1. What Is An Air Blast Cabinet?
An air blast cabinet is a dedicated enclosure designed for the cleaning, finishing, or etching of surfaces using abrasive materials propelled by compressed air. These cabinets are equipped with either suction or pressure blast systems, offering versatility in their applications.
These durable sandblasting cabinets are versatile tools that allow you to accomplish various tasks, such as smoothing surface imperfections and eliminating foreign substances like carbon from pistons, all without impacting tolerances. With the flexibility to adjust air pressure and blast media, these cabinets enable quicker and more precise surface finishing compared to alternative methods.
Smartline blasting cabinets offer the option of either suction or pressure blast systems, with the latter being the preferred choice for enhanced production speed and precise control of media at both high and low operating pressures. They come in seven different sizes and come equipped with standard features that contribute to cost savings in both operation and maintenance.
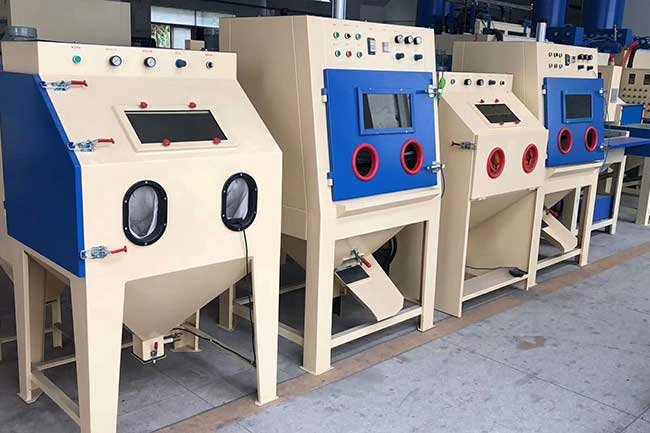
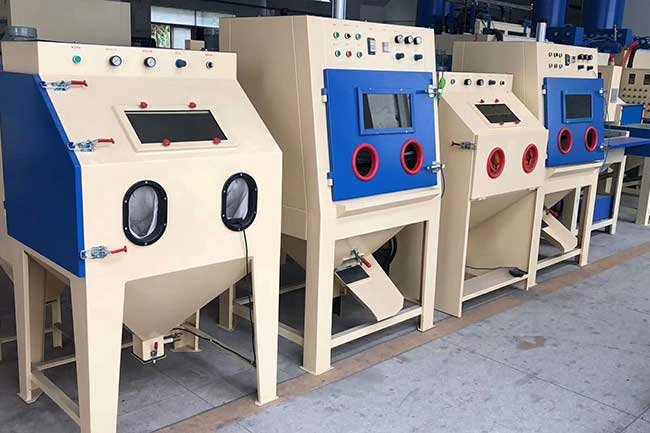
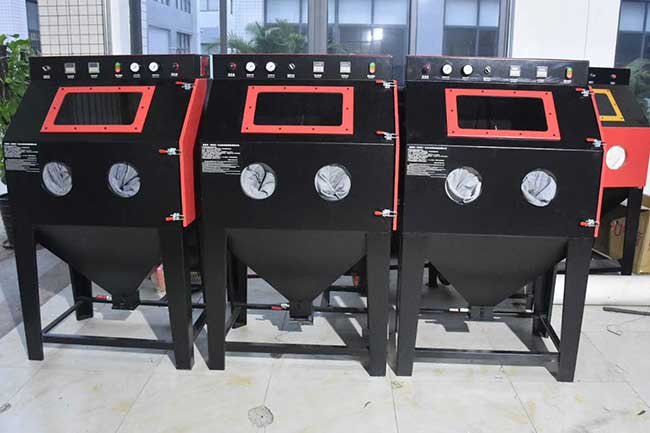
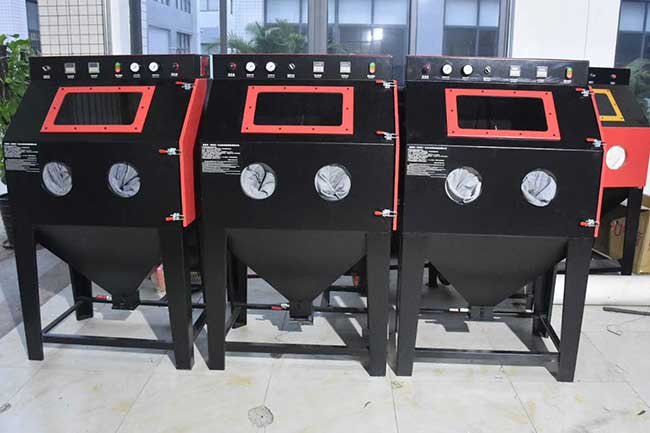
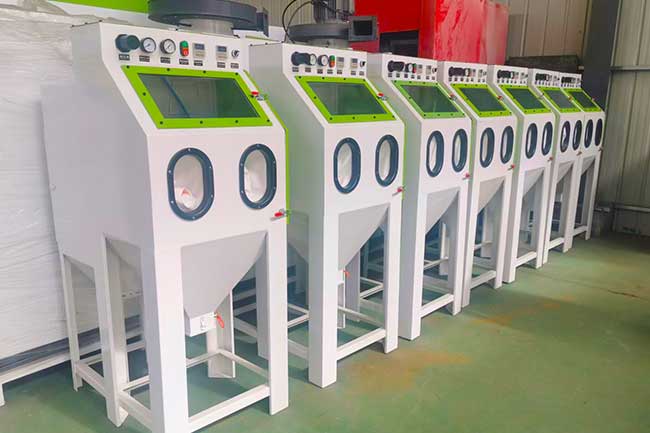
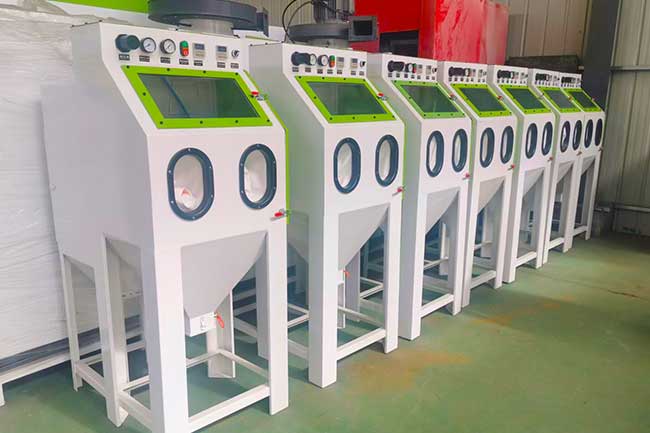


