Blasting Room 101: Things You Should Know About Blast Booth
Updated: August 15, 2025
Discover high-efficiency blast rooms from BlastKing. Enhance your surface preparation with custom-designed, eco-friendly solutions. Book a consultation today.
Outline
1. Key Components of Blast Room Systems
Think of a blast room as a large, dust-free sanctuary for abrasive blasting, just like a blast cabinet but on a grander scale. Instead of working outside, operators step inside this enclosed space to get the job done.
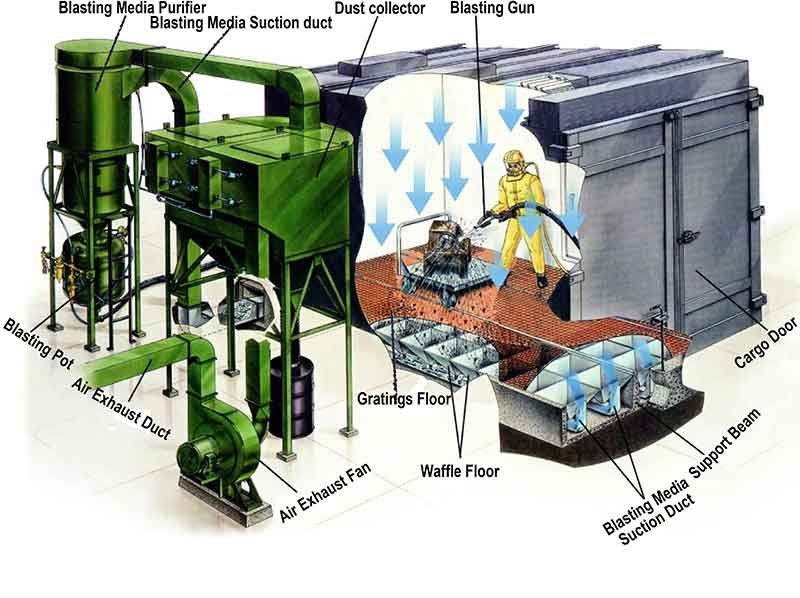
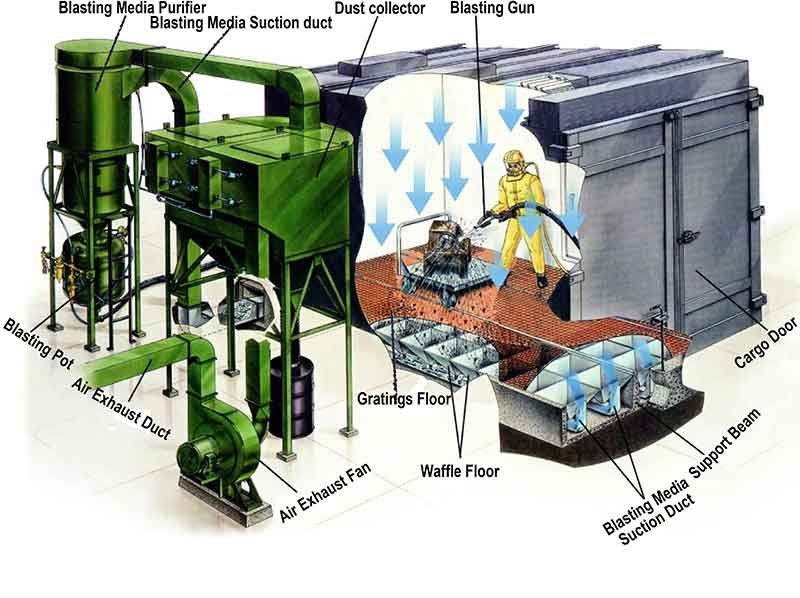
1. Blasting Chamber:
The blasting chamber is the heart of the operation. It’s built from sturdy materials like structural steel, cladding, or sandwich panels. To keep everything running smoothly and quietly, the walls and ceiling are lined with abrasion-resistant rubber or polyurethane. It’s like having a durable, noise-cancelling shield around your workspace.
2. Dust collector
The dust collector acts like the lungs of the blast room. It ensures clean air by filtering out dust, fine abrasive particles, and contaminants. This not only keeps the environment safe but also makes sure you’re breathing easy while working.
3. Abrasive reclaim system
This system is like the diligent recycler, transporting spent abrasive media after blasting to the recycling and cleaning unit. It keeps things efficient and tidy.
4. Abrasive recycling and cleaning unit
Think of this system as your efficient recycler. It transports used abrasive media from the blasting area to the recycling and cleaning unit. No mess, no fuss—just a smooth, continuous process.
5. Blasting Equipment
The blasting equipment is the star player, the essential machinery that performs the abrasive blasting. It’s what makes the whole system tick.
Understanding these components helps you appreciate how a well-designed blasting room can enhance efficiency, safety, and overall performance. Let’s ensure your blasting operations run like a well-oiled machine, perfectly tailored to your needs.
Transform Your Blasting Efficiency with Our State-of-the-Art Blast Rooms!
Imagine a workspace where dust-free, efficient blasting is the norm. Our cutting-edge blast rooms are designed to enhance your productivity and ensure the highest safety standards. Explore the benefits of a custom-designed blast room tailored to your specific needs.
Call us today at +86 135 8931 7685
2. Sand Blast Room Size
Blast chambers come in all shapes and sizes, tailored to fit your specific needs. Customization is key. A popular choice is modifying shipping containers:
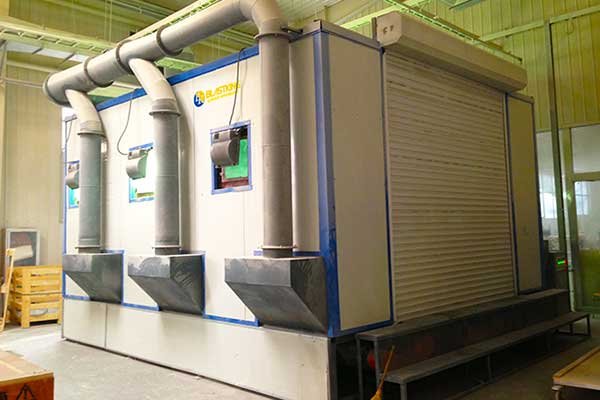
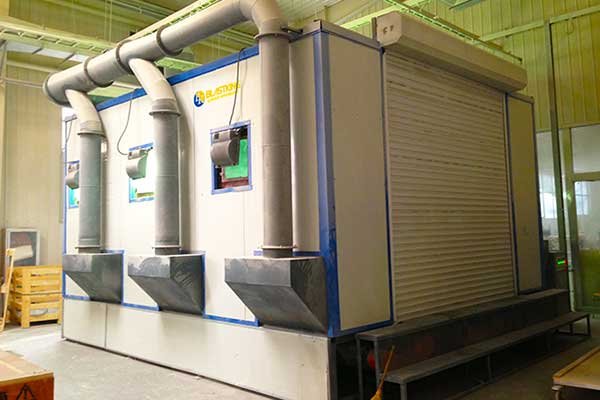
A small blast chamber which size is 3m*3m for a single blast operator
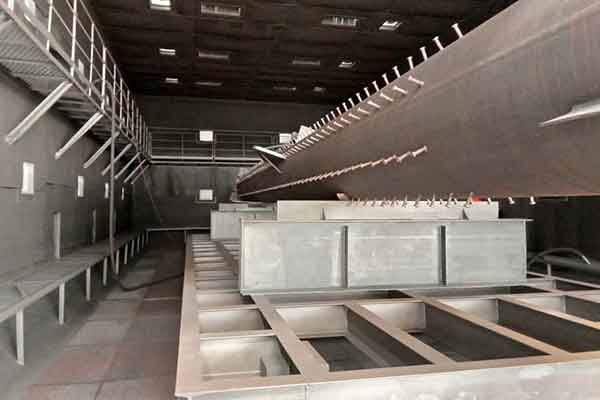
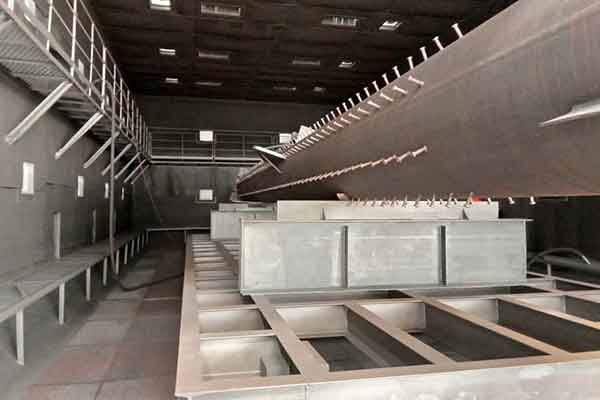
An ultra large chamber which size is 40m*40m for multiple operators
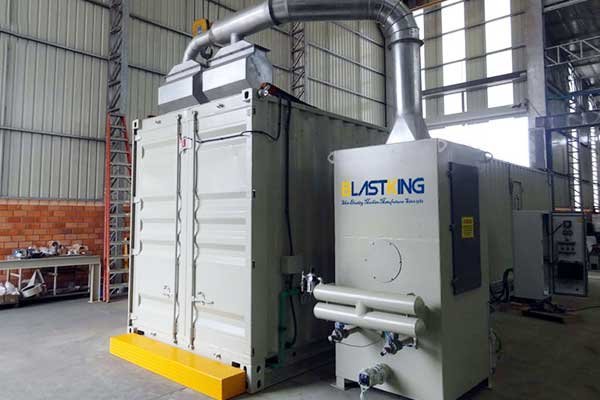
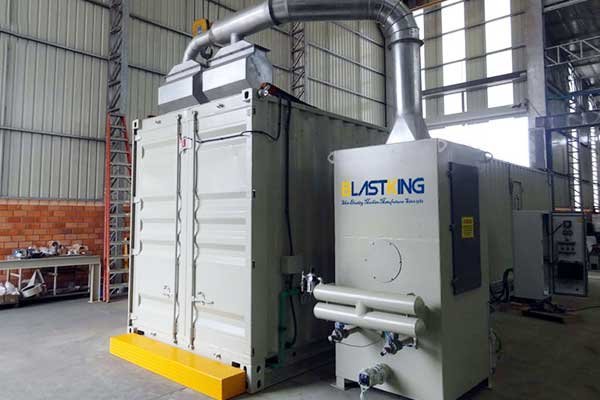
modified standard 20′ or 40′ shipping containers for blast chambers
-
Partial Blast Chamber in Shipping Containers: Picture a shipping container where part of it is your blasting chamber, and the rest houses the dust collector. It’s like having a compact, all-in-one solution. The container provides ventilation, and the abrasive recycling system is just outside, with a feed hopper inside for easy manual shoveling of spent abrasive.
