What is a Table Type Shot Blaster: An Expert Guide
BlastKing table type shot blasting machines are typically used for small to medium-sized workpieces and are ideal for applications such as deburring, descaling, cleaning, and shot peening. They can be used in a variety of industries, including automotive, aerospace, foundry, and construction.
By Mathew Lee| Updated: January 25, 2025
Introduction
In the domain of surface preparation and cleaning, shot blasting is a common technique that utilizes abrasive materials to eliminate impurities and improve the quality of various surfaces. One such shot blaster is the table-type shot blaster, which has acquired popularity due to its efficiency and versatility. In this detailed guide, we will delve into the intricacies of table-type shot blasters, examining their features, applications, and benefits, among other things.
Get A Strong Partner at Your Side Now!
Get Your Instant QuoteBlastKing’s ability to improve your business profitability is based on more than 40 years’ experience and a spirit of innovation.
BlastKing Table Shot Blaster Features
Rotary table shot-blasting machines are equipment used to clean, prepare, and finish various workpieces. Here are some features of the rotary table shot blasting machines:
Rotary table: The primary feature of a rotary table shot blasting machine is a large rotating table that holds the workpieces. The table rotates continuously, allowing for the blast media’s complete and uniform coverage of the workpiece.
Blast wheel: The blast wheel is the primary component of the shot blasting machine. It uses centrifugal force to propel abrasive media at high velocity onto the workpiece to remove any contaminants or to create a desired finish.
Abrasive media: The abrasive media used in a rotary table shot blasting machine can vary depending on the material being processed and the desired finish. Typical media include steel shot, cut wire steel shot, aluminum shot, stainless steel shot, etc.
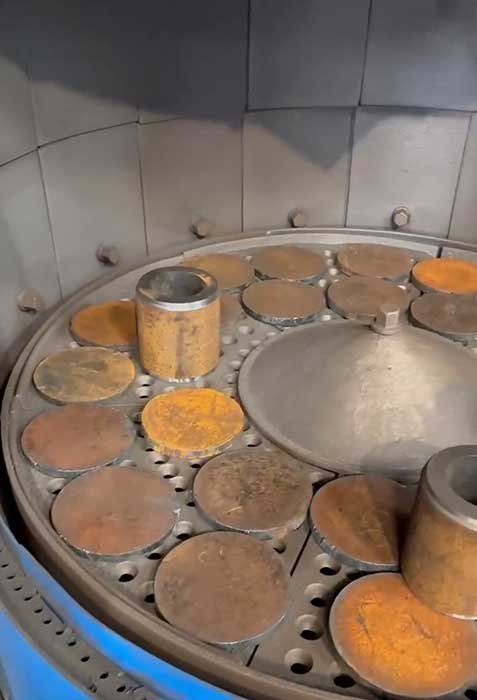
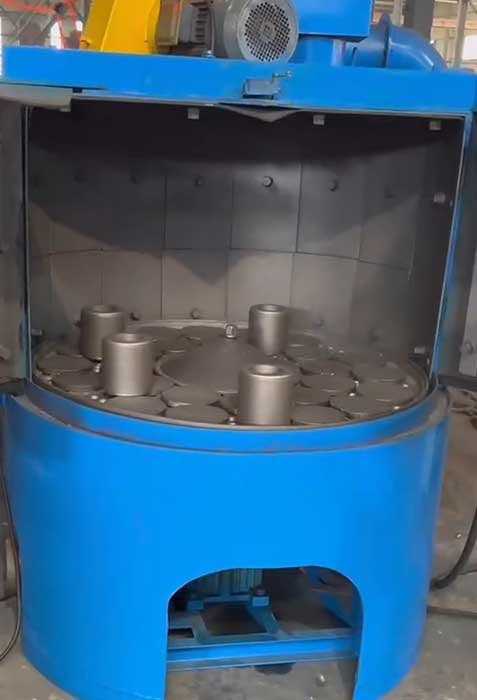
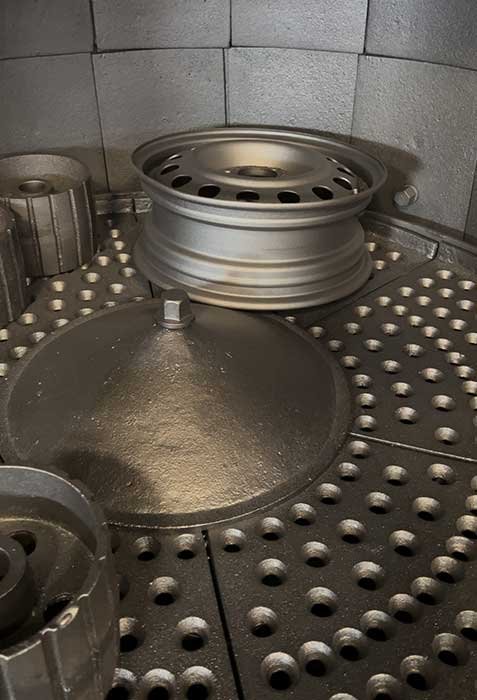
Dust collector: Shot blasting generates a lot of dust, which can be hazardous to workers and cause equipment damage. Rotary table shot blasting machines typically have a dust collector to capture and filter dust particles, ensuring a clean and safe working environment.
