Dust Free Vacuum Blasting for Superior Results!
Updated: August 29, 2025
Traditional blasting methods often result in hazardous dust clouds, endangering your health and the environment. BlastKing’s dust-free vacuum blasting machine ensures a clean and safe work environment, revolutionizing surface preparation.
1. What Is The Dust Free Vacuum Blaster Used For?
BlastKing’s vacuum or dust-free blasting presents an optimal solution for targeted repairs, welding seams, and on-site blasting within operational settings where the presence of dust and abrasive particles is undesirable.
During the blasting process, a sealed brush head ensures that dust and abrasive materials are promptly sucked up by a powerful vacuum unit. The separator and silo efficiently recycle the used abrasives, while the contained dust can be easily discharged. BlastKing’s vacuum blasting offers a secure blasting method suitable for confined or critical areas, albeit with a reduced working speed compared to open blasting techniques.
Experience efficient and clean blasting with our dust free blasting technology!
Achieving precision in surface preparation is crucial for the success of your projects. Our dust-free vacuum blasting machine offers unparalleled control and accuracy, ensuring pristine results every time.
Don’t settle for less—partner with us for precision surface preparation!
Call us today at +86 135 8931 7685
2. Vacuum Blaster Features And Benefits
- Closed-Circuit System
Benefit: Minimizes dust emission, ensuring a clean and safe work environment while reducing the need for extensive protective measures. - 100% Dust-Free Operation
