Shot Blasting and Primer Painting Machine Revolutionize Your Workflow!
Updated: August 13, 2025
Are you tired of the tedious and time-consuming process of preparing surfaces for painting or coating? Say hello to a game-changer in surface treatment technology: our automated shot blasting line.
Outline
1. What Is Shot Blasting and Primer Painting Line?
Shot Blasting and Primer Painting Lines are primarily employed for safeguarding steel products against corrosion. These preservation lines integrate heating (drying), blasting, coating, and drying processes for various workpieces like sheet steel, profiles, pipes, or steel structures within a single automated line.
They prove particularly advantageous when there’s a considerable gap between the blasting and final coating stages during manufacturing or storage. To prevent rust reformation, a weld primer is applied, offering corrosion resistance for several weeks.
These lines can accommodate sheet widths of up to 5000mm, with passage speeds ranging from 1.0m/min to 8.0m/min.
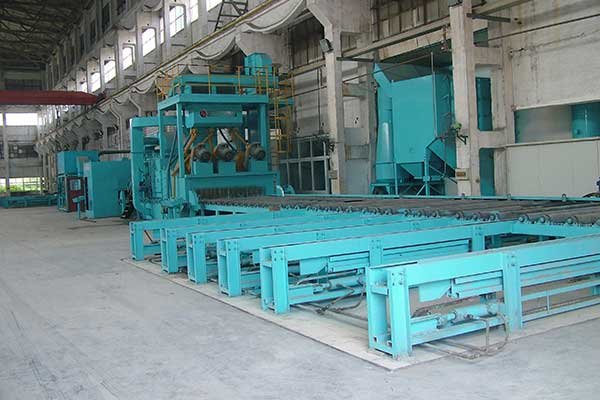
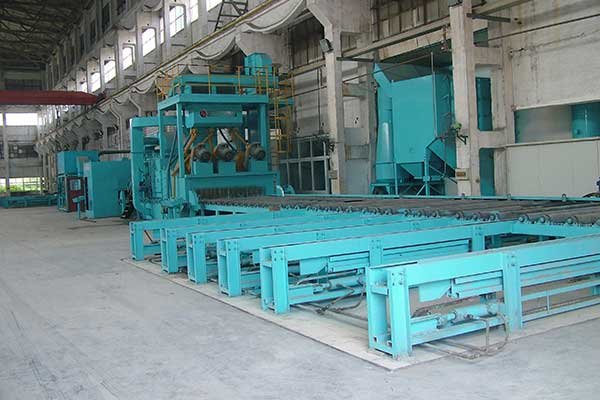
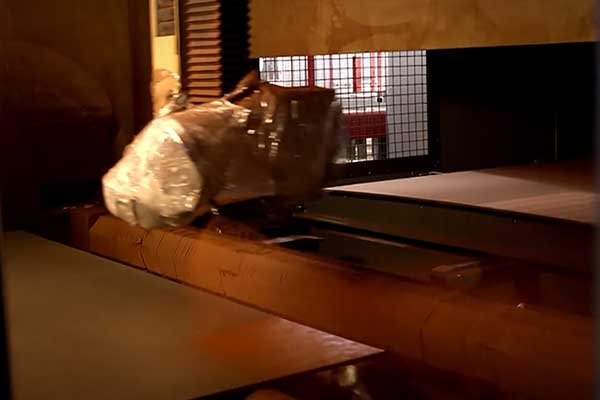
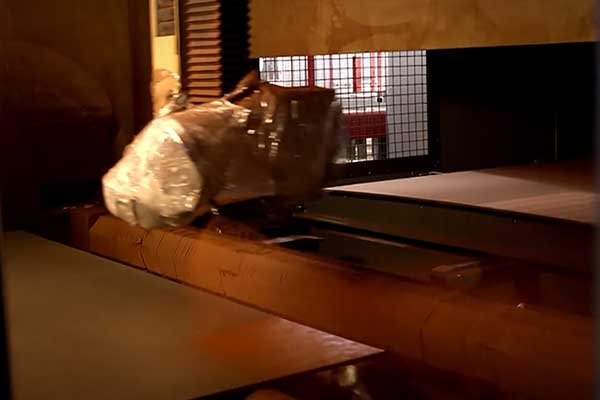
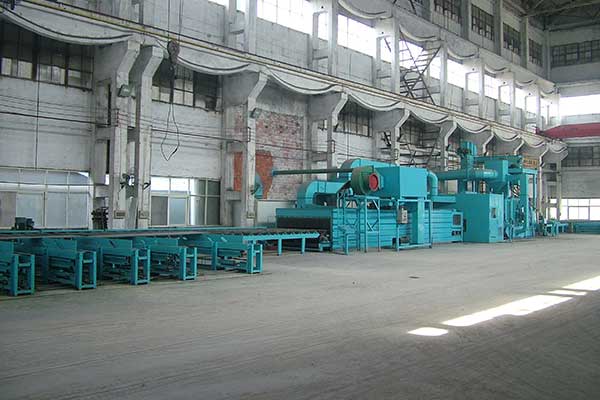
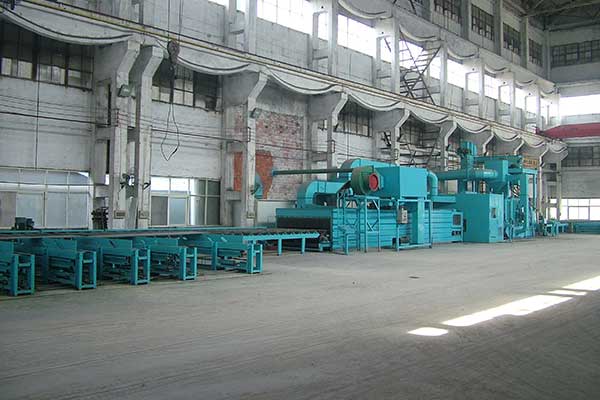
2. Features
- Complete systems quoted
- One supplier for all components
- Proven abilities – The industry leader
- Quality components
- Proven technology
- Custom designs – Flexible layouts
- Simple integration into existing manufacturing processes
- Wide range of system sizes and variants
3. Applications
For the treatment of plates, beams, and profiles in the steel manufacturing, construction, and processing industry.
- Removal of mill and forge scale and rust
- Increase of surface roughness
- Corrosion removal
- Rust and heat scale removal
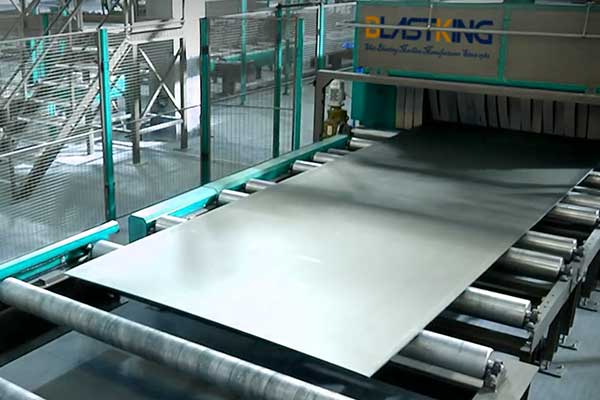
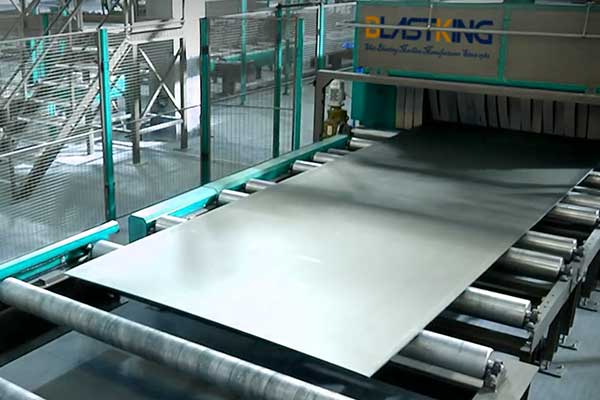
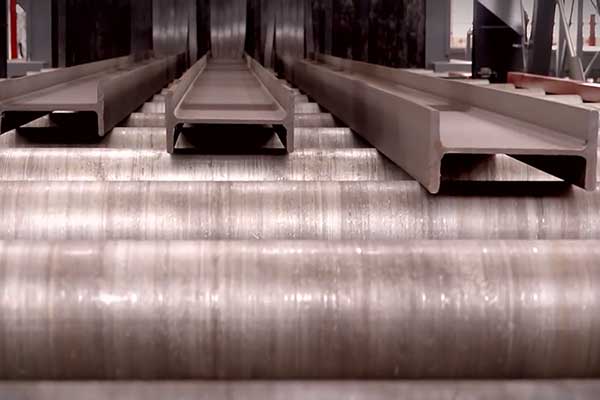
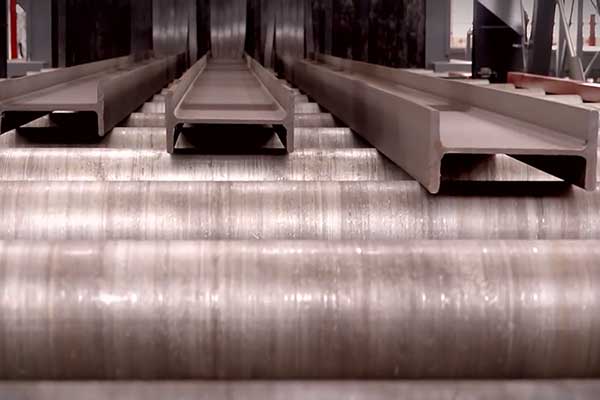