-
Full Blast Chamber in Shipping Containers: In this setup, the entire container becomes your blast chamber, with the abrasive reclamation and ventilation systems neatly positioned at the rear. It’s a smart use of space, giving you a dedicated area for blasting operations.
By understanding these components and setups, you’ll have a blast room that’s efficient, safe, and perfectly tailored to your needs. Let’s make sure your operations run like a well-oiled machine.
Discover our equipment upgrades and modernisation services
Get Your Instant QuoteBlastKing’s ability to improve your business profitability is based on more than 40 years’ experience and a spirit of innovation.
3. Customized Blasting Room
Designing a customized blast room that perfectly fits your needs is like finding the right key for a lock—it has to be just right. Let’s dive into what we need to make this happen, ensuring every detail aligns with your requirements and budget.
Key Considerations:
- Workpiece Dimensions and Weight: Think of the largest and heaviest items you’ll be blasting. We need to make sure everything fits like a glove.
- Production Volume: How much work do you plan to get done? Whether it’s a steady stream or a flood, we’ll match the capacity to your pace.
- Operators and Shifts: How many hands will be on deck, and how many shifts are you running? This info helps us design an efficient setup.
- Abrasive Media Type: The type of abrasive media you’ll use is crucial. We want to choose the right one for your specific tasks.
- Installation Site: Any size constraints or unique site conditions? We’ll tailor the design to fit perfectly, no matter the space.
- Existing Equipment: Got work handling equipment already in place? We’ll integrate it seamlessly to save you time and money.
- Compressed Air Supply: What’s the scope of your compressed air supply? We need this to ensure the system runs smoothly.
- Electrical Supply: Different setups require different electrical considerations. Let’s get it right from the start.
- System Integration: Need your blast room to work well with other equipment, like a paint room? We’ll make sure everything harmonizes.
- Budget: We respect your budget and will design a solution that meets your needs without breaking the bank.
By considering these points, we’ll craft a blast room that’s not just a tool, but a perfect partner in your production process. Let’s create a space that works hard, fits right, and stays within your budget. We’re here to ensure your success every step of the way.
Say Goodbye to Downtime: Discover Our Advanced Blast Room Solutions!
Downtime is costly. Our advanced blast rooms minimize interruptions and maximize efficiency. With robust construction and innovative features, our blast rooms keep your operations running smoothly. Learn how you can reduce downtime and boost productivity with our solutions.
Call us today at +86 135 8931 7685
Construction
Building a blast chamber is like crafting a fortress. The method you choose for construction is flexible as long as the internal surfaces are protected with liners and the structure is sturdy enough to meet your expectations.