Control system: The control system of a rotary table shot blasting machine allows for easy adjustment of variables such as blast wheel speed, abrasive flow rate, and table speed. This allows the operator to customize the machine for different workpieces and surface finishes.
Safety features: Shot blasting machines can be dangerous if not operated correctly. Rotary table shot blasting machines typically have safety features, such as interlocks and guards, to protect operators from the hazards of the machine.
Automatic loading and unloading: Some rotary table shot blasting machines can be fully automated with automatic loading and unloading capabilities. This can increase productivity and reduce labor costs.
Overall, rotary table shot blasting machines are an efficient and effective solution for cleaning, preparing, and finishing various workpieces. They are ideal for the automotive, aerospace, and metal fabrication industries.
Table Blaster Application
The table-type shot blasting machine is suitable for surface cleaning and shot peening of multi-species, small batch castings, forgings, and steel structure parts. During the blasting process, it will remove the sticky sand, sand core, and oxide skin from the surface of the workpiece. It is also suitable for surface cleaning and peening of heat treatment parts.
Get A Strong Partner at Your Side Now!
Get Your Instant QuoteBlastKing’s ability to improve your business profitability is based on more than 40 years’ experience and a spirit of innovation.
We apply shot-blasting technology to achieve the purpose of rust removal and strengthening because shot-blast cleaning is still the most economical and reliable method in the world. Shot blasting has the following advantages over other cleaning technologies.
- Improve the fatigue resistance of mechanical products and metal components
- Eliminate stress concentrations
- Extend their service life
- Optimize the surface condition of the workpiece
- Greatly improve cleaning efficiency
- Reduce the labor intensity of cleaning work
- Reduce environmental pollution
This table shot blast machine is widely used in machinery manufacturing, engineering machinery, mining machinery, pressure vessels, automobiles, ships, and other industries to improve the appearance quality and surface process state of their product parts.
Composition & Structure
The rotary table shot blaster comprises a shot blast chamber, abrasive circulation and recovery system, blast wheel and abrasive dosing unit system, self-rotating mechanism, dust collecting system, and other components.
Shot Blasting Chamber
The chamber system welded structure consists of a chambered shell, chamber roof, interior protection liner, etc. The bottom of the chamber shell has an abrasive receiving plate welded around the chamber shell and coupled with the rotary table mechanism bracket. The chamber wall and half of the chamber roof are connected by bolts which are exceptionally convenient for loading parts and unloading workpieces from the top of the blasting chamber by crane or hoist system. The whole shot blasting shell is with high manganese protection liner, and the blasting wheels installed number, direction, and power could be optional according to the features of the workpieces.
Doors
The machine has a pair of sealed doors and a pneumatic top door. The inner side of the doors is equipped with a wear-resistant rubber shield. A baffle plate between the two sealed doors prevents the blasting media from flying out of the chamber.