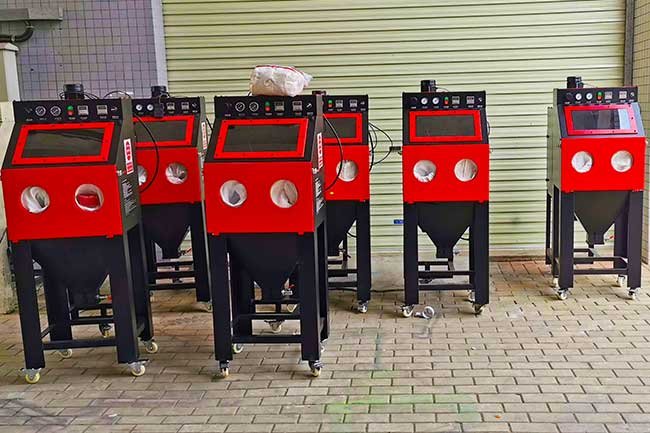
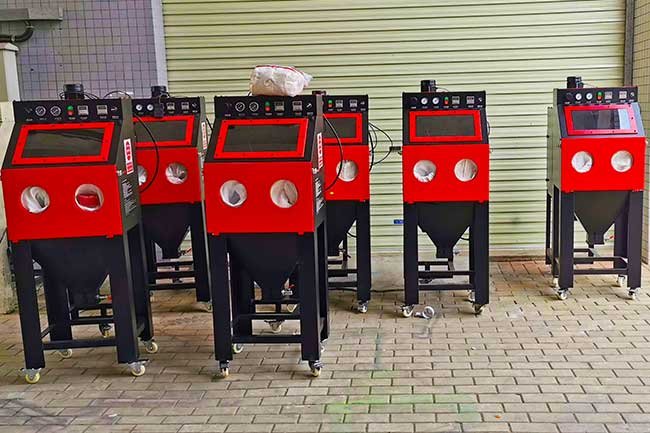
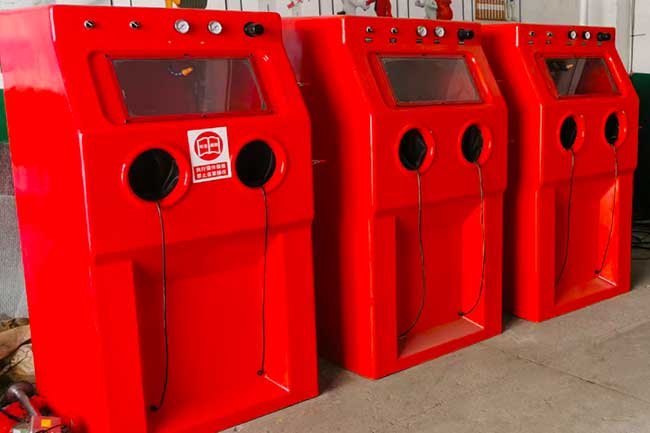
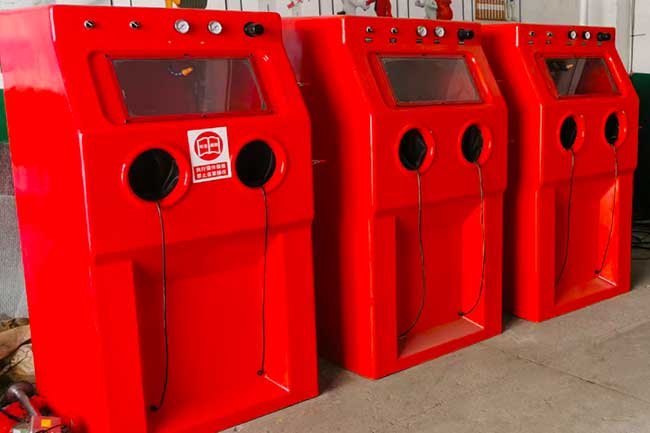
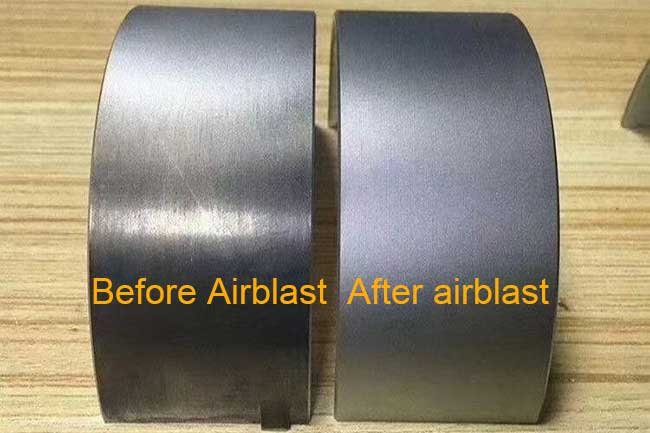
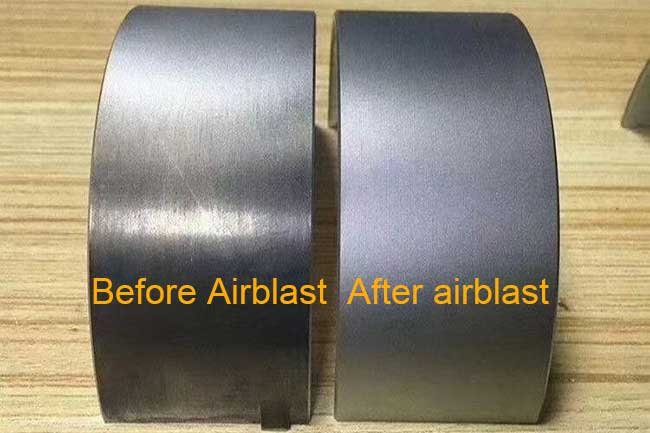
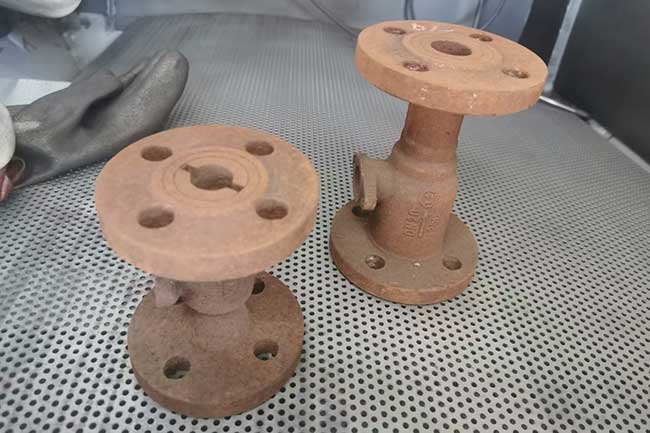
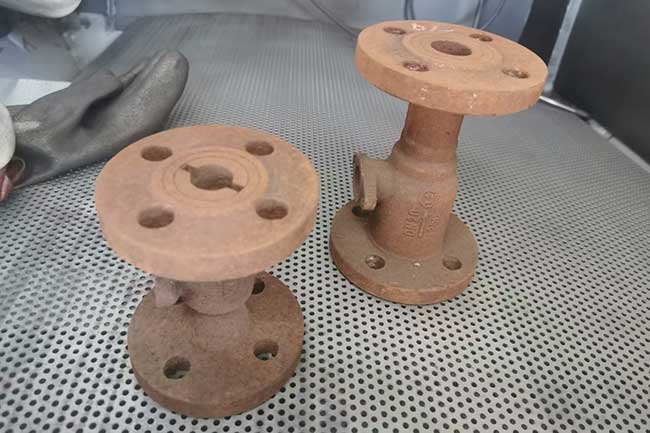
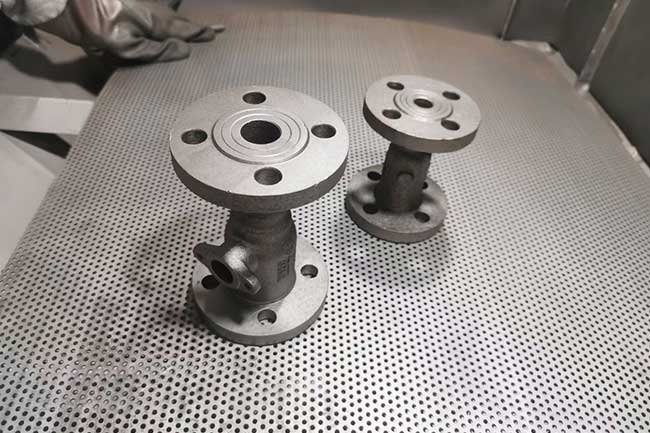
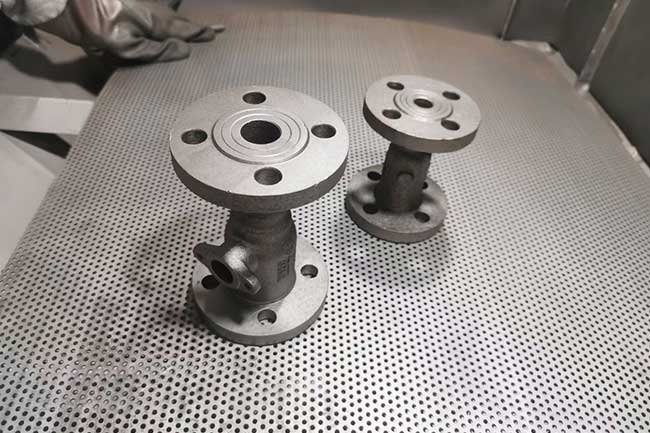
2. Features
- Low noise levels
- High ventilation rate for excellent visibility
- Compact external dimensions
- Robust construction for durability
- Large viewing window suitable for a variety of operator heights
- Reverse jet dust collector with automatic pulsing
- Elliptical glove ports accommodating a wide range of operator heights
- Internal blow down gun for convenience
- Anti-static gauntlets for safety
- Adjustable feed valve for precise and even abrasive feeding
3. Applications
These sandblasting cabinets are versatile and can be used for various applications, including:
- Cosmetic finishing
- Mould cleaning
- Preparation for painting, bonding, and plating
- Corrosion removal
- General component cleaning
- Rust and heat scale removal
- Surface texturing
The cabinets are suitable for a wide range of tasks, providing an effective solution for different finishing, cleaning, and preparation needs.
