic Finishing: Provides a precise and effective method for achieving cosmetic finishing.
Nuclear Decontamination: Well-suited for nuclear decontamination tasks.
Mold and Die Cleaning: Effective in cleaning molds and dies.
General Component Cleaning: Applicable for a wide range of general component cleaning needs.
5. Working Video
6. Is Wet / Vapor Blasting Better Than Sandblasting?
Wet / vapor blasting and sandblasting are both effective methods of surface preparation and cleaning, and the choice between the two methods depends on the specific application and the material being worked on. Here are some of the differences between wet blasting and sandblasting that can help you determine which method is better for your application:
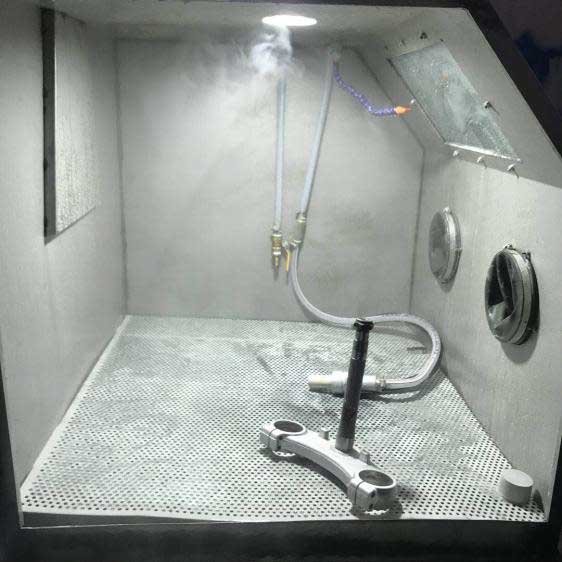
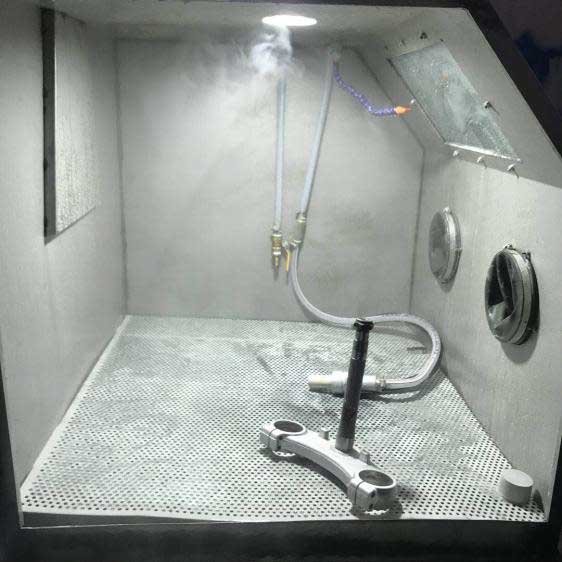
-
Dust generation: Sandblasting generates a large amount of dust and debris, which can be hazardous to the operator and the environment. Wet blasting, on the other hand, uses water to suppress dust and debris, resulting in a cleaner and safer working environment.
-
Surface damage: Sandblasting can be more aggressive than wet blasting and can sometimes cause damage to the surface being worked on. On the other hand, wet blasting is generally gentler and less likely to cause damage.
-
Rust removal: Wet blasting is often more effective than sandblasting at removing rust and other surface contaminants, as the water in the mixture helps to loosen and remove the contaminants.
-
Media consumption: Wet blasting uses less abrasive media than sandblasting, which can result in cost savings over time.
-
Eco-friendliness: Wet blasting is considered more environmentally friendly than sandblasting, as it generates less dust and debris and uses less abrasive media.
Overall, while both wet ice blasting and sandblasting have their advantages and disadvantages, wet blasting can be a better choice for certain applications where a gentler process is required, such as delicate or precision components. Wet blasting can also be a more environmentally friendly and cost-effective method, especially for larger or longer-term applications.