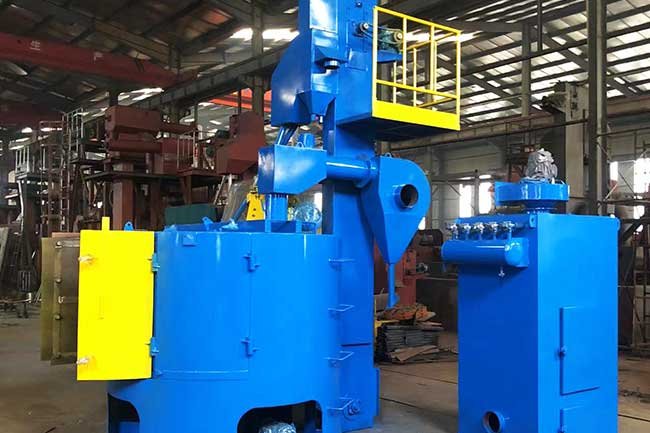
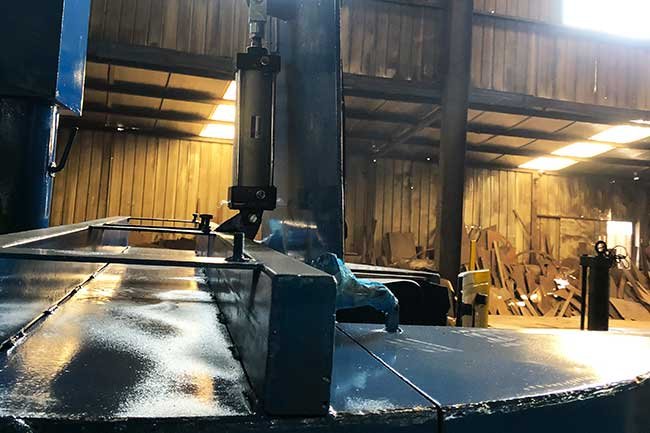
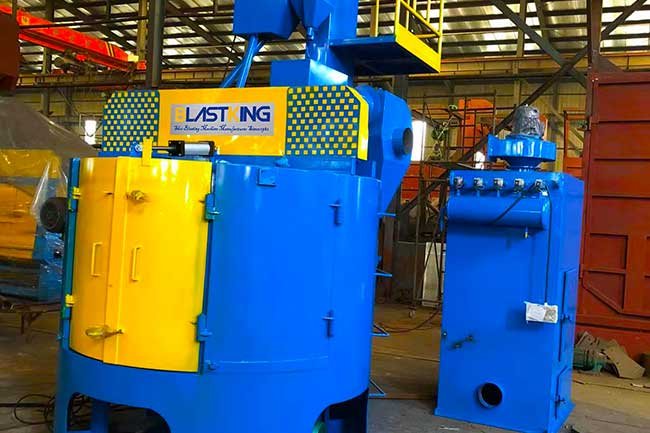
Abrasive Circulation & Recovery System
Abrasive circulation and purification systems can be divided into the circulation system and purification system, consisting of a bucket elevator, blasting media separator, abrasive dosing unit, abrasive feeding tube, etc.
Bucket Elevator
The bucket elevator comprises a cycloid reducer, upper and lower drum, conveying abrasion-resistant abrasion-resistant belt, hopper, closed barrel, and tightening device.
The bucket elevator gets material from the screw conveyor at the bottom and transports the material to the separator on top.
The elevator cover adopts a bending and forming welding structure with a beautiful appearance and good rigidity. There is an access door on the elevator cover, which can repair and replace the hopper. The end user can solve the blockage problem by opening the door cover on the lower hood shell at the bottom of the elevator.
This machine adopts an abrasion-resistant rubber belt conveyor. The buckets fixed on the conveying tape will scrape up the abrasive at the bottom of the elevator. The blasting media will be transported to the top of the elevator and dropped by centrifugal gravity to the separator.
The drum is made into a squirrel cage type to ensure that the conveying tape does not slip when working. This kind of structure not only improves the friction force between the lifting belt and the pulley, avoiding the slipping phenomenon of the old optical belt pulley, but also reduces the preload force of the lifting belt, helping to extend the service life of the lifting tape.
At the same time, the bucket elevator is equipped with a set of tightening devices. When the belt is loose, the operator can quickly pull the belt by adjusting the bolts on both sides of the upper part of the elevator. The adjustment range is 100mm.
Get A Strong Partner at Your Side Now!
Get Your Instant QuoteBlastKing’s ability to improve your business profitability is based on more than 40 years’ experience and a spirit of innovation.
Abrasive Purifying System - Separator
The RT series table blasting machine is a new product after improving technology and production process according to users’ requirements. It has the following advantages.
- The use of the popular pitless structure form, that is, to save the pit foundation construction costs and time, but also to solve the user due to the pit water storage caused by the elevator in the problem of rusting sand clumps.
- The large shot blasting volume and high blast speed of the internationally famous linear double-blade disc blast wheel. It can give the user excellent productivity and the best cleaning effect.
- The Blast principle diagram, blast chamber, and general diagram adopt advanced computer-aided design (CAD) drawing, and the blast wheels arrangement is more reasonable.
Rotary Table Mechanism
The rotary table is installed inside the chamber shell, and the sprocket drives its rotation. It is made of flat steel welded into a mesh disc with a perforated high manganese plate on the surface, which can withstand the wear and tear of high-speed abrasives throwing and prevent large pieces of materials from falling into the chassis. In addition, the bottom of the rotary table is equipped with a scraping plate. This is to collect the abrasives falling on the chassis and flow into the bucket elevator through the chute.
The cycloid reducer drives the power to drive the gear reducer, and then the energy is transferred to the rotary table through a pair of sprockets. Before the rotary table stops rotating, the abrasive dosing unit should be closed first to stop the blasting media supply and avoid the turntable’s Localized wear and tear.
Get A Strong Partner at Your Side Now!
Consult your dedicated surface preparation equipment experts to make your business succeed!
Call us today at +86 135 8931 7685