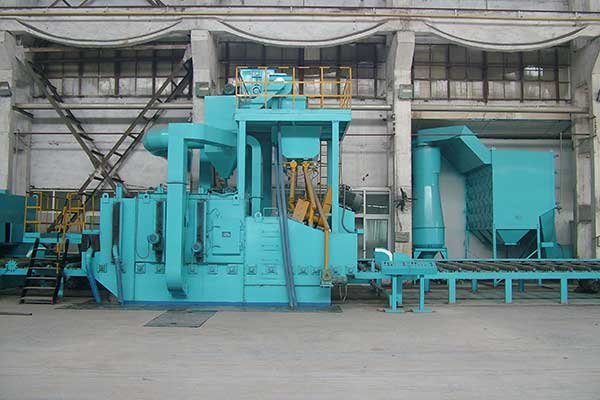
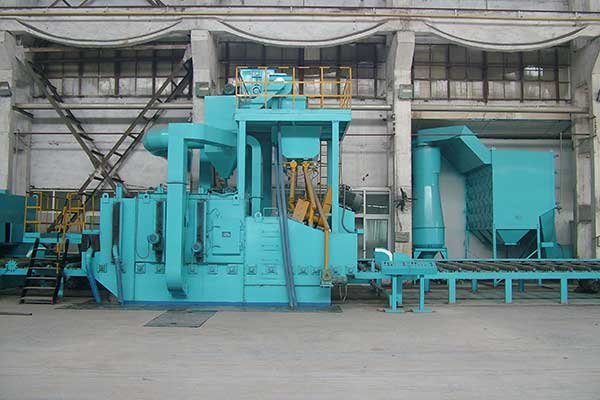
4. Key to Fully Automated Preservation Line
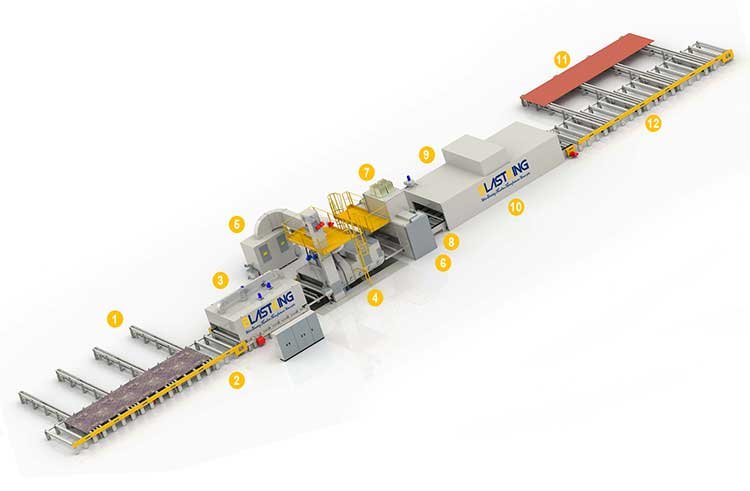
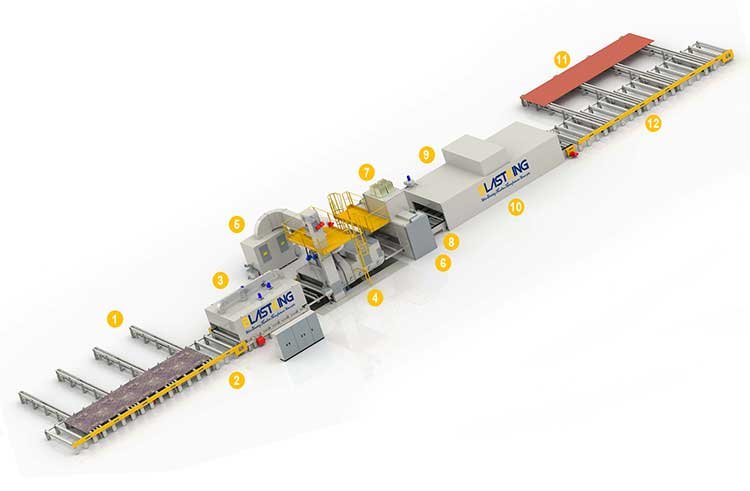
- Cross transfer conveyor
- Inlet roller conveyor
- Pre-heater
- Roller conveyor shot blast machine
- Blast machine filter
- Paint spray chamber
- Paint chamber filter
- Slat conveyor
- Heating system
- Drying chamber
- Cross transfer conveyor
- Outlet roller table
Unleash Efficiency: Shot Blasting and Primer Coating Machine Revolutionize Your Workflow!
Tired of labor-intensive surface preparation methods that drain your time and resources?
Imagine effortlessly achieving pristine surfaces with our innovative shot blasting and primer painting machines.
Say goodbye to delays, rework, and inefficiencies, and welcome increased productivity and higher-quality finishes.
Call us today at +86 135 8931 7685
5. Key Benefits
6. The Shot Blasting and Painting Line Working Process
The shot blasting and painting line follows a specific working process. Initially, the workpieces are conveyed along the inlet roller conveyor into the shot blasting chamber. Once shot blasting is complete, the workpieces proceed into the clean chamber where they undergo cleaning to remove blasting media and contaminants using brushes, a reclaim screw conveyor, and a high-pressure fan.
After the cleaning process, a coating is applied in the spray chamber, and the finished workpieces are then transported into the drying chamber. A slat conveyor facilitates the movement of the parts towards the outlet roller table. At this stage, they are either removed from the line or fed into a downstream logistics system via the cross-transfer conveyor.
Elevate Quality Standards: Achieve Flawless Finishes with Our State-of-the-Art Shot Blasting and Primer Painting Machine!
Whether you’re in manufacturing, construction, or automotive industries, our machine caters to your needs, ensuring efficiency, precision, and reliability.
