Wire Mesh Belt Shot Blasting Machine: Efficiency Unleashed
Updated: August 13, 2025
Boost your production quality with BlastKing’s Mesh Belt Shot Blasting Machine—designed for continuous, energy-efficient operation and superior surface finishes in automotive, aerospace, and heavy industries.
Outline
1. Introduction
Are you looking for a reliable way to clean or strengthen metal parts? At BlastKing, we’ve been perfecting our wire mesh belt shot blasting machines since 1982. These machines provide continuous, efficient, and consistent treatment for a wide range of components.
Below, you’ll find a clear breakdown of our system. We keep it straightforward. We also sprinkle in a bit of mild humor because work shouldn’t feel like watching paint dry!
What exactly does a wire mesh belt shot blasting machine do?
Our wire mesh belt shot blasting machine cleans, descales, deburrs, or shot peens metal parts. It features a steel mesh belt that moves components steadily through a blast chamber. Multiple blast wheels hurl abrasive media at each piece, stripping away rust, mill scale, or burrs. This method also improves fatigue life by inducing compressive stress.
Typical applications include prepping castings for painting, smoothing sharp edges on machined parts, and strengthening automotive or aerospace components. By streamlining cleaning and peening, you reduce manual labor and keep quality high.
Quick tip: Picture sending your parts through a “metal spa.” Instead of massages, they get an abrasive shower. The result? Smoother, tougher surfaces with minimal fuss.
Revolutionize Your Surface Treatment with Our Mesh Belt Shot Blasting Machine
Struggling with inconsistent surface finishes that compromise product quality?
Achieve uniform and superior surface finishes effortlessly. Our Wire Mesh Belt Blast Equipment ensures consistent cleaning and preparation, enhancing the quality and durability of your products.
Call us today at +86 135 8931 7685
2. Wire Mesh Belt Shot Blasting Machine: Robust Construction & Key Materials