7. Basic Specification
Type | KY7070W | KY9080W | KY1010 | KY1212 | KY1610 |
---|---|---|---|---|---|
Working Area Size(mm) | 700*700*800 | 900*900*800 | 1000*1000*800 | 1200*1200*800 | 1600*1000*800 |
Air consumption | flow 0.5-1.1m3/min | flow 0.5-1.1m3/min | flow 0.5-1.1m3/min | flow 0.5-1.1m3/min | flow 0.5-1.1m3/min |
Blasting Gun | 1 wet gun & 1 boron cabide nozzle (4-8mm) | 1 wet gun & 1 boron cabide nozzle (4-8mm) | 1 wet gun & 1 boron cabide nozzle (4-8mm) | 1 wet gun & 1 boron cabide nozzle (4-8mm) | 1 wet gun & 1 boron cabide nozzle (4-8mm) |
Volume of abrasive & water | 25L | 25L | 25L | 25L | 25L |
Ration of Abrasive & Water | 1:3 | 1:3 | 1:3 | 1:3 | 1:3 |
- The technical data is not binding and may be subject to change.
- Depending on the type of parts, production method, etc., further machine types and measurement specification sheets upon request.
8. What Is the Best Media for Wet Blasting?
The choice of media for wet grit blasting can depend on several factors, such as the type of surface being blasted, the desired finish, and the equipment being used. However, some common media used for wet blasting include:
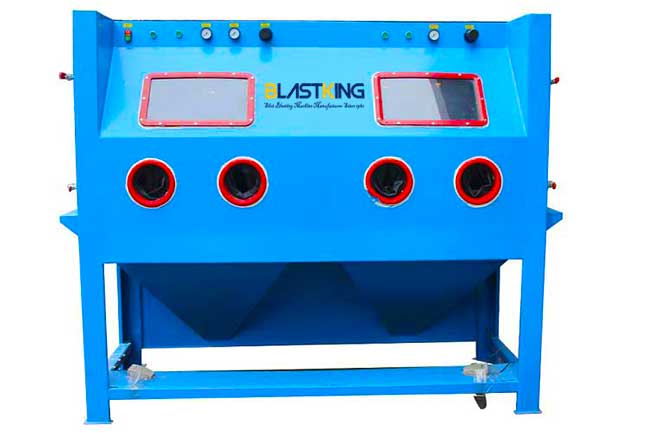
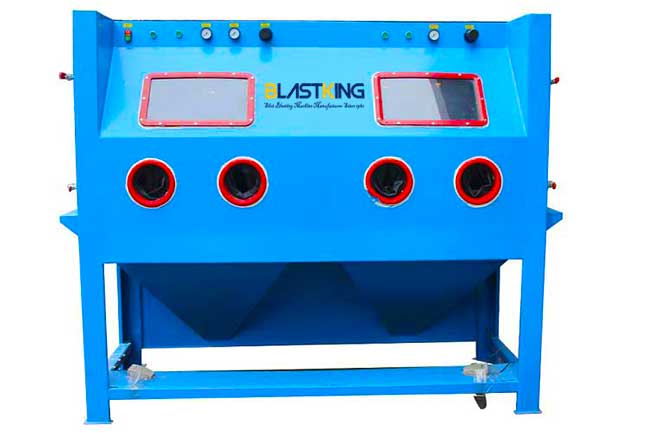
- Glass beads: Glass beads are a popular choice for wet blasting because they are non-toxic and leave a smooth finish on the surface. They are also reusable and can be used for multiple blast cycles.
- Aluminum oxide: Aluminum oxide is a durable and versatile media that can be used for a wide range of surfaces, including steel, aluminum, and other metals. It is also suitable for removing coatings, rust, and corrosion.
- Garnet: Garnet is a natural mineral that is often used for wet blasting. It is hard and angular, which makes it effective for removing tough coatings and rust. Garnet is also a low-dust option, which makes it safer and easier to use.
- Crushed glass: Crushed glass is an eco-friendly alternative to traditional abrasive media. It is made from recycled glass and is non-toxic. Crushed glass can be used for a variety of surfaces, including metal, concrete, and wood.