Benefit: Fully automated blasting and vacuum start/stop sequence guarantee a dust-free operation, eliminating health hazards and improving efficiency. - Clean, Abrasive-Free Surface
Benefit: Achieve pristine surfaces after blasting, enhancing the quality of your workmanship and reducing the need for additional cleaning steps. - Automatic Filter Cleaning
Benefit: No time-loss with automatic filter cleaning and dust discharge, maximizing productivity and minimizing downtime. - Easy Disposal
Benefit: Dispose of collected dust effortlessly with easy-to-use plastic bags, streamlining cleanup processes and reducing labor requirements. - Portability
Benefit: Easily relocate or transport the unit as needed, offering flexibility and convenience for various project locations. - Wide Range of Brushes
Benefit: Choose from a wide range of brushes to fit all types of surfaces, including flat, cornered, and radiused, ensuring versatility and precision in surface preparation.
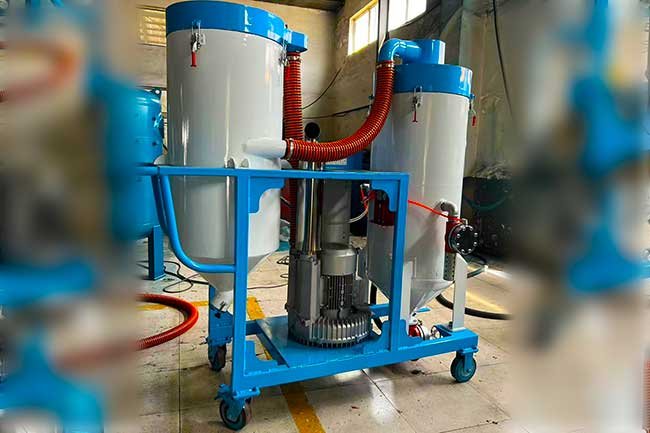
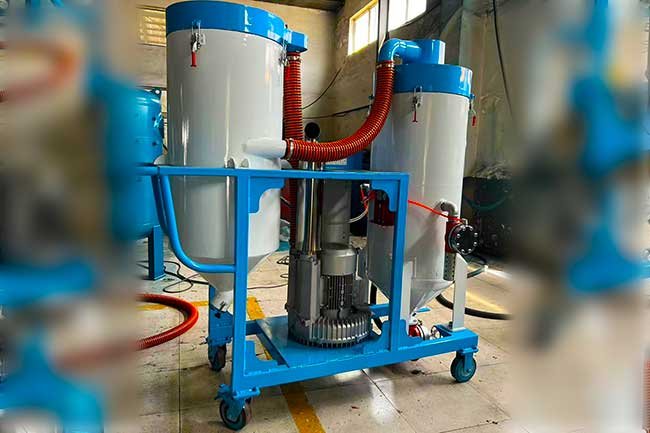
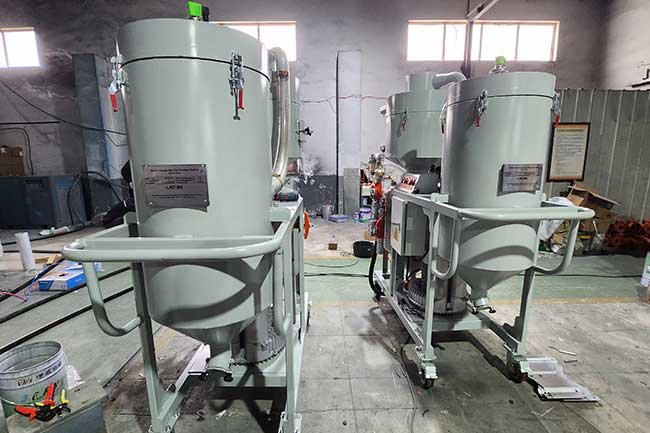
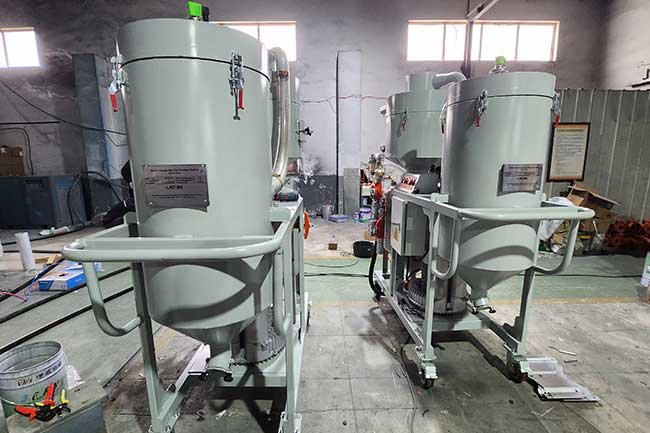
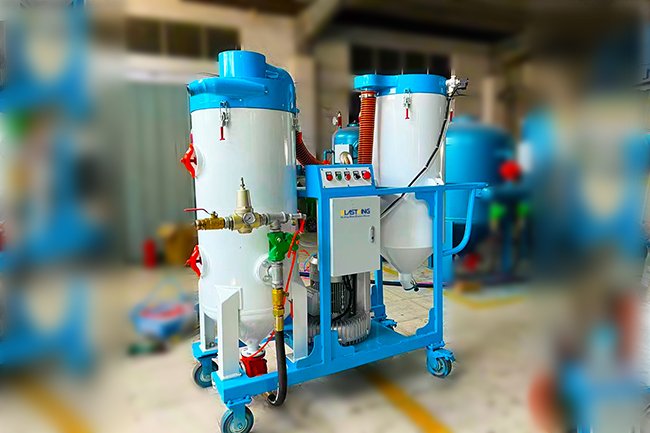
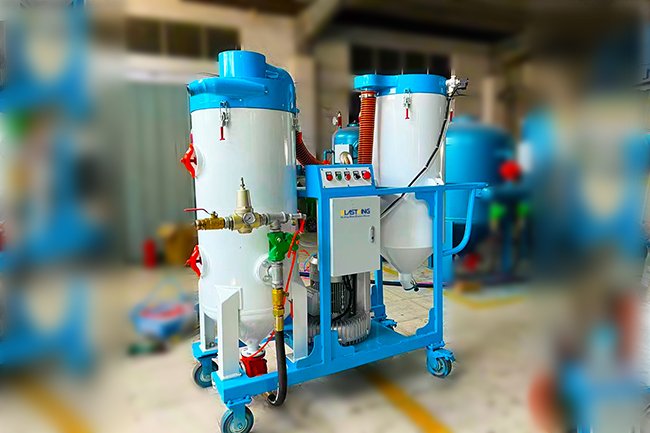
3. Applications
The utilization of steel abrasive facilitates cost-efficient, effective, and potent blasting, alongside meticulous oversight of surface preparation. Easily interchangeable blast head fittings offer versatility in blasting various surfaces, encompassing flat planes, interior and exterior corners, as well as both small and large diameter pipes. Supplementary accessories cater to specific needs, such as blasting expansive horizontal surfaces or refining the edges of steel plates.