BlastKing Wire Mesh Belt Shot Blasting Machines are engineered with premium materials for maximum durability and exceptional performance in demanding industrial environments. Here’s what makes our construction stand apart:
Abrasion-Resistant Manganese Steel Liners
Our shot blasting chambers are strategically equipped with manganese steel liners in areas experiencing the highest abrasive flow. This unique material exhibits a remarkable ability to harden upon impact—effectively shielding the machine from continuous wear and significantly extending its service life. With this advanced design, maintenance requirements are dramatically reduced.
Heavy-Duty Blasting Chamber
The main blasting cabinet features robust, thick steel walls, ensuring unparalleled structural integrity and longevity. Key areas within the chamber are further fortified with replaceable wear-resistant panels, simplifying maintenance routines. Operators benefit from reduced downtime, easy upkeep, and consistent productivity.
Durable Design: Built to Withstand the Toughest Conditions
Experiencing frequent equipment breakdowns and high maintenance costs?
Constructed with high-quality materials and wear-resistant components, our machine offers longevity and reliability, reducing maintenance needs and ensuring continuous operation.
Call us today at +86 135 8931 7685
High-Performance Wire Mesh Belt Conveyor
The conveyor belt, integral to the system’s operation, is custom-engineered to withstand intense blasting conditions. The surface of our wire mesh belt is hardened to an impressive 65 HRC, making it exceptionally resistant to high-velocity abrasive impacts. Constructed from corrosion-resistant steel wires intricately woven together, the belt accommodates a variety of part shapes and weights, allowing blasting media to effortlessly pass through without clogging.
Modular Conveyor System
To boost efficiency and reduce maintenance time, the conveyor system is designed with modular segments. High-quality, industrial-grade motors precisely control each segment, ensuring smooth, stable belt movement. If a section ever requires repair or replacement, the modular design allows for quick, targeted maintenance without extensive teardown—saving time and reducing costs.