Call us today at +86 135 8931 7685
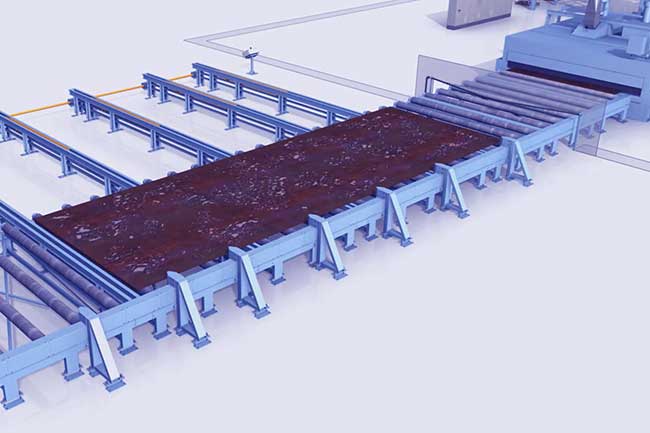
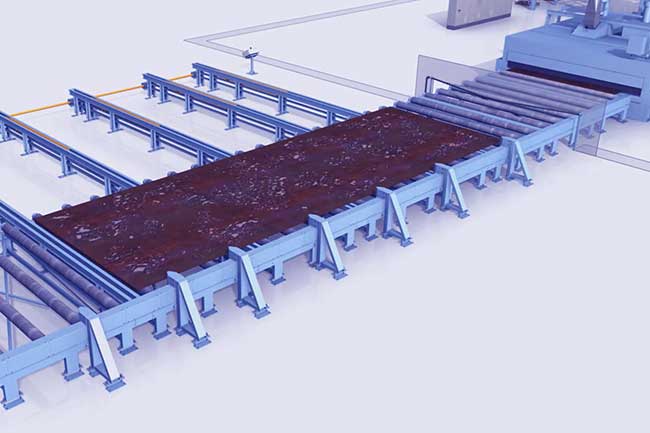
6.1 Transport Systems
Transport systems for industrial applications encompass various types of conveyors and handling equipment tailored to specific needs. Examples include roller conveyors, chain conveyors (slat conveyors), conveyors dedicated to the painting section, cross conveyors known as “lift and go” systems, fork conveyors, shuttle conveyors, drives, and controls designed for automatic conveyor lines. Additionally, there are parts turning and collecting systems tailored specifically for welding constructions and tubes.
6.2 Shot blast systems
The roller conveyor shot blast systems play a crucial role in the complete shot blasting and primer coating line. Components such as large steel sheets, tubes, round bars, angle bars, and I-beams are transported on a roller conveyor through several stages including the pre-heater chamber, blast chamber, and a blow-off/brush-off station.
Mounted onto the machine housing, the high-performance blast wheels ensure thorough and consistent blast coverage of the parts. This process optimally prepares the surface of the parts for the subsequent primer coating, ensuring effective corrosion protection and enhancing the overall quality of the finished products.
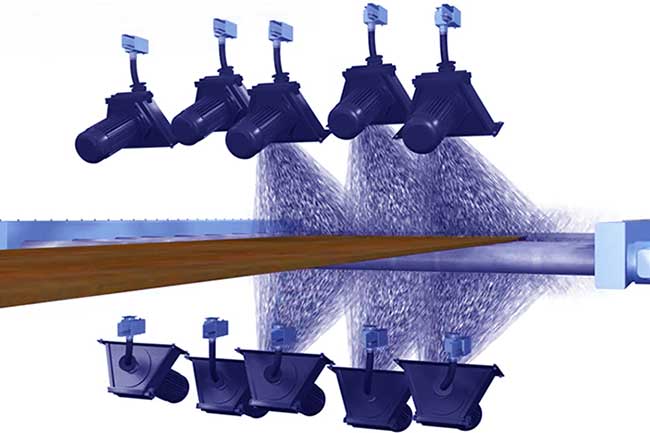