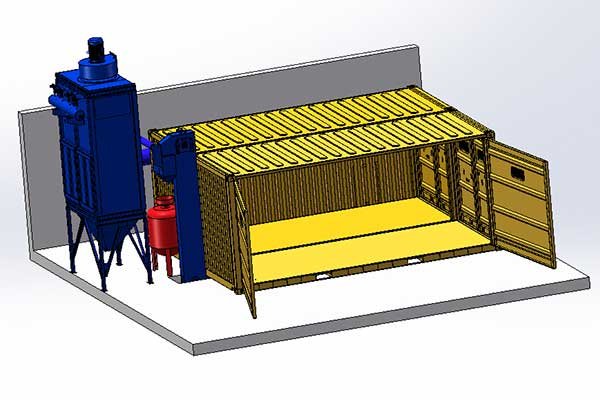
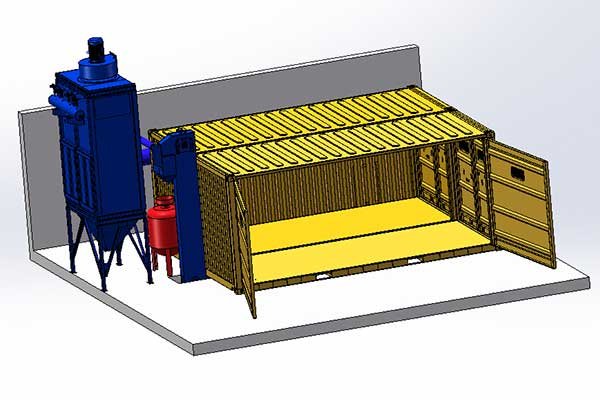
We have sandblast rooms modified by standard 20′ or 40′ shipping containers
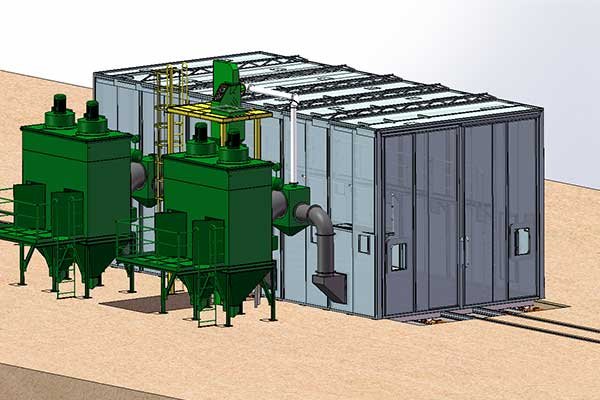
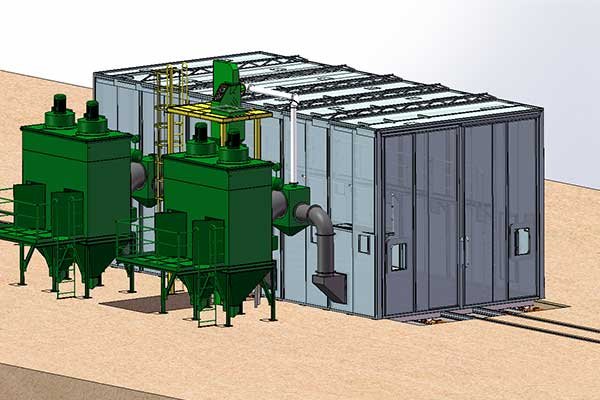
we have blast chambers made by made by profiles frame and sandwich panel with rock wool interlayer.
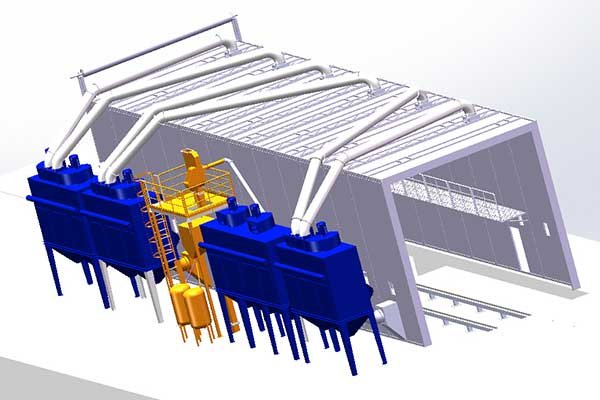
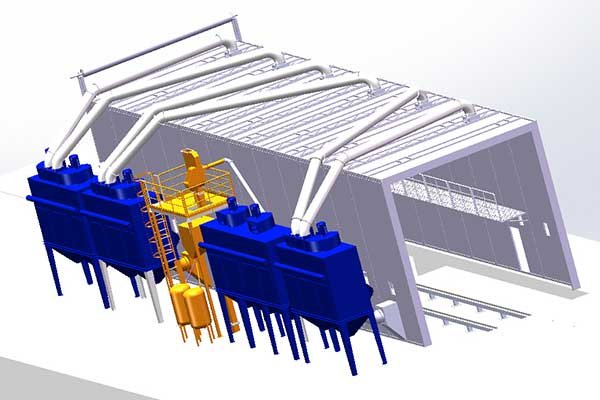
we have a chamber structure made by the assembly of standard galvanized steel sheets.
Door options for abrasive blast room
There are several door options for blast chambers, each with its unique benefits:
-
Sliding Doors: Sliding doors open sideways, similar to an elevator, providing easy access.
-
Swing Doors: Swing doors open outwards, offering a straightforward, traditional design.
-
Roller Shutter Doors: Roller shutter doors roll up, saving space as they don’t require extra floor area for door movement.
Regardless of the door type, safety is paramount. Blast chambers typically include a door interlocking mechanism to ensure blasting operations cannot start unless the doors are fully closed.
By understanding these construction and door options, you can choose the best design for your blast chamber, ensuring efficiency, safety, and space optimization.
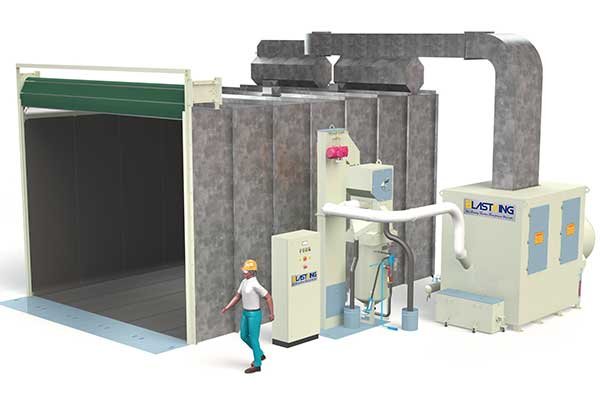
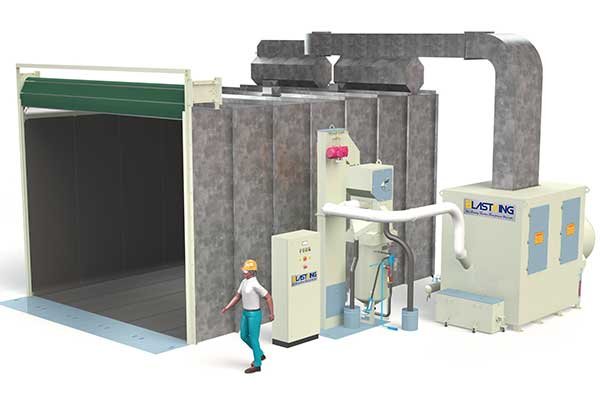
We have small blast chambers with rolled-up doors from the outside in the rolled-up position.
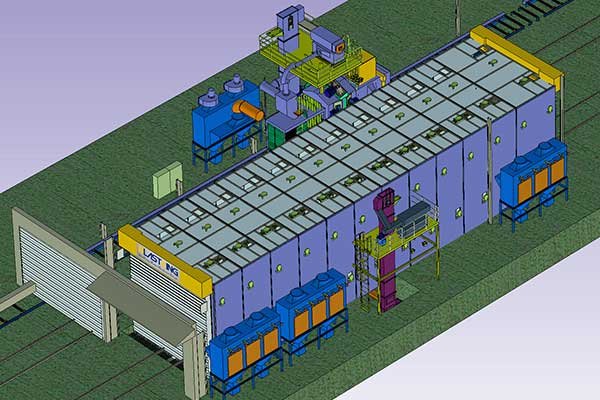
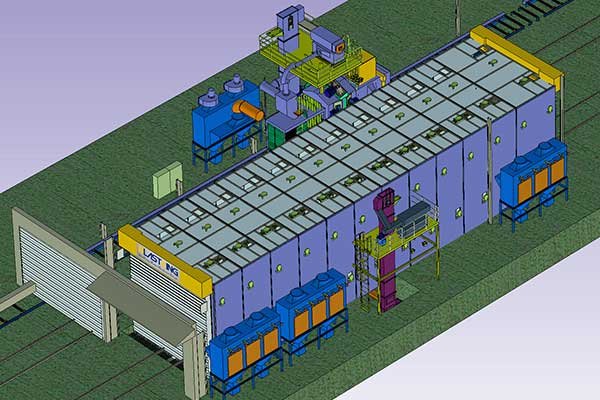
We have customized blast chambers with rolled-up doors at both ends of the blasting room.