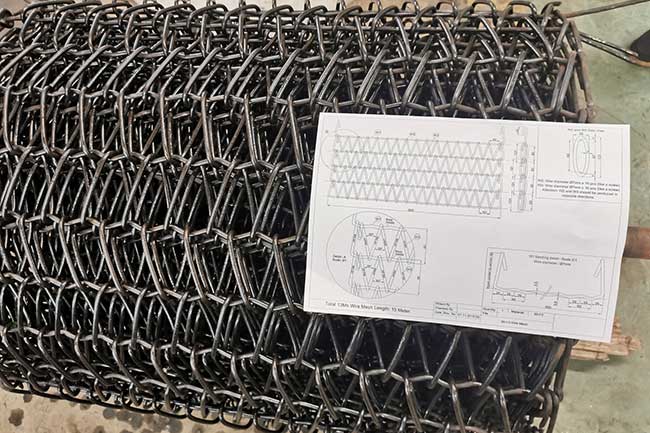
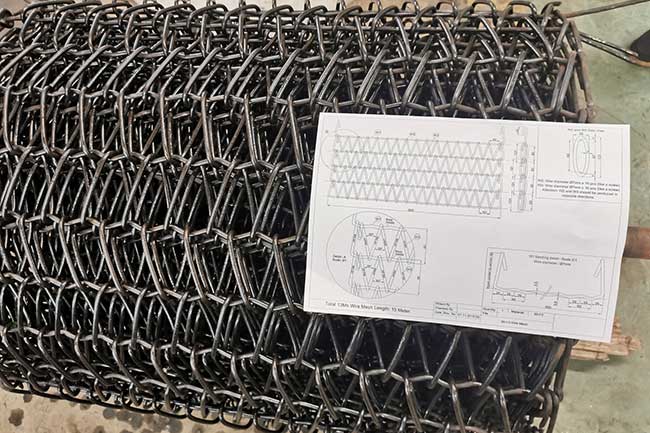
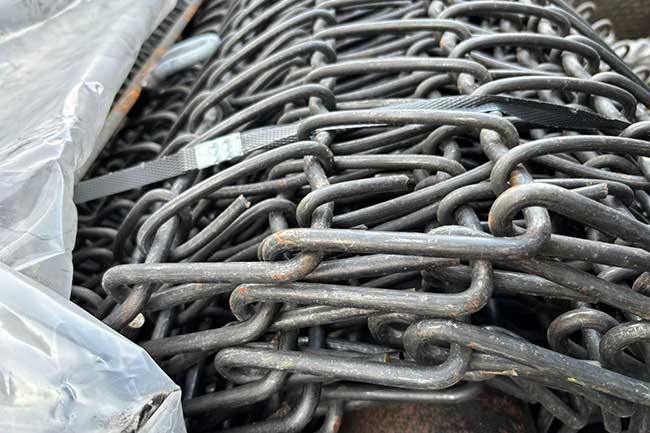
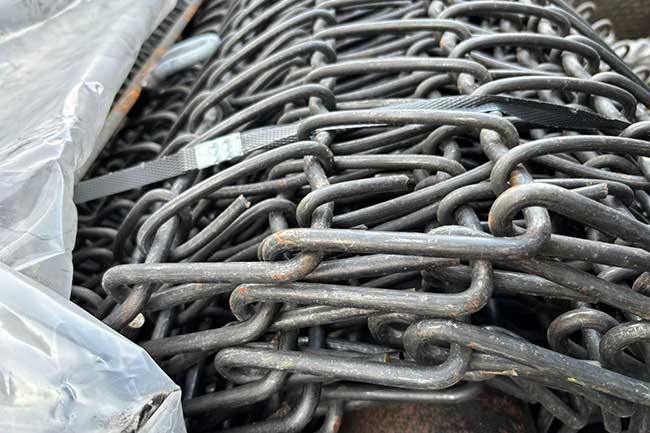
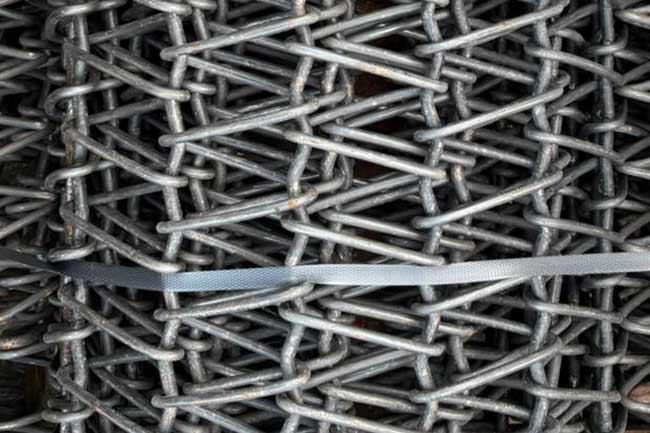
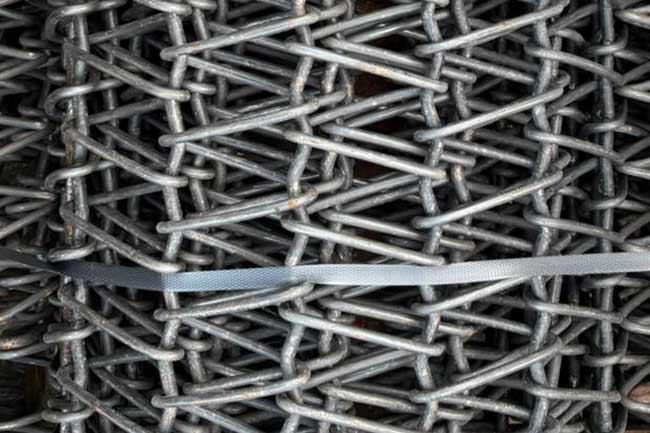
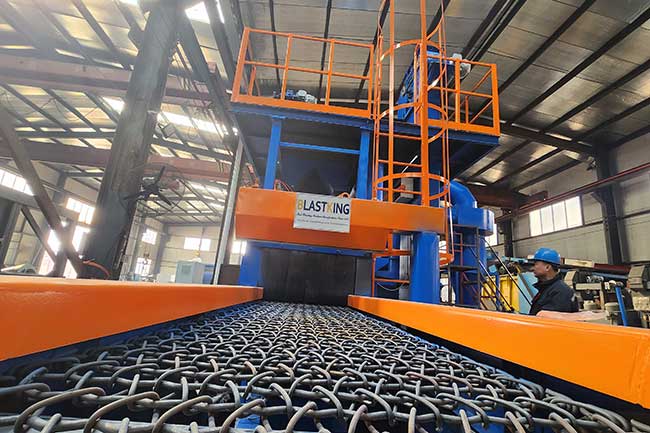
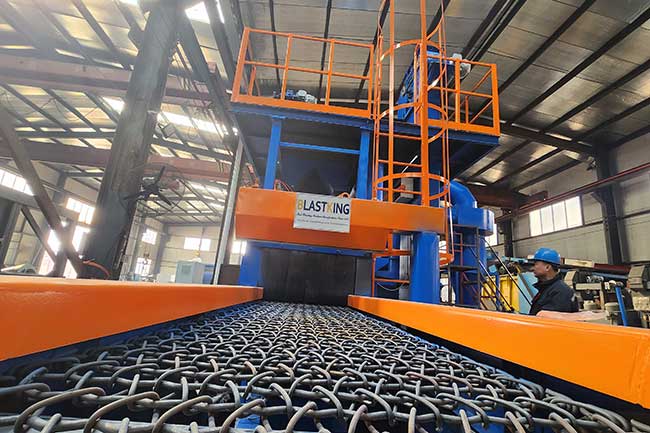
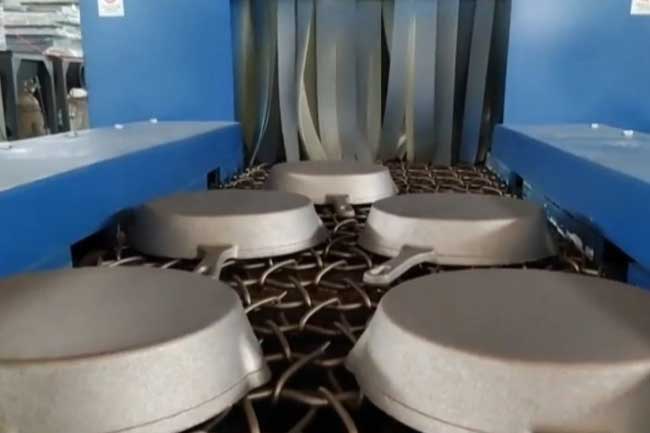
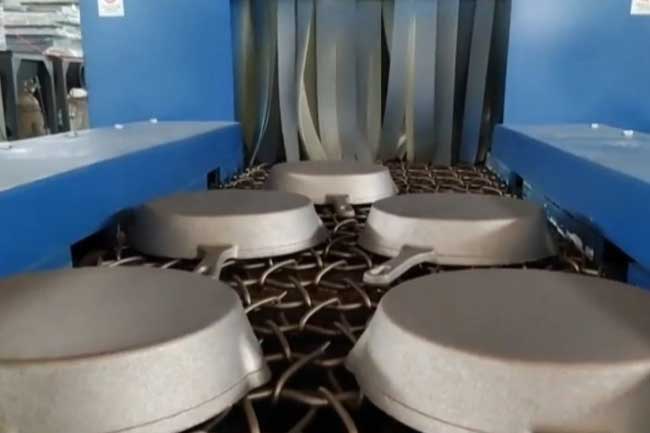
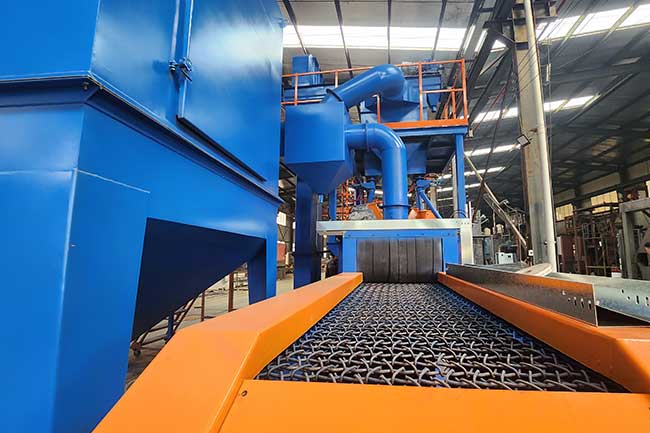
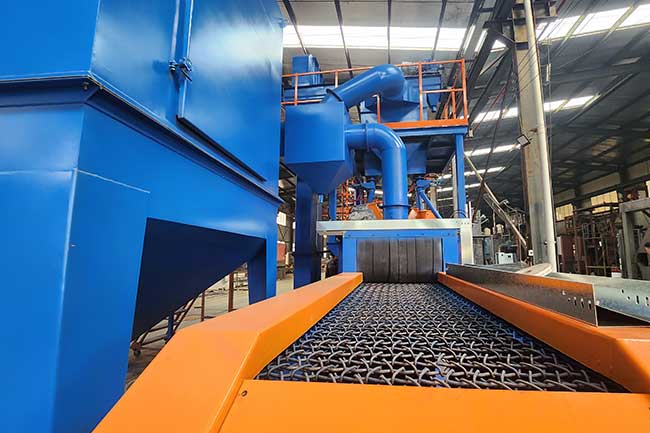
Advanced Protection & Reliability
Beyond durability, the robust construction of BlastKing’s Wire Mesh Belt Shot Blasting Machine ensures consistent and uniform cleaning results. The sturdy conveyor system precisely positions parts for optimal blasting coverage, enhancing production quality and efficiency.
Fun Fact:
Manganese steel is famously tough—so tough, in fact, that it’s often called “the steel that can’t be tamed.” At BlastKing, we believe every steel just needs a confident operator, paired with the right machinery.
Optimize your surface preparation with BlastKing—your reliable partner in shot blasting solutions.
3. Blast Wheel Arrangement
Blast wheels generate the impact that cleans or peens your metal parts. We carefully position each wheel to cover every visible surface. Most setups include multiple wheels, each powered by high-performance motors ranging from 7.5 kW to 22 kW. The wheels can handle steel shot, grit, or other abrasives.
Each wheel has an impeller, control cage, and replaceable blades. These parts control how the abrasive stream hits your components. By changing the wheel angle or adjusting wheel motor or wheel number configurations, you can optimize coverage. This flexibility helps you tackle anything from small brackets to bulky housings.
Remember: Proper positioning of blast wheels avoids “blind spots,” so you won’t need a second pass or extra cleaning steps.