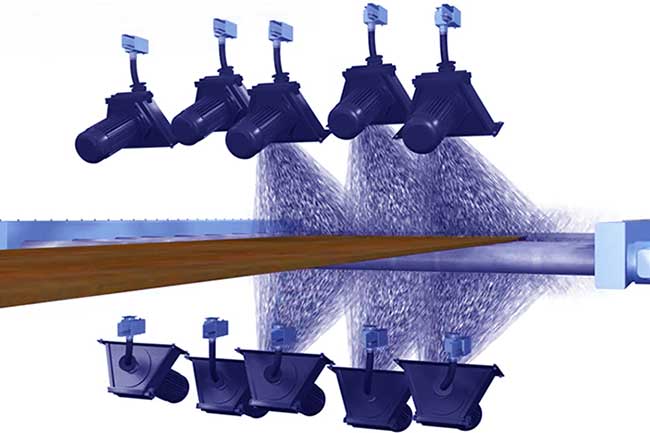
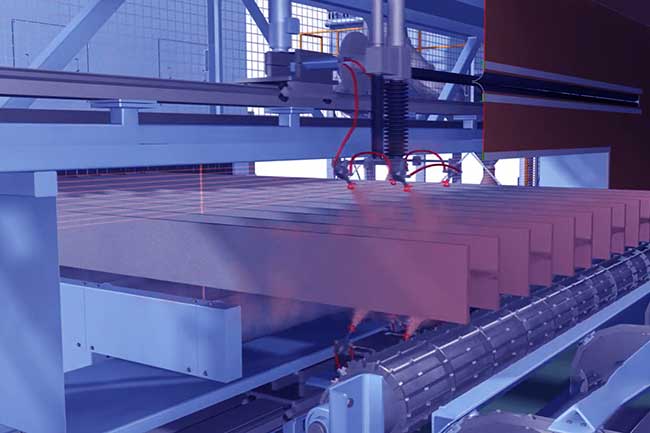
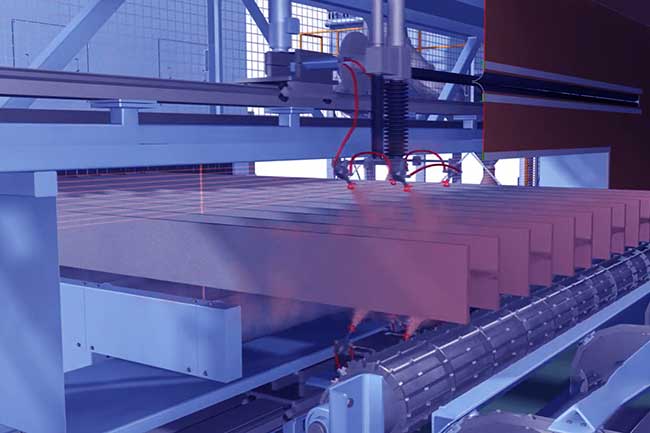
6.3 Paint Spray Chamber
The paint spray chamber automatically identifies the various plate and profile widths, applying a continuous coating process with a weld-primer thickness ranging from approximately 15 to 25 micrometers (μm).
To address environmental concerns, paint dust and solvents (if non-water-based paint is utilized) undergo treatment in accordance with local regulations. This treatment typically involves passing them through an automatic filter unit and a paint mist treatment plant.
6.4 Drying chamber & slat conveyor
In this area, the preserved steel plates and profiles undergo continuous drying. Workpieces are conveyed through the drying chamber using a slat conveyor. To minimize contamination from overspray, there is a considerable distance between the spray zone and the slat conveyor. Additionally, an elevating roller is strategically positioned upstream to address height discrepancies and ensure smooth transfer of thin plates onto the conveyor cross slats, thus preventing bending. The plates are supported only by the contact points of the conveyor cross slats, minimizing contact with the workpiece and preserving the wet primer.
The length of the drying chamber varies based on factors such as the type of paint, coating thickness, and passage speed.