Given the process’s safety and dust-free nature, it allows for concurrent execution of other production processes in proximity to the blasting operation.
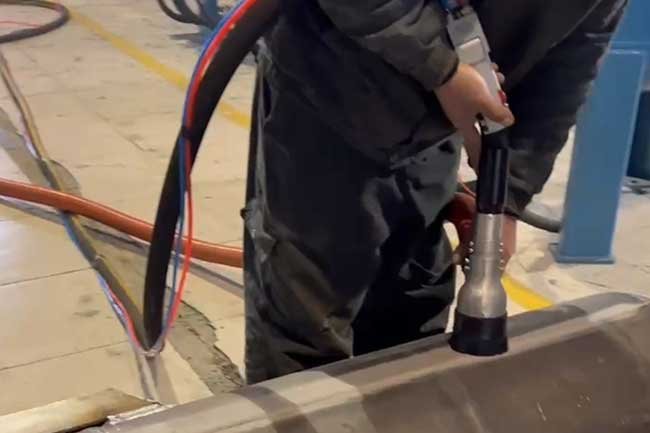
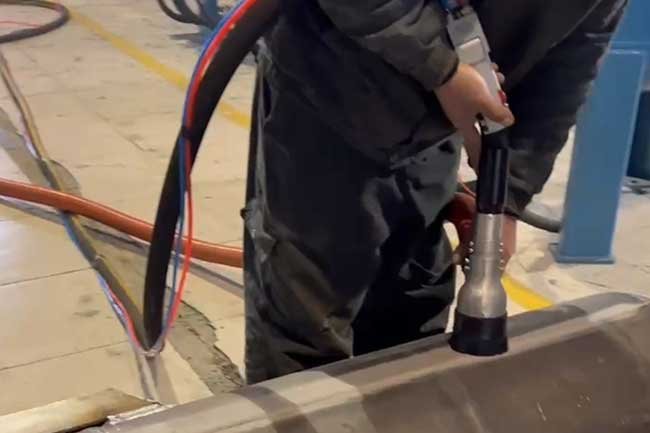
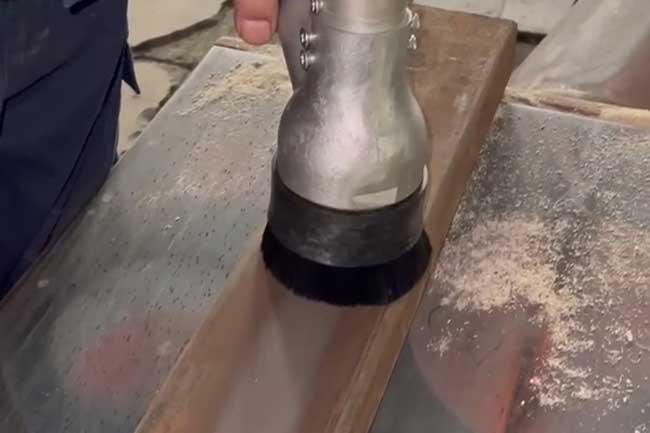
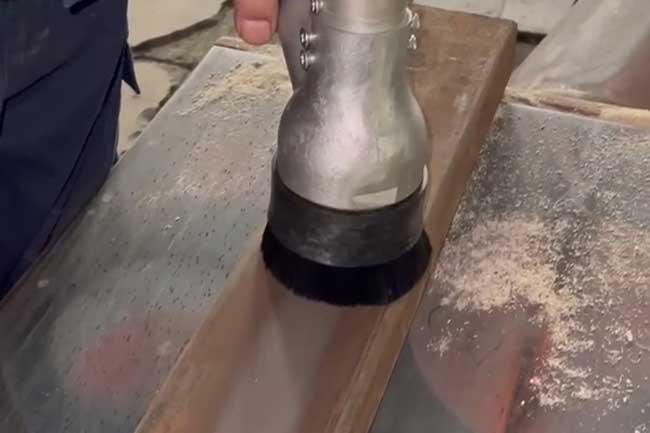
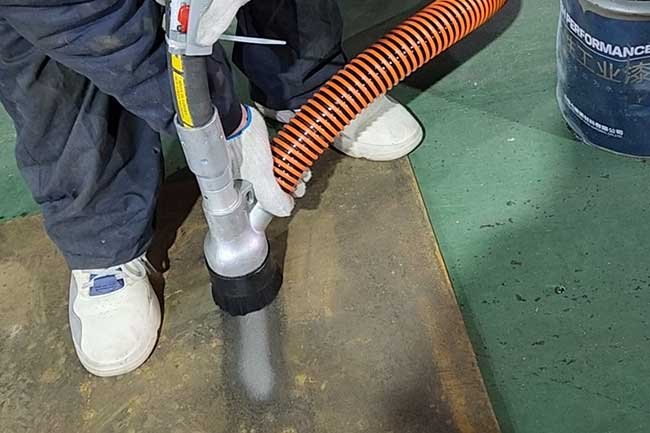
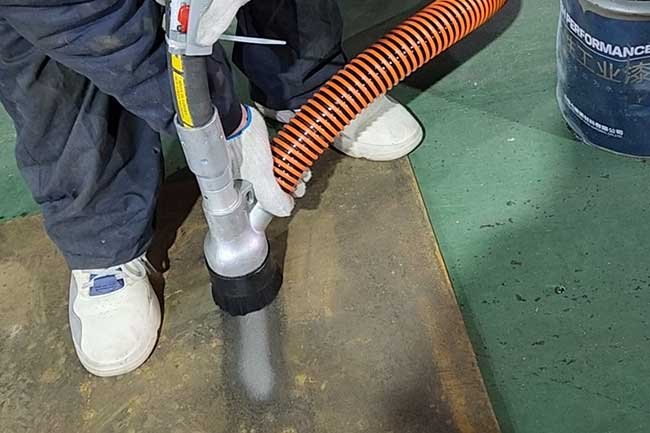
Streamline your projects with hassle-free dust containment and removal!