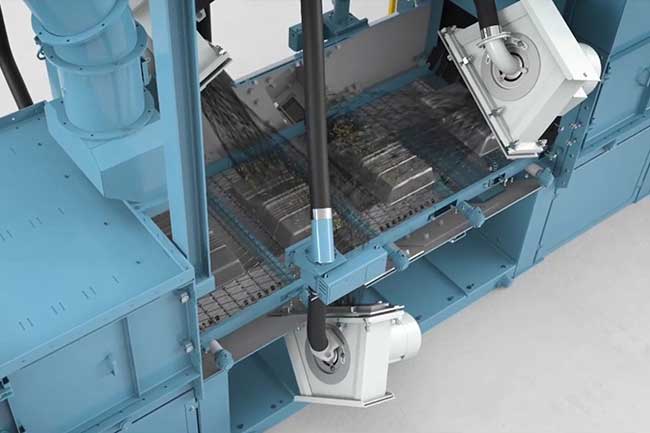
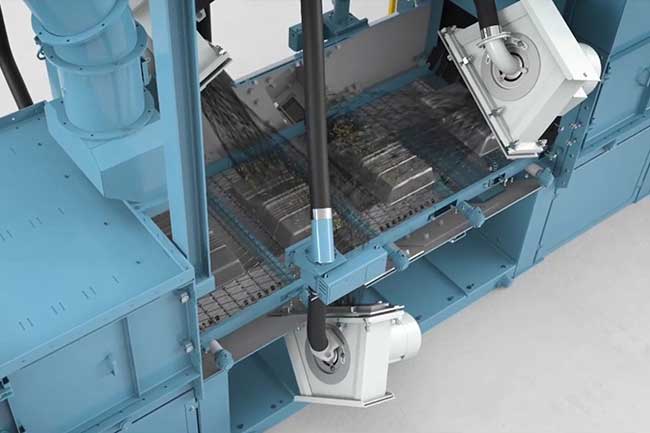
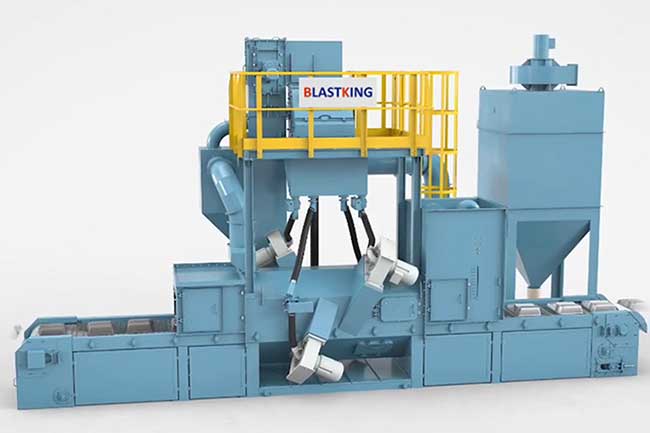
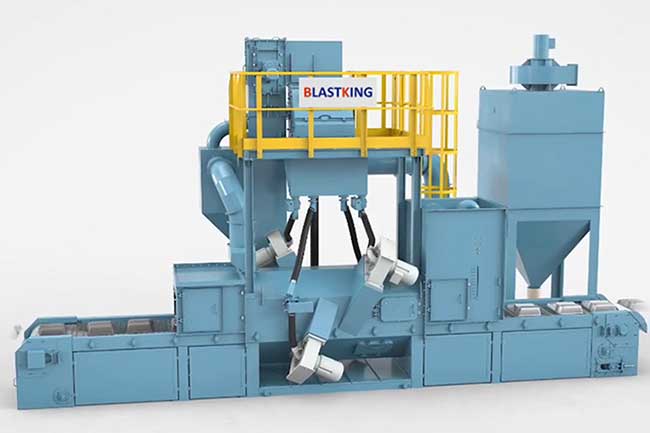
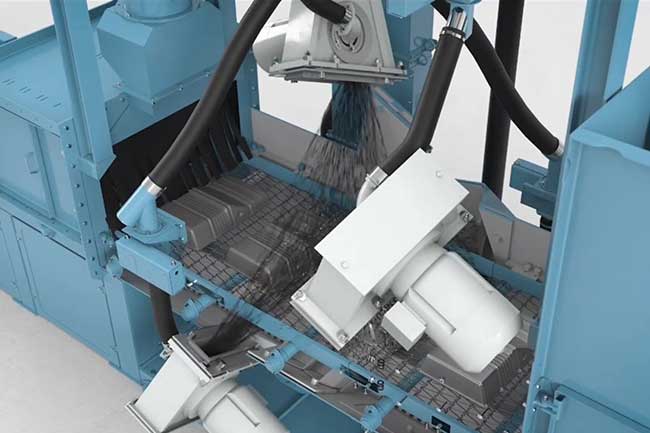
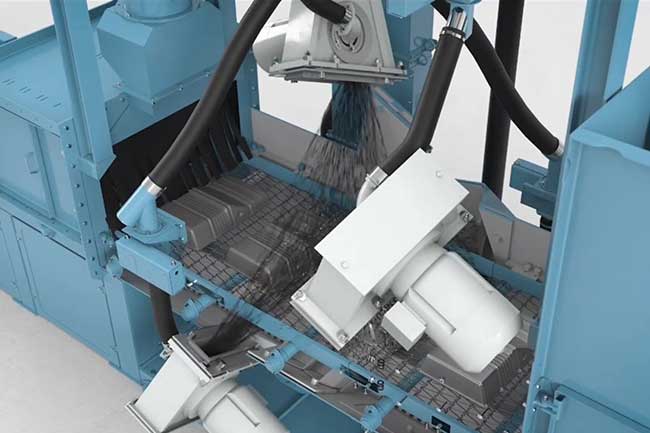
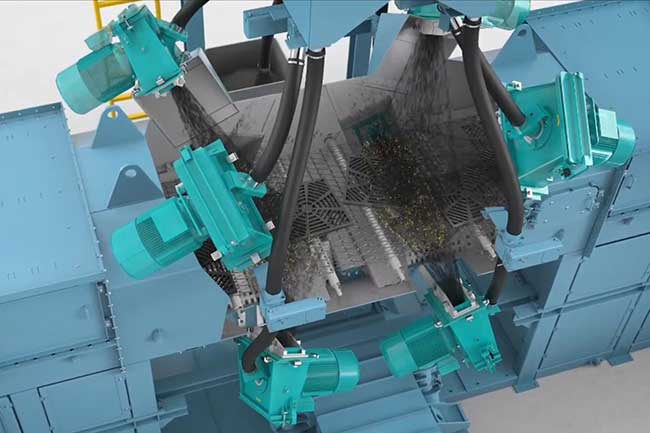
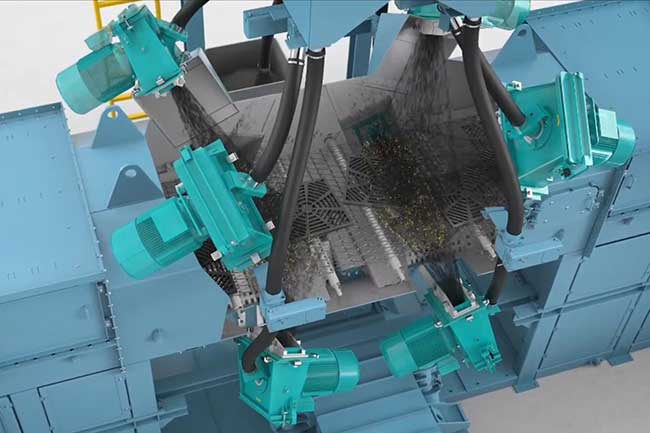
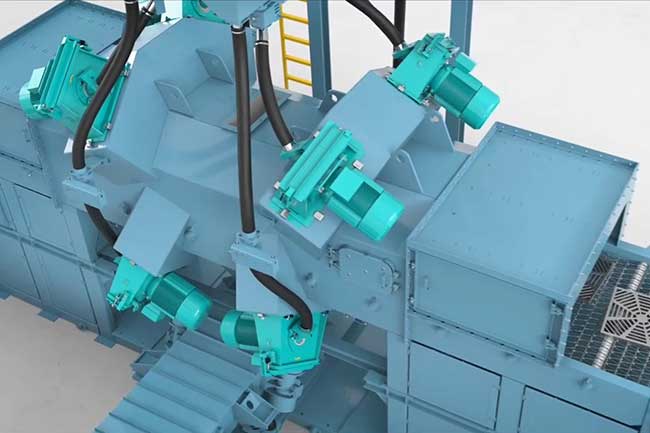
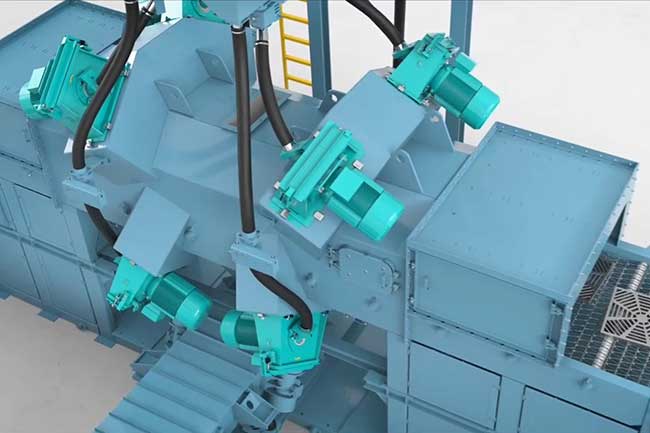