4. Considerations for Choosing an Air Blast Cabinet
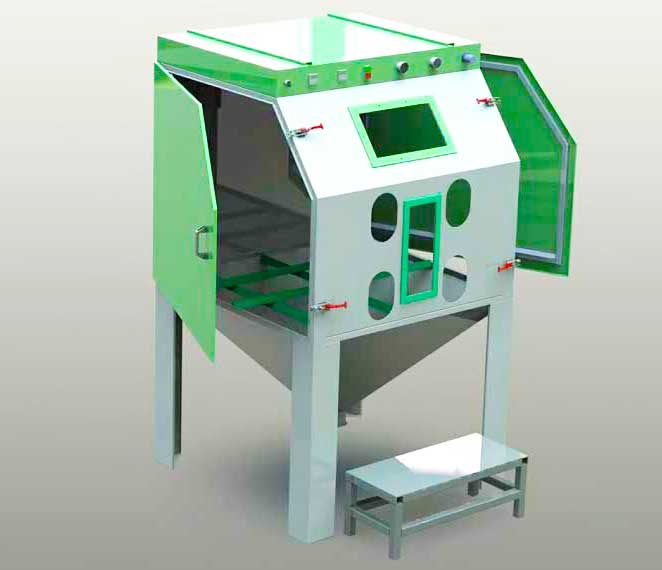
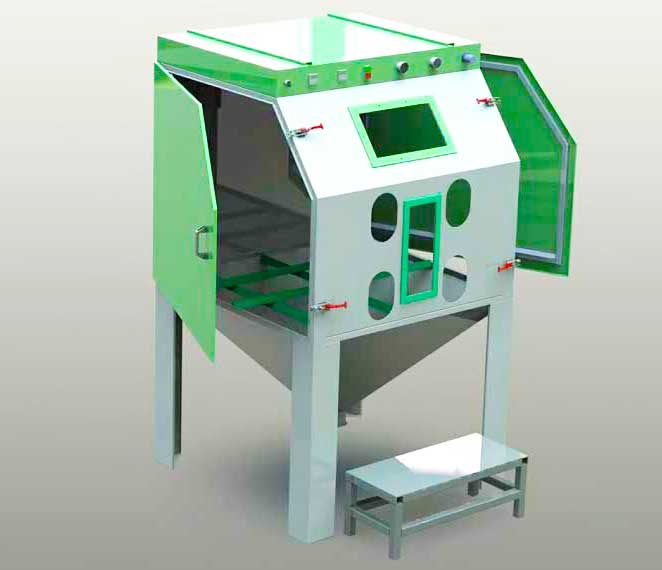
1.Material Compatibility:
- Ensure compatibility with the materials you’ll be working with.
- Certain materials may necessitate specific abrasive media or cabinet features.
2. Size and Capacity:
- Determine the appropriate size and capacity for your projects.
- Oversized or undersized cabinets can impact efficiency and lead to unnecessary expenses.
3. Dust Collection System:
- Prioritize an efficient dust collection system.
- This is crucial for maintaining a clean workspace and preventing potential health hazards.
4. Abrasive Media:
- Different applications may require specific types of abrasive media.
- Choose a cabinet that accommodates the abrasive media suitable for your particular projects.
5. Working Video
6. Key Components
7. Basic Specification
Type | KY6050 | KY9060 | KY9080 | KY1010 | KY1212 |
---|---|---|---|---|---|
Cabinet Innner Length | 600 | 900 | 900 | 1000 | 1200 |
Cabinet Inner Width | 500 | 600 | 800 | 1000 | 1200 |
Cabinet Inner Height | 550 | 600 | 650 | 700 | 800 |
- The technical data is not binding and may be subject to change.
- Depending on the type of parts, production method, etc., further machine types and measurement specification sheets upon request.