Traditional blasting poses significant health and safety risks due to dust exposure. Our dustless vacuum blasting machine prioritizes safety by containing dust particles, protecting both workers and the surrounding environment.
Get in touch to simplify your surface preparation process!
Call us today at +86 135 8931 7685
4. Dust Free Blasting
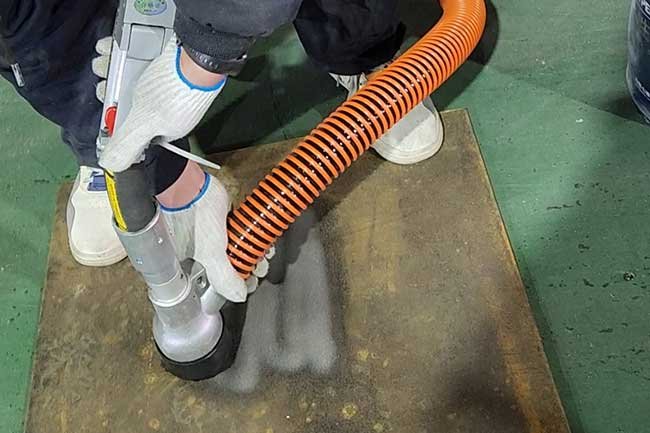
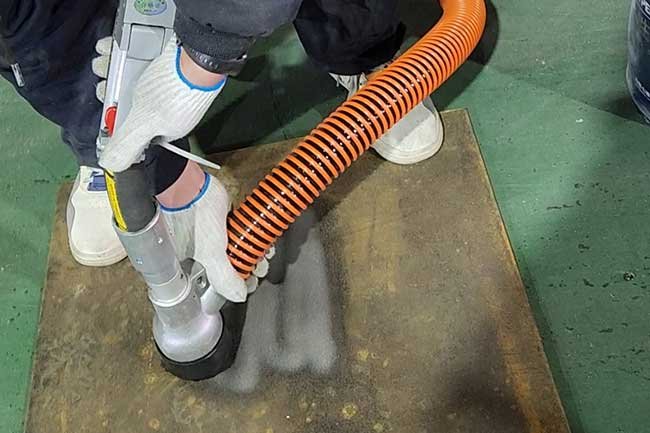
5. Working Video
Protect Your Team and Environment with Our Dustless Vacuum S Blasting Solution!