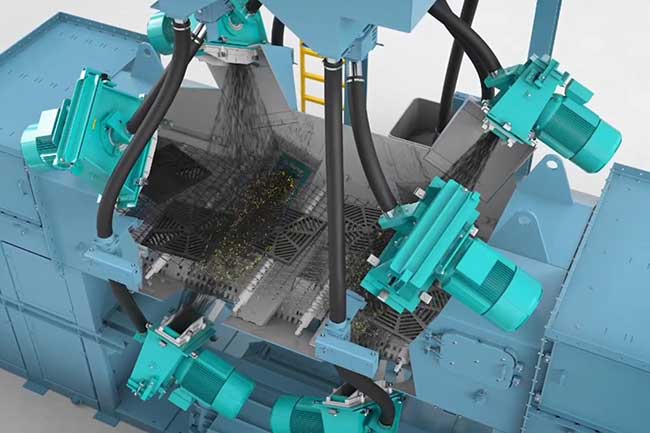
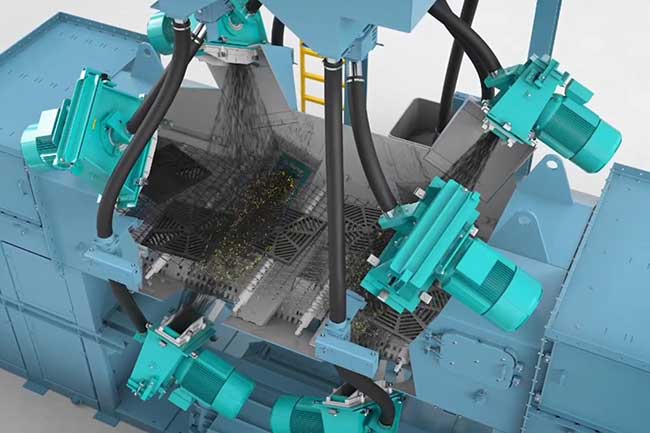
4. Abrasive Recovery and Circulation
Used abrasive drops into a reclaim system that filters out dust, broken shot, or metal fragments. First, an air wash separator removes lighter particles. Next, a magnetic separator captures any stray ferrous debris. Finally, the clean abrasive flows back to the wheels.