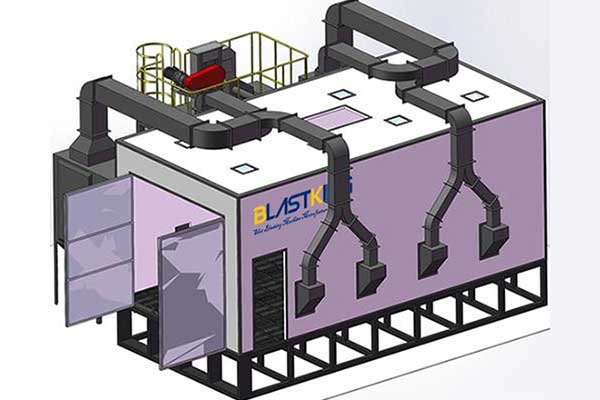
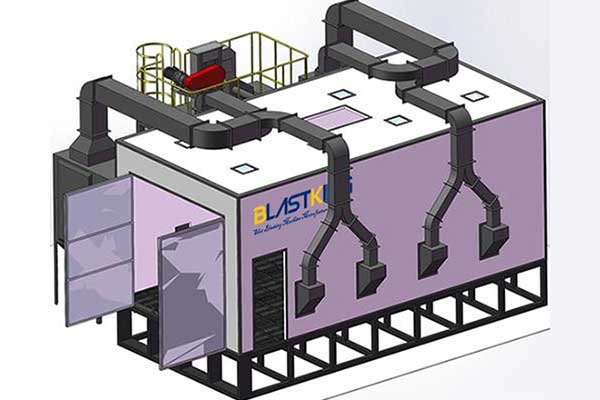
We have dual swing door styles sand blast chambers where the doors open outwards.
Key features
Let’s dive into what makes a blast chamber tick and ensure it’s working efficiently and safely for you.
-
Lighting: Imagine working in a well-lit space where you can see every detail. Not all blast chambers have ceiling lighting, but adding side lights in larger chambers can make a world of difference.
-
Access Doors: Getting in and out should be a breeze. Larger blast rooms often come with multiple access doors for convenience. In smaller rooms, the main blast chamber doors do the trick.
-
Flooring:
- Full Floor Abrasive Media Recovery: Think of industrial floor grids that let you move around freely while the system recovers the abrasive media.
- Manual Sweep Recovery: A smooth floor is your best friend here, making it easy to sweep up and recycle the abrasive media.
-
Ventilation Systems: Good airflow is key to a clear view and safe environment:
- Inlet Air Ventilation Plenum Louvers: Usually found on the roof or doors, these ensure consistent airflow.
- Dust Collector Ducting: Placed at the opposite end to create that perfect down-draft or cross-draft airflow, giving you clear visibility while you work.
-
Specialized Systems:
- BlastKing’s Waffle Pneumatic Recovery System: Picture a smart setup with air louvers spread evenly across the ceiling, optimizing ventilation and media recovery.
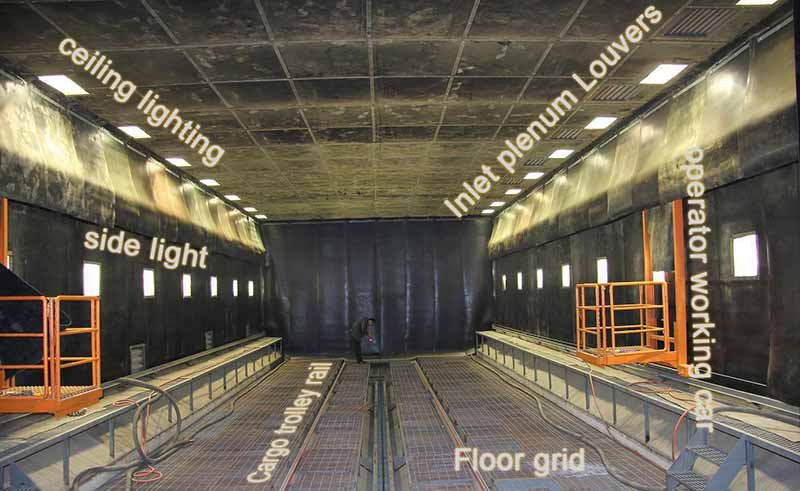
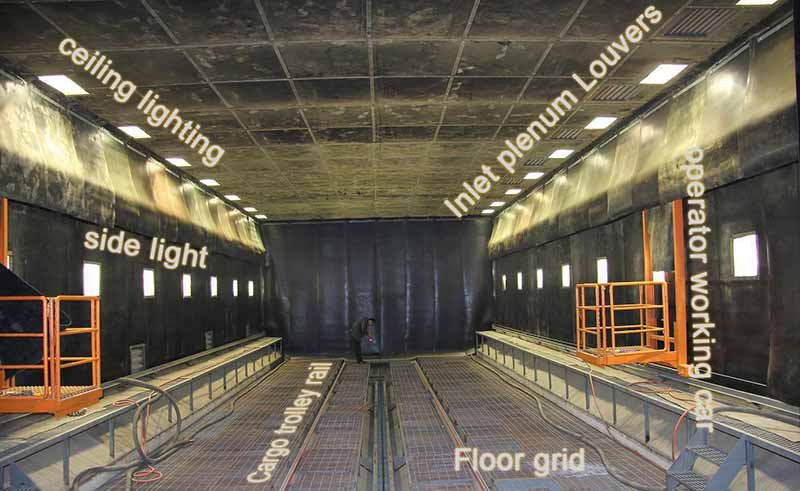
Discover our equipment upgrades and modernisation services
Get Your Instant QuoteBlastKing’s ability to improve your business profitability is based on more than 40 years’ experience and a spirit of innovation.
By incorporating these features, we ensure your blast chamber is not just functional but a joy to work in. Let’s make your workspace efficient, safe, and perfectly suited to your needs.
Work Handling in Blast Chamber
Getting your workpieces in and out of the blast chamber efficiently is crucial, and there are several ways to do it, from high-tech setups to simple, budget-friendly solutions.