Cleaning up after traditional blasting methods can be time-consuming and labor-intensive. Our advanced technology eliminates the need for extensive cleanup, saving you valuable time and effort.
Don’t settle for less—partner with us for precision surface preparation!
Call us today at +86 135 8931 7685
6. FAQs (Frequently Asked Questions)
Q1: What Are the Application Restrictions of the Dust Free Blasters?
The application restrictions of the dust-free blasters primarily revolve around their suitability for blast cleaning parts that cannot be accommodated within a cabinet or blast room due to factors such as size, weight, or transportation distance. The design of these machines facilitates localized blast cleaning without the dispersion of abrasive, dust, or debris into the surrounding environment. However, to ensure safety and protect both individuals and equipment in the vicinity, the following additional limitations apply:
-
Individuals without special protective clothing are prohibited from remaining within a 10-meter perimeter from the blasting activity.
-
Damageable equipment should be relocated beyond a perimeter of 10 meters to avoid potential harm.
In terms of suitable blast media, options include glass beads, aluminum oxide, steel grit, or steel shot, among others. It’s important to note that there is no lifetime warranty when using aluminum oxide with the blast machine, which is rated for a maximum working pressure of 8 bars.
-
Q2: What Are The Main Components of A Dust Free Vacuum Abrasive Blaster Unit?
The core components of the vacuum sand blasting machine typically encompass a comprehensive array of sophisticated machinery tailored to ensure optimal performance and efficiency. At the heart of the apparatus lies the blast pot, meticulously engineered to house and dispense abrasive materials with precision and control. This reservoir serves as the reservoir of kinetic energy, where abrasive particles await deployment onto the target surface, ready to unleash their transformative power.
Complementing this pivotal element is the robust suction unit, a powerhouse of suction prowess designed to swiftly and effectively extract debris generated during the blasting process. Through its relentless suction force, this unit ensures that no remnants of the abrasive or dislodged materials are left to linger, thereby upholding the pristine integrity of the working environment.
Nestled within the blast head are specialized brushes, meticulously crafted to interface seamlessly with the contours of the surface under treatment. Serving as the vanguard of surface treatment, these brushes operate in tandem with the abrasive stream, ensuring thorough and uniform coverage while meticulously addressing surface imperfections with finesse and precision.
Further enhancing the functionality of the system is the intricate filtration unit, a marvel of engineering ingenuity tasked with the arduous duty of separating paint and debris from the abrasive material. Employing a multifaceted approach to filtration, this unit effectively sieves out unwanted contaminants, thereby preserving the purity and efficacy of the abrasive material for continued use.
Together, these meticulously engineered components synergize to form an indispensable arsenal in the realm of surface preparation, imbued with the capability to seamlessly execute dust free vacuum sand blaster operations with unparalleled efficiency and finesse.
Q3: How Does The Vacuum Blaster Work?