This process prevents waste and reduces costs. You’re not dumping shot every day. Plus, consistent abrasive quality means consistent blasting strength. That stability keeps your finish uniform and predictable.
Why it matters: Recycling saves money. You buy less new shot, and you don’t handle as much waste. It’s kind of like refilling your coffee cup instead of brewing a fresh pot every time.
Gentle Yet Effective: Ideal for Delicate and Complex Parts
Concerned about damaging thin-walled or intricate components during blasting?
Our machine’s gentle handling ensures that even the most delicate parts, such as aluminum castings and intricate forgings, are cleaned effectively without risk of deformation or damage.
Call us today at +86 135 8931 7685
5. Containment and Air Quality
Stray abrasive can be a nuisance. We keep it in check with Vulkolan curtains and rubber seals around infeed and outfeed points. These barriers let parts pass through but block media from escaping.
Inside, powerful dust collectors draw airborne particles out of the chamber. The filters capture fine dust, and the cleaned air recirculates safely or vents outside. You’ll spend less time sweeping floors or ducking clouds of dust.
Think of it as a vacuum that never takes a break. It keeps your workspace tidy and helps you meet environmental standards.
6. Control Systems and Automation
A PLC (Programmable Logic Controller) coordinates blast wheel speeds, conveyor speeds, and abrasive flow. Operators set parameters through an easy-to-use interface. If something goes off track, the system triggers an alert or halts the process. This reduces damage to parts and safeguards personnel.
In many factories, these machines sync with robotics or automated transfer systems. That integration streamlines loading, blasting, and unloading. It cuts manual handling and boosts consistency.
Reminder: Good automation keeps folks from running around in circles. Let the machine handle the heavy lifting, and use your time for other tasks.
Seamless Integration into Your Production Line
Worried about the challenges of incorporating new equipment into your existing setup?
Designed with versatility in mind, our Mesh Belt Shot Blasting Machine integrates smoothly into various production lines, enhancing your operations without major modifications.
Call us today at +86 135 8931 7685
7. Maintenance and Reliability
Shot blasting is tough on equipment. We mitigate wear by using heavy-duty materials and modular designs. Manganese steel panels protect the blast chamber, and wire mesh belts are reinforced for strength. Blast wheels come apart quickly for blade or control cage swaps.
Regular checks on belt alignment, dust collectors, and wear liners help you dodge expensive breakdowns. Early detection of issues means shorter downtimes. Our support team can also offer guidance if you spot unusual wear or performance dips.