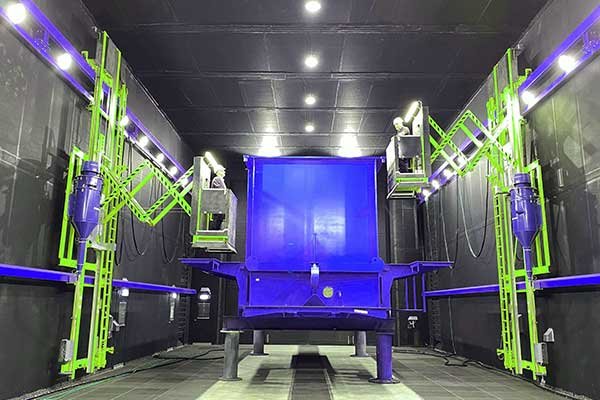
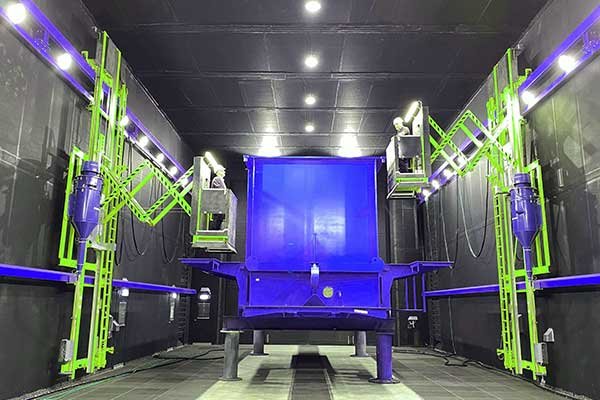
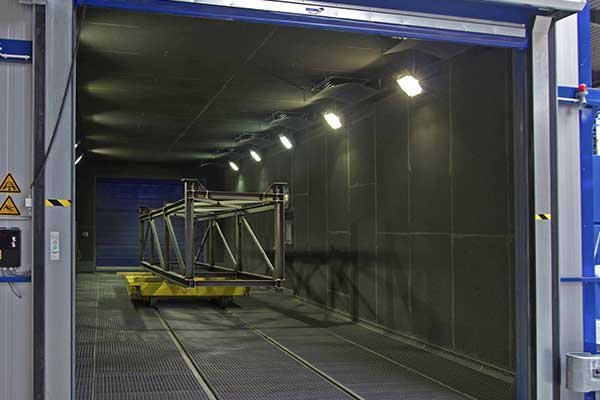
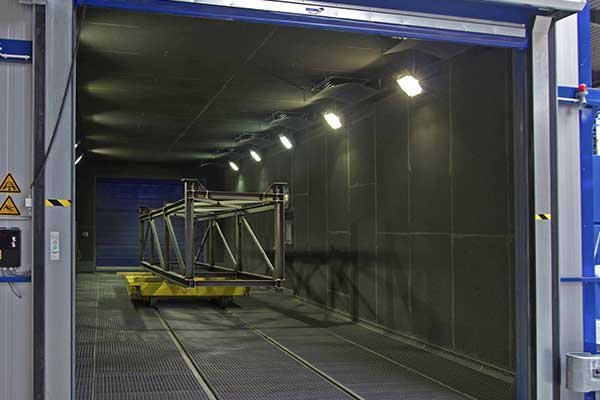
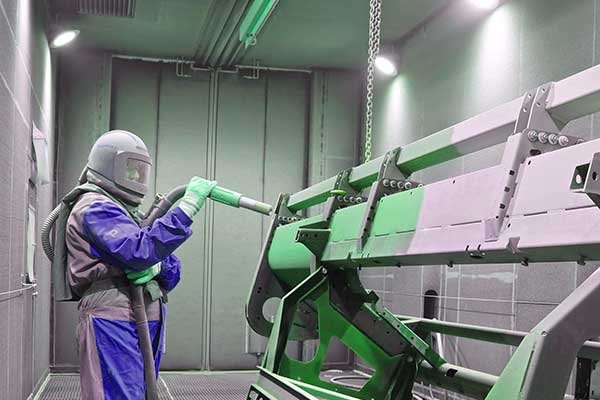
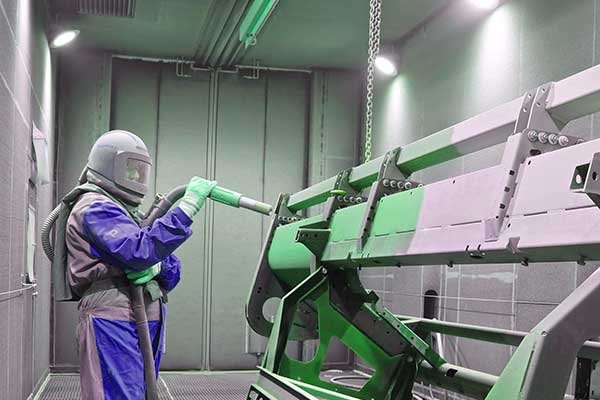
-
Mechanized Trolleys and Turntables: Imagine having a system where you can easily move along the blast chamber’s length, height, and width. Mechanized trolleys and turntables with articulated platforms make this possible. Central tracks allow workpieces to glide in and out smoothly, making the whole process a breeze.
-
Inline Production Layout: Picture a blast chamber with doors at both ends, designed for non-stop production. With multiple trolleys, you can minimize downtime—one trolley rolls in with a new workpiece as soon as the finished one exits. It’s like having a seamless conveyor belt of productivity.
-
Hoist-Crane System: Think of a hoist-crane system as your heavy-lifting hero. This setup allows you to lift and lower workpieces, ensuring even the bottoms get blasted thoroughly. It’s perfect for handling larger, heavier items with ease.
Choosing the right work handling system is like picking the right tool for the job—it ensures everything runs smoothly, efficiently, and just the way you need it. Let’s make sure your blasting operations are as seamless and effective as possible.
Optimize Your Blasting Operations with Custom-Designed Blast Rooms!
Every business is unique, and so are our blast rooms. We design each room to fit your exact specifications, ensuring optimal performance. From size to ventilation, every detail is crafted to improve your operations. Discover the power of a blast room designed just for you.
Call us today at +86 135 8931 7685
4. High-efficiency Blasting Rooms Ventilation
Imagine trying to work in a fog—frustrating, right? That’s why having a top-notch ventilation system in your sandblasting room is crucial for keeping things clear and safe. Let’s break it down.
Why Ventilation Matters
A solid ventilation system with a dust collector at the opposite end of the inlet air plenum ensures a steady crossflow of air. This setup effectively removes airborne dust and fine abrasive media, giving you the visibility you need.
Getting the Right Dust Collector Flow Rate
Here’s the secret sauce for calculating the perfect dust collector flow rate (CFM):
- Calculate the Cross-Sectional Area: Measure the blast chamber’s cross-sectional area in square feet.
- Apply the Flow Factor:
- For metallic abrasive, multiply by 30.
- For nonmetallic abrasive, multiply by 45.
- Factor in Extra Operators: Add 10% to the flow rate if more than one operator is using the blast room.
Example Calculation
Let’s say you have a blast room that’s 5m x 5m x 10m, and you’re using glass beads (nonmetallic abrasive):
- Cross-Sectional Area: 5m×5m=25 square meters=269 square feet
- Flow Rate Needed: 269 sq ft×45=12,105 CFM
- Recommended Unit: Go with the 12,000 CFM dust collector for this setup.
Picking the Right Size
BlastKing’s got you covered with dust collectors in sizes like 3000 CFM, 4500 CFM, 5000 CFM, 5500 CFM, 7500 CFM, 9000 CFM, 10000 CFM, 12000 CFM, 15000 CFM, 20000 CFM, and 30000 CFM. If your needs fall between these sizes, it’s smart to upsize to the next available option for better performance.