BlastKing’s airblast dust free blasting is a sophisticated method meticulously designed to contain abrasive particles and debris within a specialized blast head. This innovative approach ensures that minimal dust and airborne particles are released into the surrounding environment, thereby facilitating a cleaner and safer work area. Achieving complete dustless blasting represents the pinnacle of this technology, where the elimination of any dust or airborne contaminants becomes a reality through the utilization of a vacuum system. Within this dust free blasting machine system, both the abrasive and debris are securely contained within the blast head, subsequently extracted by either an electric or air-powered vacuum mechanism.
Renowned for their efficiency and environmental consciousness, these systems are commonly referred to as “closed-loop” blast systems. This nomenclature reflects their remarkable capacity to recover and automatically recirculate the abrasive material around the apparatus, minimizing waste and maximizing efficiency.
Central to the closed loop dust free blasting unit is the fusion of a blast pot with a robust suction unit. Within the blast head, the intricate process of blasting is facilitated by brushes meticulously contoured to the surface being treated. Here, the abrasive material, typically aluminum oxide, undergoes a cycle of recovery and reuse, ensuring optimal resource utilization. Concurrently, the filtration unit diligently separates paint and debris from the abrasive material, depositing them into a waste bag autonomously.
The versatility of dust-free blaster extends across a wide spectrum of materials, offering not only cost-effectiveness but also environmental friendliness. This comprehensive approach to surface preparation exemplifies a harmonious balance between efficiency, efficacy, and environmental stewardship.
Q4: How Does It Differ From Traditional Blasting?
Unlike traditional blasting methods that generate significant dust and debris, dust-free vacuum blasting machines integrate vacuum systems to capture particles immediately, resulting in minimal mess and environmental impact.
Q5: Can It Remove Rust and Corrosion Effectively?
Absolutely, dust-free vacuum blasting machines excel in removing rust, corrosion, paint, and other surface contaminants without causing damage to the underlying substrate, making them ideal for surface restoration projects.
Q6: What Are The Idea Applications For the Dust Free Vacuum Blasters?
Vacuum or dust-free blasting stands as an optimal solution for targeted repairs, addressing welding seams, and conducting on-the-spot blasting within operational environments where the presence of dust and abrasive pollutants poses significant concerns. This method ensures a meticulous approach to surface preparation while safeguarding against environmental contamination. By employing advanced vacuum technology, it effectively contains abrasive materials and debris, mitigating the risk of dispersal into the surrounding atmosphere. This approach not only enhances the quality of surface treatments but also promotes a safer and healthier working environment. Furthermore, the versatility of vacuum blasting extends beyond traditional applications, offering a flexible and adaptable solution for various industrial and commercial settings. Whether tackling intricate repairs or addressing surface imperfections, vacuum blasting emerges as a reliable and efficient technique, aligning with modern standards of quality and environmental responsibility.
7. Conclusion
The rise of dust-free vacuum sand blasting machines is changing the game in surface cleaning and prep. These cutting-edge tools don’t just set new industry standards—they also show our commitment to the environment. By reducing harmful emissions and shrinking the ecological footprint, these eco-friendly blasters align with global sustainability goals.
But wait, there’s more! These machines are also cost-effective and versatile, making them must-haves across various industries. Whether you’re in automotive refinishing or industrial maintenance, dust-free vacuum blasters efficiently remove coatings, rust, and corrosion. They prep surfaces perfectly for top-notch finishes and long-lasting durability.
Plus, they make work safer and more comfortable. No more airborne contaminants and less exposure to hazardous materials mean a healthier work environment without compromising performance or efficiency.
And that’s not all. Our range of airblast equipment and shot blasting solutions boosts productivity and streamlines operations. Need automated machines for high-volume production? Or precision gear for specialized tasks? We’ve got you covered with options to fit every industrial need.
Embracing dust-free vacuum blasters isn’t just about keeping up with technology. It’s about committing to excellence and sustainability. As we innovate, we stay dedicated to providing solutions that empower businesses, protect the planet, and raise industry standards.
Ready to make the switch? Let’s blast ahead together!