Pro tip: Schedule simple inspections like you’d schedule oil changes in a car. A little foresight saves big headaches.
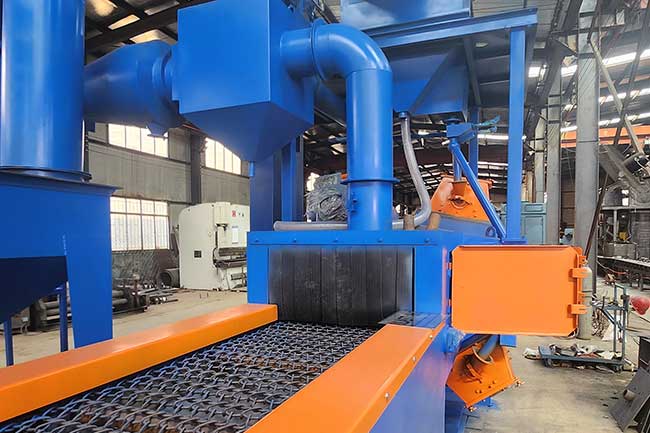
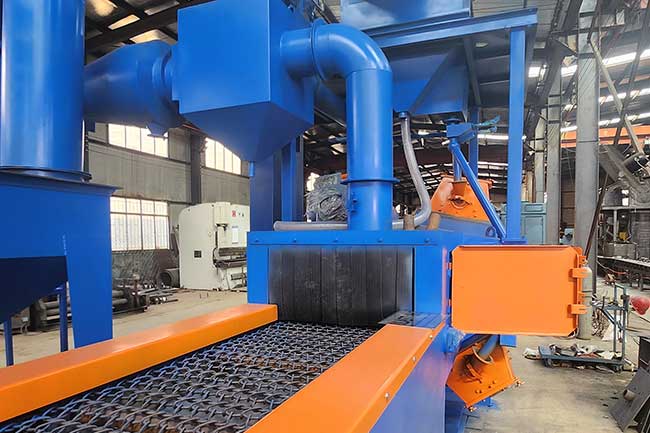
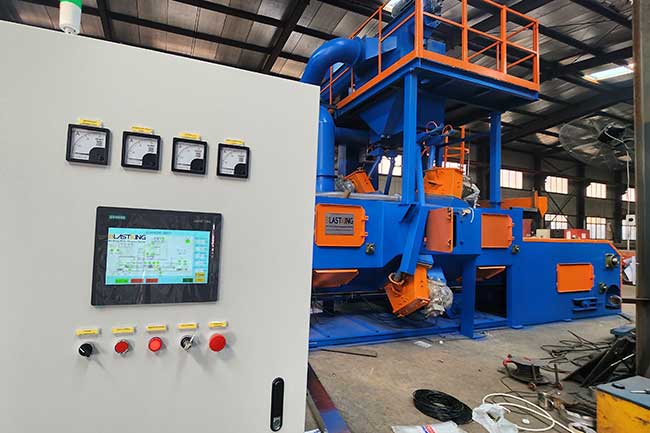
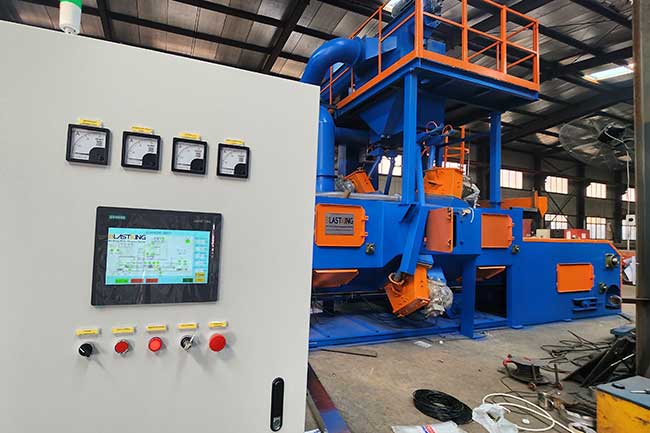
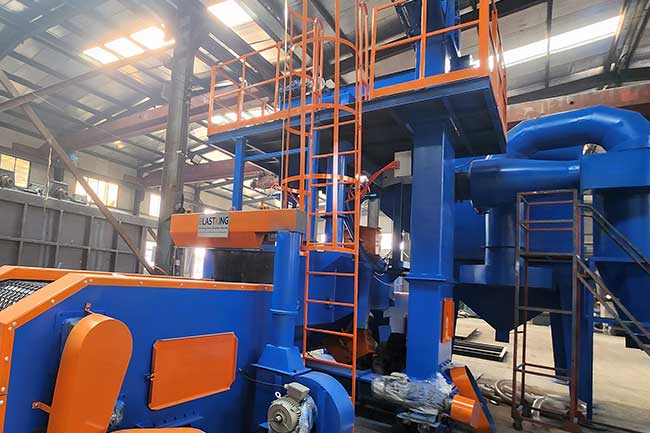
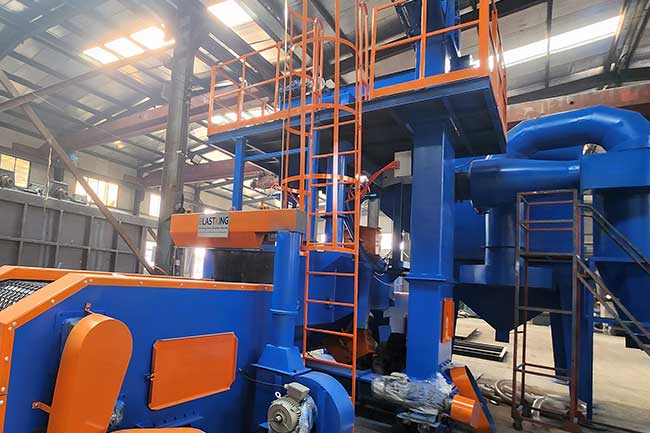
8. Part Quality and Surface Consistency
Every part rolling off your production line should meet the same cleanliness or peening standard. Our wire mesh belt method maintains a steady abrasive flow. Carefully placed blast wheels guarantee even surface impact. That uniformity matters if you’re applying paint or coatings later. It also matters for parts needing tight tolerances or stress relief.
This consistent coverage ensures fewer rejects or reblasting cycles. It also boosts overall product reliability. Clients and end-users notice when parts look and perform better right from the get-go.
Bottom line: When surfaces are smooth and free of contaminants, everything else down the line just works better.
9. Adaptability to Various Industries
Our wire mesh belt shot blasting machine fits automotive, aerospace, foundry, and structural steel processes. Automotive plants use it for axle components or brake assemblies. Foundries clear sand and scale from freshly cast parts. Aerospace facilities rely on shot peening to extend fatigue life in critical parts.
The belt conveyor handles many shapes and sizes. As long as they fit beneath the maximum height clearance, they can ride through. Changing abrasive types or adjusting conveyor speeds lets you handle different materials with minimal fuss.
No “one-trick pony” here. You get a system that adapts to your production mix rather than forcing you to adjust your entire line.
Durable Design: Built to Withstand the Toughest Conditions
Experiencing frequent equipment breakdowns and high maintenance costs?
Content: Constructed with high-quality materials and wear-resistant components, our machine offers longevity and reliability, reducing maintenance needs and ensuring continuous operation.
Call us today at +86 135 8931 7685
10. Installation and Integration
At BlastKing, we aim to simplify setup. We collaborate on layout, power requirements, and dust collector placement. The machine can stand alone or connect to an existing conveyor network. In some plants, it sits right after machining stations. In others, it’s positioned before paint booths.
Electrical and mechanical tie-ins are straightforward with the help of our technical team. We also provide clear documentation for routine operation. Proper foundation anchoring keeps the system stable over time. Our goal is to get you blasting without extended downtime.