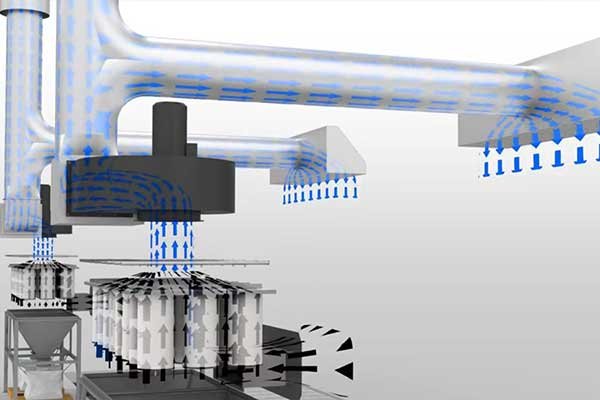
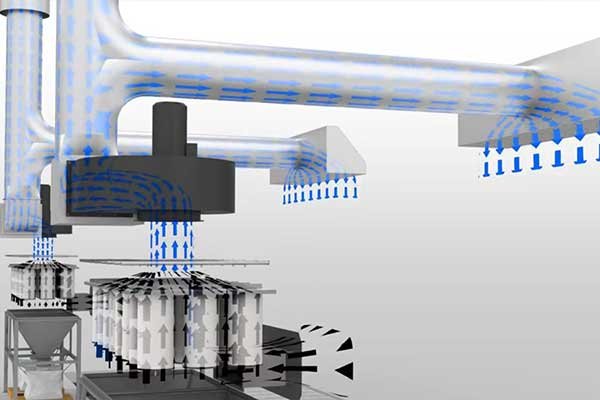
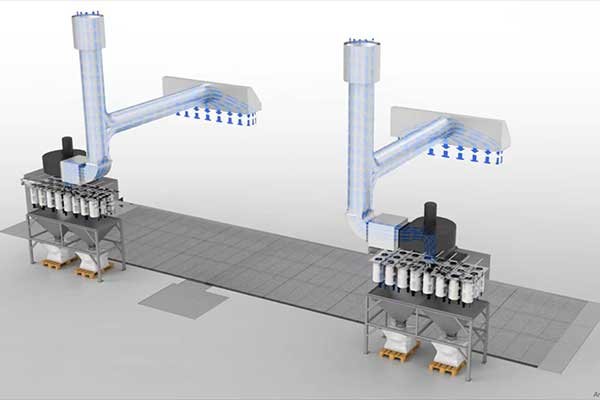
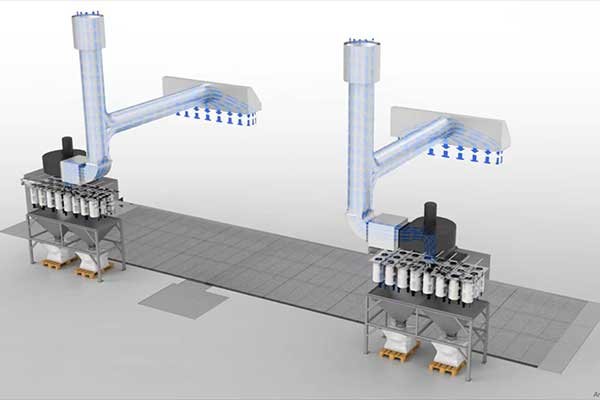
Custom Solutions
Not all blast chambers are the same, and sometimes you need a custom solution. Custom dust collectors can be tailored to fit your specific requirements, ensuring you get the best ventilation possible.
By following these guidelines, you’ll ensure your blast chamber is a clear, safe, and efficient workspace. Let’s make sure you’re working in a space where you can see everything clearly and get the job done right.
Maximize Your ROI with Durable and Efficient Blast Rooms!
Investing in a quality blast room pays off. Our durable and efficient designs ensure long-term performance and reliability, giving you the best return on investment. See how our blast rooms can save you money and enhance your operational efficiency.
Call us today at +86 135 8931 7685
5. Abrasive Recovery
Recycling and reusing abrasive media is key to efficient and cost-effective blasting operations. Let’s explore three main methods to get the job done:
1. Manual recovery
Manual recovery is the go-to for low-production blast rooms because it’s easy on the wallet. The feed hopper sits inside the blast chamber, while the rest of the system is outside.
Making Manual Recovery Easier:
- Imagine no more shoveling. By mounting the abrasive media recycling system in a pit, the feed hopper sits flush with or slightly below the blast room floor. This way, you can sweep or blow the spent abrasive directly into the hopper—no back-breaking work required!
Pit-Mounted Systems Tips:
- Keep it dry. Ensure the pit has proper drainage to prevent water from sneaking in and causing equipment failures.
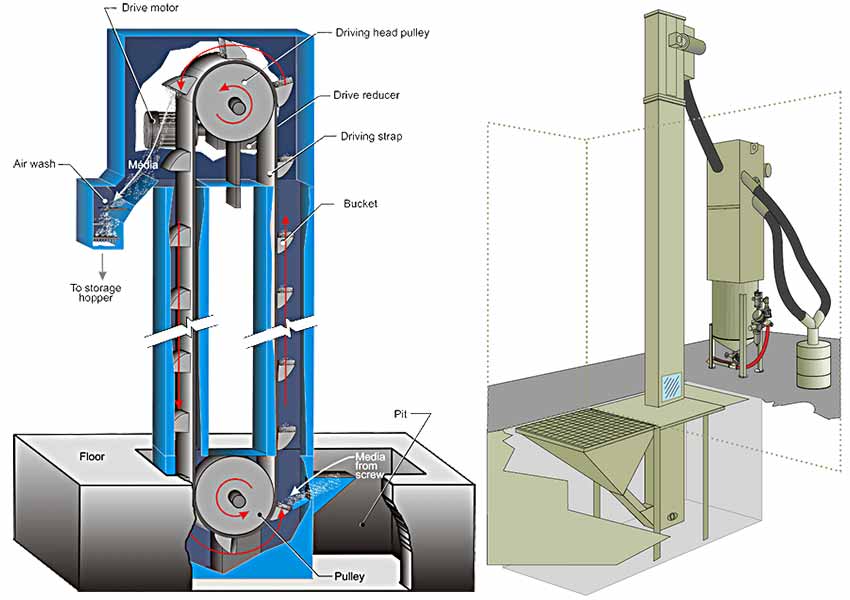
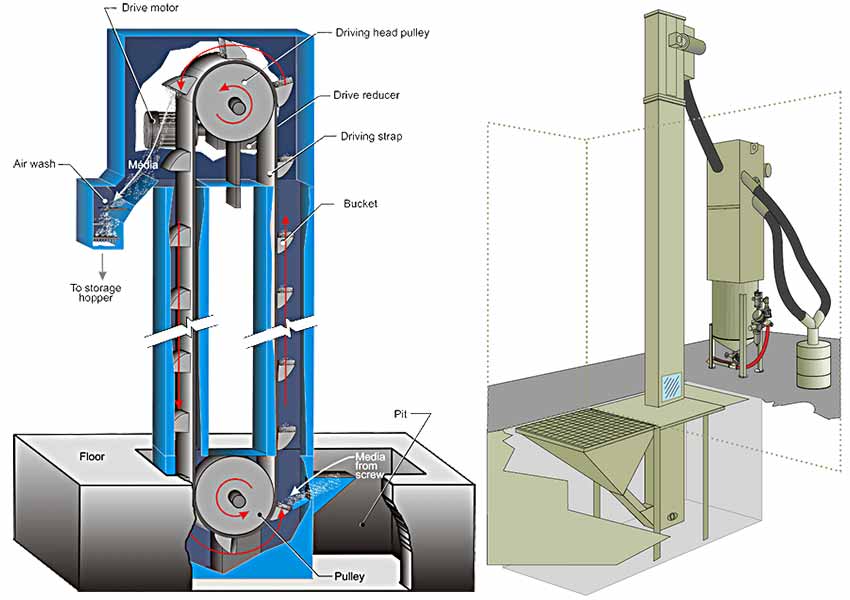
2. Mechanical Recovery
Mechanical recovery systems take the load off your shoulders by automating the process. They transport spent abrasive media into the feed hopper or directly into the bucket elevator boot.