8. BlastKing Provides A Range of Custom Blast Cabinets
When standard blast cabinets fall short of meeting your needs, BlastKing steps in with tailored solutions. Whether you require a fully or partly automated cabinet or one crafted to precise dimensions, we’ve got you covered. Our expertise extends beyond conventional applications; for instance, we’ve collaborated with a fashion design firm to automate the production of “distressed-look” jeans using our blast cabinets. With BlastKing, the possibilities are limitless. Reach out to our experts today to discuss your unique requirements and explore the diverse range of customized solutions we offer.
Boost Productivity: Streamline Operations with Cutting-Edge Sand Blasting Cabinets!
Ready to revolutionize your surface treatment process? Take the first step towards efficiency and quality – order your Blasting Cabinet today!
Call us today at +86 135 8931 7685
9. FAQs (Frequently Asked Questions)
Q1: How Do Abrasive Blast Cabinets Work?
An abrasive blast cabinet functions as a self-contained system, facilitating the precise removal of paint or debris from various parts. Essentially, it comprises enclosed metal structures with strategically placed openings, windows, and integrated equipment designed for the utilization of abrasive media like sand. Through the application of compressed air, these cabinets propel a wide array of loose grains or abrasive materials, achieving diverse outcomes such as polishing, cleaning, deburring, texturing, and surface removal.
Operators engage with the parts within the cabinet by inserting their arms into specialized gloves attached to designated ports. Additionally, they can observe the workpiece through viewing windows and control the cabinet’s operation using a bottom pedal or treadle mechanism for convenient on/off functionality.
Q2: What Factors Should Be Considered When Choosing an Abrasive Blast Cabinet?
To ensure you choose the most appropriate abrasive blast cabinet for your specific application, it’s crucial to weigh several factors before making a decision. Here’s a breakdown of key considerations:
Types of Blasting Systems:
- Blasting Cabinet: Utilizes a gun to draw abrasive media into the nozzle, suitable for light production, basic cleaning, and occasional use. Requires higher air pressure.
- Direct-Pressure Cabinet: Dislodges abrasive media at a higher blasting flow rate, allowing adjustment of pressure for varying tasks.
Types of Manual Abrasive Blast Cabinets:
- Standard Hand Cabinets: Available in various configurations, suitable for small to medium-sized components.
- Modified Hand Cabinets: Economically tailored to meet specific customer needs, reducing lead times over custom-engineered equipment.
Coverage Area:
The size of your compressor determines the coverage area. Larger compressors accommodate larger blast nozzle sizes, resulting in more coverage in less time. Cabinet size should match the workload, considering simultaneous or individual piece processing.
Types of Airflow:
- Propelling System: Produces airflow to direct abrasives onto the surface.
- Exhaust Mechanism: Clears dust particles and pollutants from the cabinet to prevent screen clogging.
Price:
Consider the cost relative to the quality of materials used for blasting and cabinet construction. Cheaper options may compromise performance and durability. Ensure the price reflects the cabinet’s size and the quality of components like valves, tubing, and nozzles for optimal results.
Q3: What Is Abrasive Blasting?
Abrasive blasting involves the process of directing a high-pressure stream of abrasive material onto a surface to either smooth or roughen it, as well as to aid in shaping or removing particles, dust, and contaminants.
A typical abrasive blasting system comprises three key components: an abrasive container or blasting pot, a propelling device, and a blasting nozzle. Together, these components facilitate the cleaning or removal process while ensuring the integrity of the surface being treated.
Abrasive blasting techniques vary depending on the type of abrasive material used. Some of the most common forms include:
-
Pressure/Suction Blasting: This method involves using either pressure or suction to propel abrasive material onto the surface for cleaning or preparation.
-
Wet Blasting: In wet blasting, water is mixed with the abrasive material to reduce dust and heat generated during the process, resulting in a gentler treatment of the surface.
-
Soda Blasting: Soda blasting employs sodium bicarbonate (baking soda) as the abrasive material, making it a non-destructive and environmentally friendly option suitable for delicate surfaces.
-
Bead Blasting: Bead blasting utilizes small spherical beads as the abrasive material, often preferred for achieving a uniform finish on metal surfaces.
-
Dry-Ice Blasting: Dry-ice blasting involves propelling pellets of dry ice (solid carbon dioxide) at high speeds to clean or prepare surfaces without leaving behind any residue.
-
Centrifugal Blasting: In centrifugal blasting, abrasive material is propelled by centrifugal force generated by a rapidly rotating wheel or disk, offering a controlled and efficient surface treatment method.