Tip: Double-check ceiling height and part flow direction before finalizing the spot. A little planning saves you from future forklift tango moves.
11. Operational Efficiency and Throughput
Continuous operation is a key advantage. The belt keeps your parts moving, and the blast wheels do the heavy cleaning. You’re not waiting around for a batch to finish. This boosts overall throughput and meets tight production schedules.
You can also fine-tune the conveyor and wheel speeds to optimize cycle time. Parts with stubborn rust may need a slower pass. Clean, lightly oxidized parts might cruise through faster. By staying flexible, you avoid over-treating or under-treating items.
Remember: Time is money. Keeping that belt rolling at the right pace helps you maximize productivity.
Tailored Solutions to Meet Your Specific Needs
Finding it challenging to source equipment that fits your unique requirements?
We offer customizable configurations to match your specific applications, ensuring that our Mesh Belt Shot Blasting Machine meets your operational needs perfectly.
Call us today at +86 135 8931 7685
12. Environmental Responsibility
Shot blasting is more eco-friendly than chemical-based treatments. Our machine reuses abrasive media, lowering disposal and new material costs. Dust collectors capture airborne particles instead of venting them outside. This supports a healthier workspace and local compliance.
We also use energy-efficient motors and drives to reduce power consumption. Variable Frequency Drives (VFDs) can manage blast wheel output based on real-time demand. By not blasting at full throttle when it’s unnecessary, you save energy. That’s kinder to the planet and your wallet.
It’s like turning off the lights in an empty room. Small changes add up over long production runs.
13. Quality Management and Process Verification
The machine’s PLC logs crucial data like blast wheel RPM, belt speed, and abrasive flow rate. This data helps you confirm that each batch was processed within the correct settings. If a product falls short of specs, you can refer to the logs to identify any anomalies.
Uniform conditions support strict standards required by aerospace, automotive, or other regulated industries. Consistent results mean fewer surprises down the line. It also gives you a record to show auditors or clients who demand proof of controlled operations.
Confidence check: When you can trace every step, you minimize guesswork. That’s a big deal for professional QA teams.
Tailored Solutions to Meet Your Specific Needs
Finding it challenging to source equipment that fits your unique requirements?
We offer customizable configurations to match your specific applications, ensuring that our Mesh Belt Shot Blasting Machine meets your operational needs perfectly.
Call us today at +86 135 8931 7685
14. Economic Impact and ROI
Automating cleaning or peening tasks slashes manual labor costs and cuts rework. By reusing abrasive media, you spend less on replacements. Consistent blasting also speeds up post-blast operations like coating or inspection. These factors combine to give a solid return on your investment.
Over time, reliable equipment and fewer production hiccups can enhance customer satisfaction. Delivering top-quality, on-time orders often leads to repeat business. A well-optimized shot blasting process helps your entire line run smoother.
Think of it as a long-term investment in efficiency and brand reputation. Reliability is something clients remember.
15. Conclusion
A wire mesh belt shot blasting machine from BlastKing is your ally in high-volume, efficient metal treatment. The continuous conveyor design, powerful blast wheels, and robust construction deliver consistent results every time. Manganese steel liners and modular components keep maintenance manageable. Plus, advanced controls and dust containment make operations safer and cleaner.
We’ve honed this technology since 1982 to support professionals in automotive, aerospace, foundry, and beyond. By combining adaptability with strong ROI, our system can suit small shops or sprawling production lines. If you need a proven way to elevate part quality—and maybe cut down on stressful manual labor—our wire mesh belt shot blasting machine is ready to roll. Let’s chat about how it can transform your workflow. It might just make your parts feel invincible—and lighten your workload along the way!
16. Frequently Asked Questions
Which industries typically use wire mesh belt shot blasting machines?
These machines are popular in automotive, aerospace, foundries, metal fabrication, construction steel, and heavy machinery manufacturing industries.
What are the main benefits of choosing BlastKing’s wire mesh belt shot blasting machine?
BlastKing’s machines offer consistent results, continuous production flow, reduced labor costs, simplified maintenance, reliable abrasive recycling, and improved surface preparation quality.
Can the abrasive material be reused?
Yes, the abrasive media is continually recycled through a built-in reclamation system, reducing material costs and environmental waste.
Can this shot blasting machine integrate into an existing production line?
Absolutely. The wire mesh belt machine easily fits into automated lines with robotic handling or conveyors. Its PLC controls communicate smoothly with existing manufacturing setups.
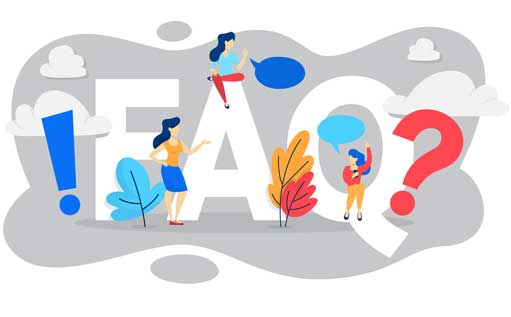
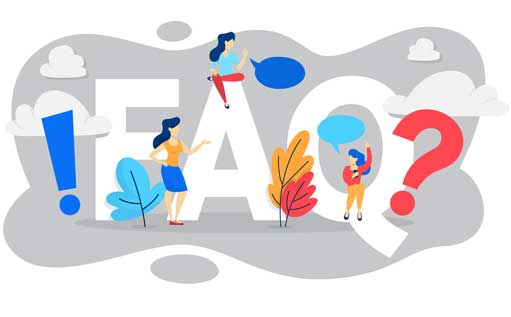
Need more help?
We have got you covered.