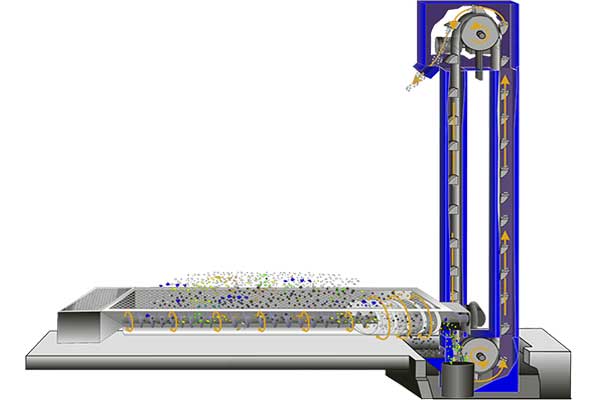
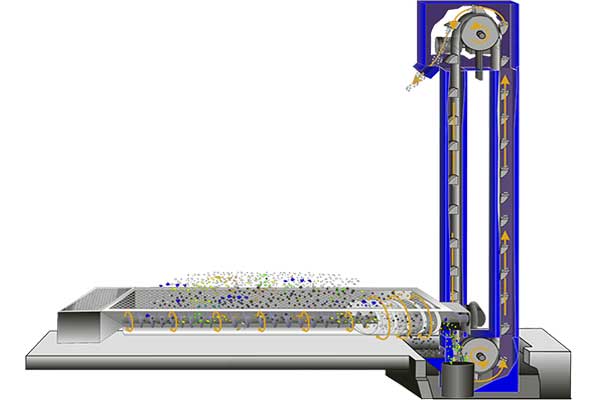
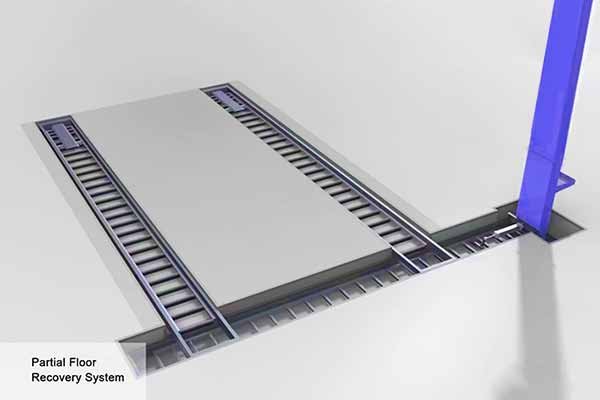
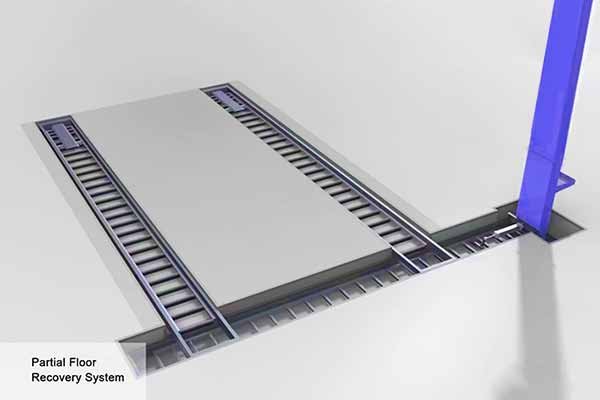
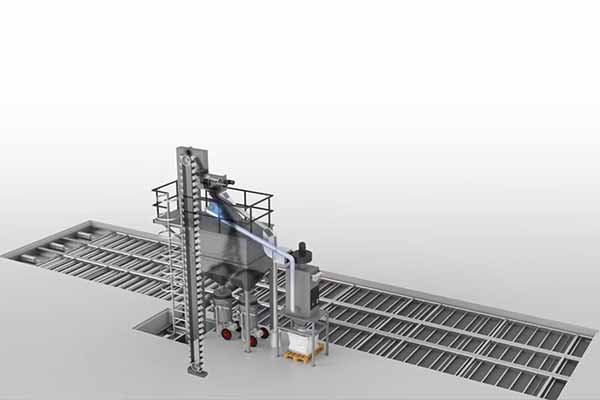
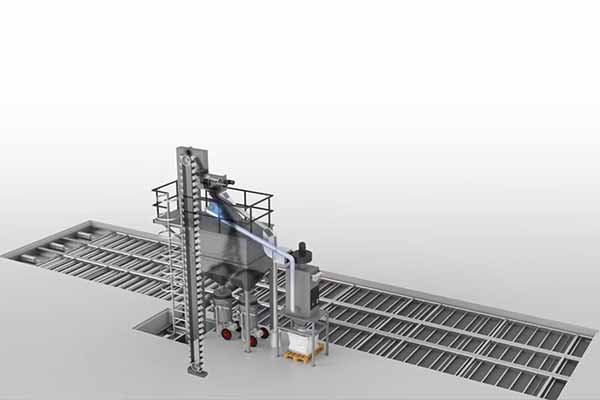
Types of Mechanical Recovery Systems:
-
Screw Conveyor Layout:
- Picture multiple screw conveyors running the length of the blast chamber, all feeding into a central screw conveyor that leads to the bucket elevator.
- Factor in Extra Operators: Add 10% to the flow rate if more than one operator is using the blast room.
Example Calculation
Let’s say you have a blast room that’s 5m x 5m x 10m, and you’re using glass beads (nonmetallic abrasive):
- Cross-Sectional Area: 5m×5m=25 square meters=269 square feet
- Flow Rate Needed: 269 sq ft×45=12,105 CFM
- Recommended Unit: Go with the 12,000 CFM dust collector for this setup.
Picking the Right Size
BlastKing’s got you covered with dust collectors in sizes like 3000 CFM, 4500 CFM, 5000 CFM, 5500 CFM, 7500 CFM, 9000 CFM, 10000 CFM, 12000 CFM, 15000 CFM, 20000 CFM, and 30000 CFM. If ng>
- Imagine rows of scraper conveyors on the blast chamber floor, each feeding into a central scraper conveyour nede sizes, it’s smart to upsize to the next available option for better performance.
Partial Floor Recovery Systems:
- In partial systems, the operator sweeps spent abrasive to the nearest conveyor, reducing the number of individual conveyors needed.
By selecting the right abrasive recovery method, you can enhance efficiency and sustainability in your blast room operations.
3. Pneumatic Recovery
Picture a system where air does all the heavy lifting—literally. Pneumatic recovery systems use air to transport abrasive media efficiently. These systems come in modular designs that don’t require foundation pits, with recovery floors as low as 20cm. This setup can significantly cut down on construction costs and save valuable time.
Understanding these recovery methods lets you choose the perfect system to boost efficiency and keep costs in check. Imagine a blast room that runs like a well-oiled machine, making your job easier and your operations smoother. Let’s find the right fit for you and keep things running seamlessly.
Enhance Safety and Visibility with Our High-Performance Blast Rooms!
Safety and visibility are critical in blasting operations. Our blast rooms are equipped with top-notch ventilation and dust collection systems, providing a clean and safe environment. Ensure the safety of your operators and maintain high visibility with our superior solutions.
Call us today at +86 135 8931 7685
6. FAQs (Frequently Asked Questions)
Q1: What is the primary purpose of a blast room?