- Plastic media: Plastic media is a soft and gentle media used for delicate surfaces, such as automotive parts and plastics. It is also non-abrasive, which makes it a good option for cleaning without damaging the surface.
It’s important to note that the best media for wet blasting can vary depending on the application and equipment used. It’s always a good idea to consult a professional or equipment manufacturer for recommendations on the best media for your specific needs.
9. How to Choose the Right Vapor Blasting Machine?
Today, we’re diving into the crucial process of selecting the right machine for your job in the realm of vapor honing. This is a common question that often marks the beginning of a conversation with our customers. If you’re remotely interested in the vapor honing process, listen up – we’ve got valuable insights to share that will guide you in making the best choice.
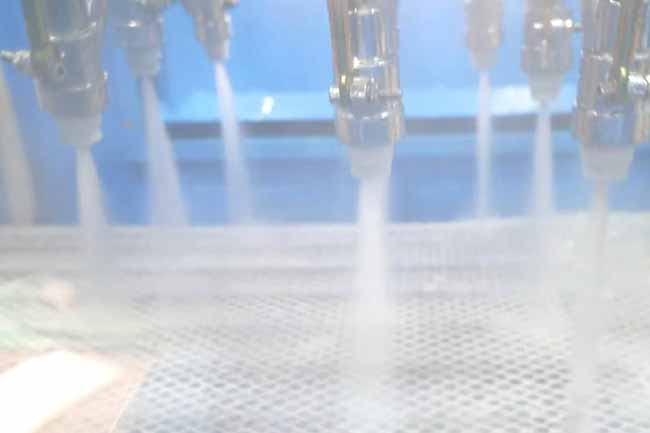
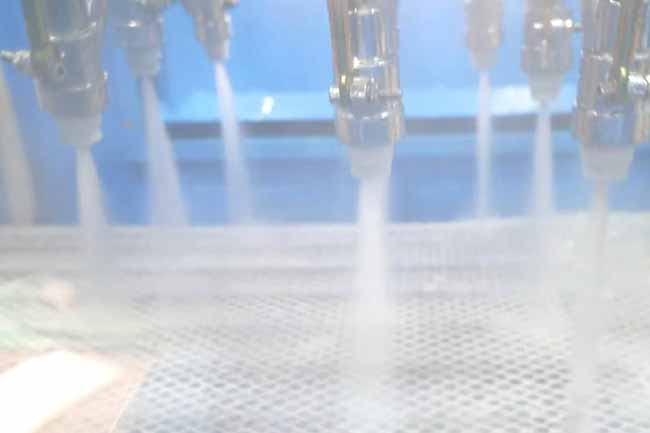
The first question we always pose to our customers is about the size of their parts. Understanding the dimensions of your parts is essential as it helps us determine the most suitable product for your needs. We offer a range of sizes and shapes, including manual versus automated wet cabinets. Determining the size of your parts is critical to avoid choosing a cabinet that’s either too small or too large for your requirements.
Following that, we inquire about the weight of the parts. Whether your parts are heavy or light plays a crucial role in narrowing down the options for the best-fitting cabinet.
Another key consideration is the frequency of your blasting and processing operations. Is it a daily, weekly, or monthly activity? Knowing the frequency helps us tailor our recommendations to ensure you get the most cost-effective and efficient solution.
Additionally, we may inquire about the number of people who will be using the cabinet. This might seem like an unusual question, but it matters. Different individuals may treat machinery differently, so understanding the user dynamics helps in recommending a product that aligns with durability and user behavior.
In summary, the four key factors to consider are part size, part weight, blasting frequency, and the number of users. These considerations ensure that you don’t overspend or underspend, getting you the best product for your specific needs. If you have further questions or need assistance, don’t hesitate to reach out to our sales team via email at market@blastkinggroup.com or give them a call. They’re always here and happy to help.
Get A Strong Partner at Your Side Now!
Consult your dedicated surface preparation equipment experts to make your business succeed!
Call us today at +86 135 8931 7685