Each of these abrasive blasting methods offers unique advantages and is selected based on factors such as the type of surface being treated, the desired finish, and environmental considerations.
-
Q4: What Are the Advantages of Abrasive Blasting?
Abrasive blasting stands out as the most efficient and cost-effective technique for surface cleaning and coating preparation. It offers numerous advantages over alternative methods, such as chemical cleaning, notably due to its ability to be executed within a controlled environment.
Here are some key benefits of utilizing abrasive blasting for surface cleaning:
-
Enhanced Efficiency: Abrasive blasting ensures swift and thorough removal of unwanted contaminants, resulting in a faster and more effective cleaning process.
-
Preservation of Material Integrity: This technique guarantees the integrity of the underlying material, minimizing the risk of damage during the cleaning and preparation process.
-
Climate Control Systems: Abrasive blasting setups often incorporate climate control systems, maintaining optimal conditions for surface preparation before coating application.
-
Reusable Abrasive Media: The abrasive media used in blasting can be reused multiple times, reducing the need for frequent replacement and lowering overall costs.
-
Reduced Recleaning and Recoating Needs: By effectively removing contaminants and preparing the surface for coating, abrasive blasting lessens the necessity for costly recleaning and recoating processes.
-
Environmental Friendliness: Compared to chemical cleaning methods, abrasive blasting is considered more environmentally friendly, as it minimizes the use of harmful chemicals and reduces hazardous waste generation.
-
Prevention of Coating Issues: Abrasive blasting helps prevent common coating problems like blistering and delamination by thoroughly cleaning and preparing the surface, ensuring optimal adhesion of the coating material.
-
Q5: What Are The Common Applications of Manual Blast Cabinets?
When selecting the appropriate blast cabinet, it’s crucial to prioritize the application over mere size compatibility with the part. Here’s a breakdown of common abrasive blasting applications and the corresponding cabinets:
-
Industrial Use: Typically associated with production equipment utilized in manufacturing facilities, industrial applications demand cabinets equipped with dust collectors tailored to the active machining duty cycle and abrasive type. These cabinets are designed to withstand the rigors of continuous operation in industrial settings.
-
Shop Use: For shop applications, convenience takes precedence over speed. Operators prioritize the ease of use of blasting cabinets over the time and effort required to clean parts thoroughly. Cabinets commonly found in both large and small shops are ideal for maintenance and repair tasks, catering to intermittent or infrequent usage patterns.
-
Home Use: Optimal results in home-use blast cabinets are achieved with the inclusion of an appropriate dust collector, a separator reclaimer, and a flow rate exceeding six cubic feet per minute (CFM). While these systems can effectively clean parts when used correctly, they are best suited for processing small, hand-held components within 3 to 4 minutes.
-
Hobby Use: Blast cabinets designed for hobbyists typically feature light-duty construction and consist of a basic box structure with a window and glove ports. To ensure optimal performance, hobbyist cabinets should be equipped with a trigger gun boasting high-quality in-cabinet lighting and a viewing window. Additionally, essential components such as a foot-operated blasting gun, a dust collector, an abrasive mixing valve, a separator reclaimer, and air controls contribute to a fulfilling hobbyist blasting experience.
-
Q6: Why BlastKing Abrasive Equipment?
At BlastKing Abrasive Equipment, our commitment lies in offering a diverse range of reliable products and blast systems that consistently surpass the expectations of our valued customers. Moreover, we take great pride in our cutting-edge facility situated in Qingdao City, China, which boasts a fully-equipped testing laboratory and an expansive product demonstration area. These spaces are equipped with comprehensive prototyping, validation, and process development machinery, ensuring thorough and precise evaluations.
In addition to ensuring product and service availability, we go the extra mile by providing comprehensive support to our clientele. This includes offering training programs, technical assistance, turnkey installation services, and laboratory testing for our equipment. Furthermore, the adept and seasoned team at BlastKing is dedicated to offering personalized consultations and design recommendations, collaborating closely with our customers to craft optimal solutions tailored to their specific requirements.
Get A Strong Partner at Your Side Now!
Consult your dedicated surface preparation equipment experts to make your business succeed!
Call us today at +86 135 8931 7685