When it comes to industrial cleaning, a blast room is your secret weapon. Imagine trying to scrub a rusty old ship with a toothbrush—tedious, right? A blast room is designed to handle heavy-duty tasks like this with ease. Its primary purpose is to provide a controlled environment where abrasive blasting can be performed safely and efficiently.
Think of a blast room as a high-tech car wash for industrial equipment. Instead of water and soap, it uses abrasive materials to clean surfaces, remove rust, and prepare items for painting. This process not only saves time but also ensures a thorough clean, making sure every nook and cranny is spotless.
Safety is another key element. Imagine a bustling workshop where dust and debris are flying everywhere—chaotic and dangerous. A blast room contains the mess, preventing harmful particles from spreading. This protects workers and keeps the workspace clean, which is crucial for maintaining a productive environment.
Ever heard the saying, “A stitch in time saves nine”? Using a blast room can extend the lifespan of your equipment. Regular blasting prevents corrosion and wear, reducing the need for costly repairs or replacements. It’s like giving your machinery a new lease on life.
Efficiency is where the blast room really shines. Picture trying to paint a fence with a toothbrush—ineffective and exhausting. A blast room’s advanced technology ensures a consistent, high-quality finish every time. This means less rework and more time to focus on other important tasks.
In a nutshell, a blast room is essential for any industry dealing with large, dirty, or rusty items. It provides a safe, efficient, and thorough cleaning process, protecting your investment and ensuring your equipment is always in top condition. So next time you think about industrial cleaning, remember the blast room—it’s not just a room; it’s a game-changer.
Q2: Can blast rooms accommodate large objects?
Absolutely, blast rooms can accommodate large objects, and here’s why they’re an ideal solution for your heavy-duty needs.
Imagine trying to clean a massive steel beam with a handheld tool—like trying to dig a well with a teaspoon. It’s just not practical. That’s where blast rooms come in. They’re designed to handle the big stuff, making them indispensable for industries dealing with large and heavy components.
Think about a shipyard. The hull of a ship is gigantic, right? You can’t exactly fit that in a small cabinet blaster. Blast rooms provide the space needed to maneuver and treat these large surfaces efficiently. It’s like having a football field where you can play freely, compared to being cramped in a tiny backyard.
But it’s not just about size. Blast rooms are customizable. You can configure the space, ventilation, and abrasive recovery systems to suit the specific needs of your projects. This flexibility ensures that even the most cumbersome objects are treated effectively, without compromising on safety or efficiency.
Consider the story of a wind turbine manufacturer who struggled with cleaning their enormous turbine blades. Traditional methods were slow and inefficient. Switching to a blast room transformed their process, allowing them to handle the blades with ease, improving their turnaround time, and boosting their overall productivity.
Blast rooms also enhance worker safety. Instead of struggling with awkward angles and confined spaces, workers have the room to move and operate equipment properly. This reduces fatigue and the risk of accidents, making the workplace safer and more productive.
In short, if your business involves large, heavy objects, a blast room isn’t just a good option—it’s a game-changer. It’s like upgrading from a bicycle to a jet plane. The efficiency, safety, and flexibility you gain are unparalleled, ensuring your operations run smoother and faster. So, don’t settle for less; make sure your blast room is ready to handle the big jobs.
Q3: What types of abrasive media can be used in a blast room?
When it comes to blast rooms, choosing the right abrasive media can be a game-changer. Let’s dive into what works best.
First up, steel shot or steel grit. This one’s a heavyweight champ, perfect for heavy-duty cleaning and surface preparation. Think of it as the tough guy in your toolkit, breaking down the toughest rust and coatings. Next, aluminum oxide. It’s sharp, reusable, and great for getting a smooth finish. Imagine it as the precision surgeon, making sure your surfaces are flawless.
Then there’s glass beads. These are the gentle giants, ideal for polishing and peening without damaging the surface. It’s like using a feather duster but with the power to clean deeply. And don’t forget garnet. Known for its eco-friendly nature and high efficiency, garnet is the eco-warrior of abrasive media. It’s tough on contaminants but kind to the environment.
Plastic abrasives are the specialists, best for delicate tasks like aircraft maintenance. They’re the gentle touch, ensuring no harm while doing their job. Lastly, silicon carbide. This is the speedster, cutting through surfaces quickly and efficiently. It’s your go-to when time is of the essence.
Choosing the right abrasive media isn’t just about getting the job done; it’s about doing it efficiently and effectively. So, what’s your abrasive media of choice?
Q4: How does a media recovery system work?
Have you ever wondered what happens when media gets contaminated in industrial processes? A media recovery system is the unsung hero that ensures efficiency and sustainability. Let’s dive into how it works.
Imagine you’re cleaning a large ship’s hull. The blasting media—tiny abrasive particles—gets contaminated with paint and rust. This is where the media recovery system steps in. Think of it as a diligent recycling plant. First, it collects the spent media and debris through a vacuum or mechanical conveyor. Then, it separates the usable media from waste.
The separation process is akin to panning for gold. The system uses screens, magnetic separators, and air wash classifiers to sift through the media. Clean media is returned to the hopper for reuse, while contaminants are disposed of. This not only saves costs but also minimizes environmental impact.
Picture this: instead of constantly buying new media, you’re reusing what you already have. It’s like turning yesterday’s leftovers into a gourmet meal. Plus, it keeps your operation running smoothly, avoiding unnecessary downtime.
In essence, a media recovery system is your reliable partner in maintaining operational efficiency and sustainability. It’s the little engine that could, tirelessly working behind the scenes to keep everything on track.
Q5: What safety measures should be taken when operating a blast room?
Operating a blast room safely is essential to ensure both efficiency and the well-being of operators. Let’s dive into the must-do safety measures.
First and foremost, personal protective equipment (PPE) is non-negotiable. Wearing a blast helmet, heavy-duty gloves, and an appropriate suit shields you from abrasive particles. Think of it like suiting up for battle; you wouldn’t go in unarmed, right?
Proper ventilation is key. Ensure your blast room has a robust dust collection system. Imagine working in a fog; not only is it hard to see, but it’s also tough to breathe. Clear air means clear vision and safe breathing.
Regular maintenance checks are crucial. A stitch in time saves nine, as they say. Inspect hoses, nozzles, and seals frequently to prevent unexpected failures.
Emergency protocols should be well understood. Everyone should know the drill, literally. Quick access to emergency exits and communication devices can be life-saving.
Training is the cornerstone of safety. Equip your team with the knowledge and skills they need. Remember, a well-trained team is like a well-oiled machine, running smoothly and safely.
Lastly, never rush. Safety is no accident. Take the time to follow procedures meticulously. After all, better safe than sorry!
7. Conclusion
Blast rooms revolutionize industries by providing a safe, controlled space for abrasive blasting. They enhance safety, efficiency, and cost-effectiveness. Understanding how blast rooms work and their benefits is crucial for maximizing their potential.
Investing in blast rooms is a step toward quality and efficiency. With the right knowledge and practices, your operations will not just improve—they will thrive. A well-prepared surface is the foundation of excellent work, and blast rooms are the ideal tool to achieve that.
In addition to standard and custom blast rooms, BlastKing specializes in designing and developing automated shot blasting machines. Contact us to learn more and elevate your operations!
Get A Strong Partner at Your Side Now!
Consult your dedicated surface preparation equipment experts to make your business succeed!
Call us today at +86 135 8931 7685