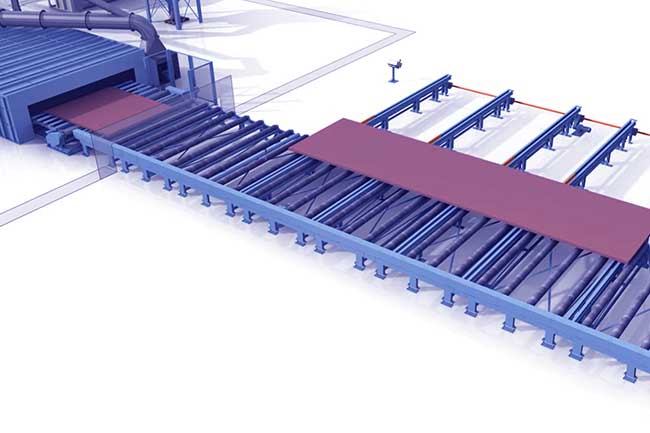
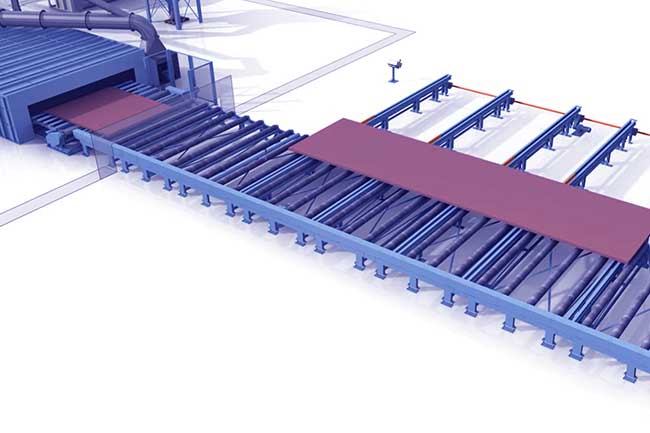
7. Working Video
8. Conclusion
The protection of sheet metal and profiles with a thin layer of primer during storage and processing, followed by the application of primer before the final paint coating. The process, which involves cleaning rusted surfaces in an automated roller conveyor shot blasting machine and applying primer in an automatic painting chamber, is automated, enabling cost-effective results for large quantities with quality protection. Generally, the line comprises a hydraulic loading device, longitudinal roller conveyor, moisture drying chamber, through-feed cleaning machine, machine dust filter, primer painting chamber with cross painting robots, slat conveyor, and hydraulic unloading device. Depending on technological needs, the line can be integrated into other lines combining operations such as straightening, cutting, welding, final painting, etc. Proper selection of primer allows for subsequent welding and extended material storage.
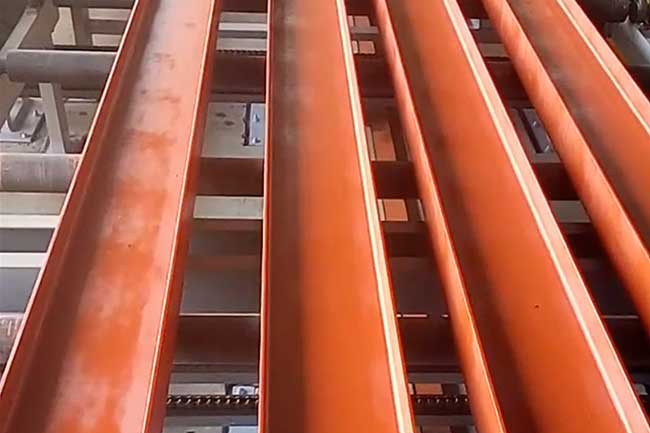
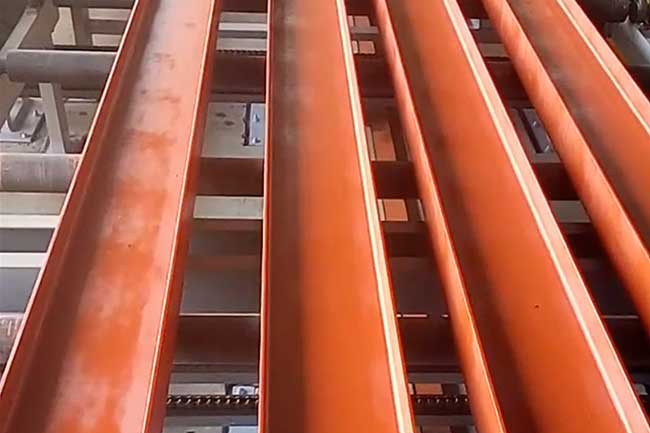
Get A Strong Partner at Your Side Now!
Consult your dedicated surface preparation equipment experts to make your business succeed!
Call us today at +86 135 8931 7685