BlastKing’s surface preparation machine customers enjoy high quality, cost-saving, and efficient operation of blast machines.
Barrel Blasting Machine: A Comprehensive Guide to Selection and Use
Updated: August 12, 2025
Deburring, rust removal, and surface prep, all done in a snap? Yes, please! Discover the magic of barrel blasting machines. They don’t just clean metal—they transform it. Ready to take your industrial cleaning game up a notch?
Outline
1. Introduction
A barrel blasting machine is a tool for cleaning and preparing metal surfaces by removing rust, paint, and contaminants. It uses abrasive media to blast surfaces, delivering quick, efficient results. These machines are essential in industries that require high productivity and consistent surface quality.
2. What is a Barrel Blasting Machine?
The BlastKing Barrel Blast Machine uses a rotary barrel for tumbling action, making sure all surfaces of the workpieces get cleaned in a single load. These heavy-duty machines are built tough to clean all kinds of castings, forgings, weldments, heat-treated parts, and stampings.
Our barrel-type shot blast machines can handle a wide range of tumbling workpieces, thanks to the recirculating conveyor belt and annular side spaces that form a tank-like setup to process the pieces efficiently.
3. Features
- Single piece barrel design that eliminates pinch points
- Fully welded construction with abrasive resistant steel in the bottom and sloped walls where blast media flows
- Access panels are provided in the blast cabinet for ease of maintenance
- Equipped with ORICA blast wheels for faster cleaning cycles and superior durability
- The barrel rotation and work door are operated by a hydraulic cylinder
4. Applications
- Suitable for a variety of processes, including deburring, rust removal, core and sand removal, burr removal, and shot peening
- When production volume requires batch processing
- Small to medium-sized castings, fabricated parts, and heat-treated workpieces.
- Batch shot peening of small springs.
- Lower value parts when impact between parts is not an issue
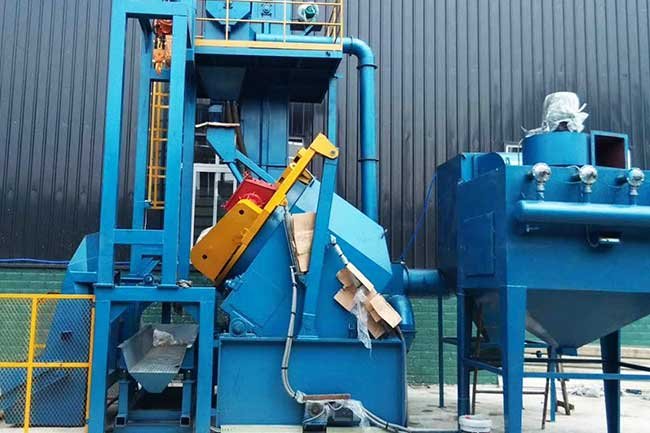
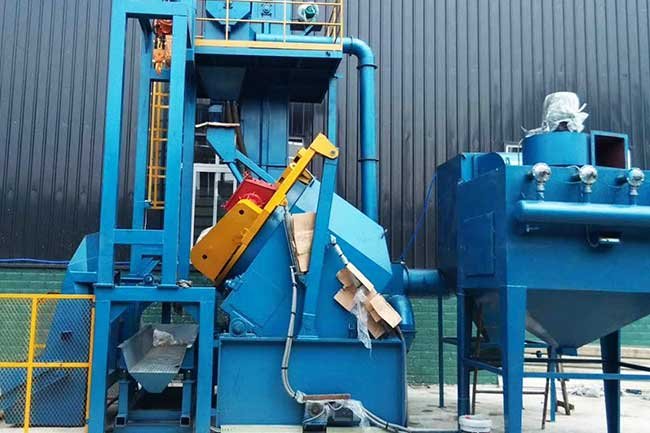
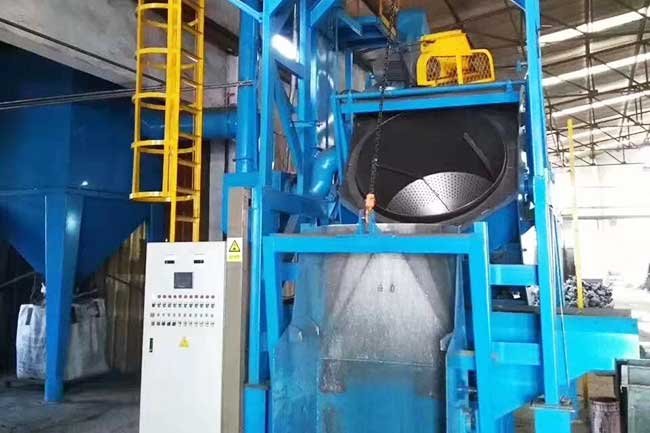
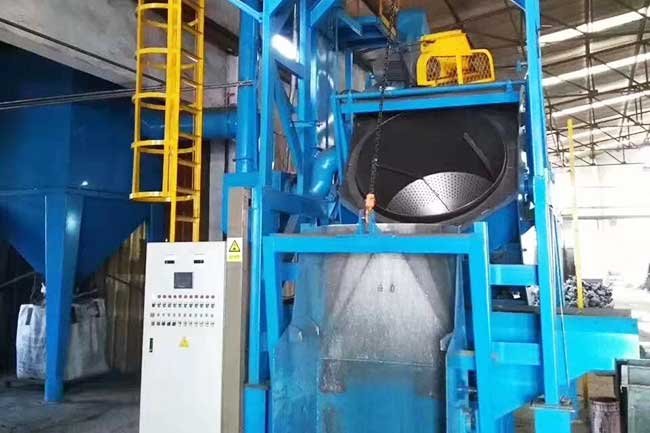
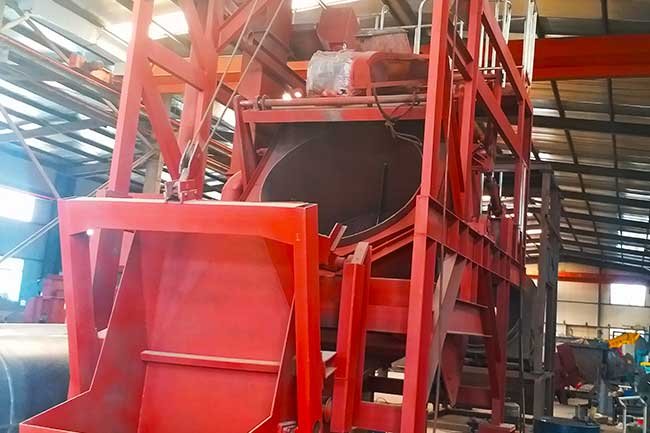
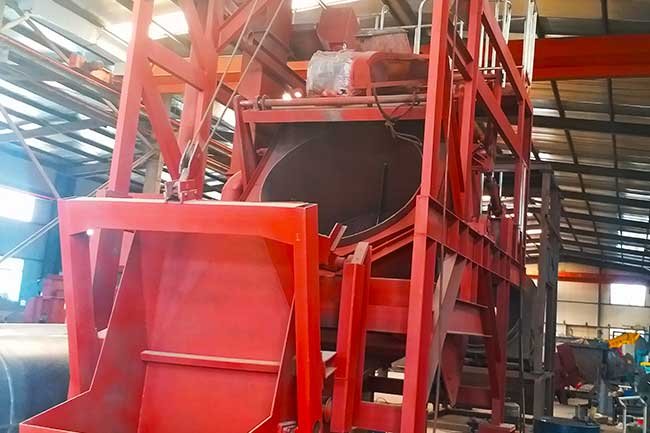
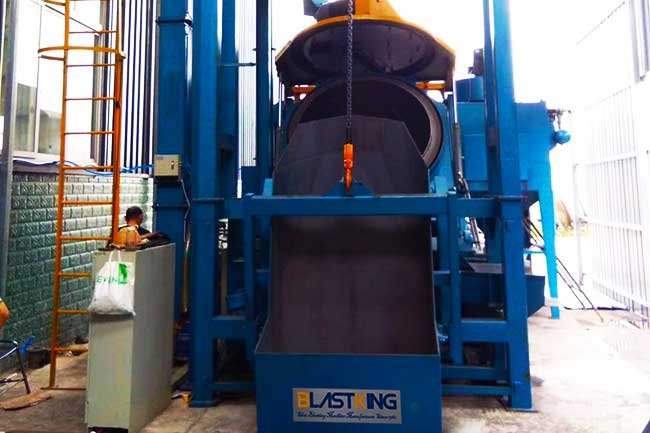
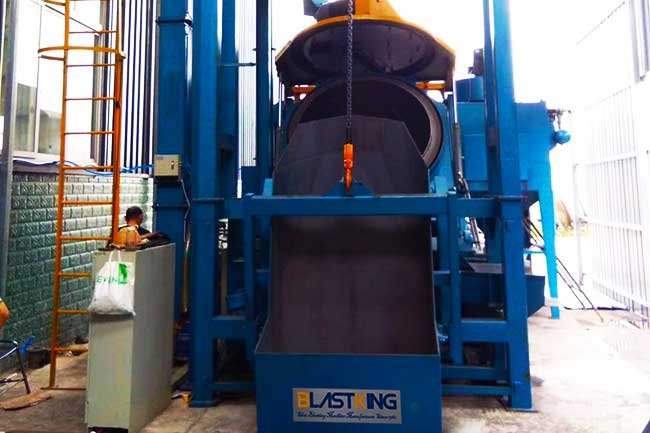
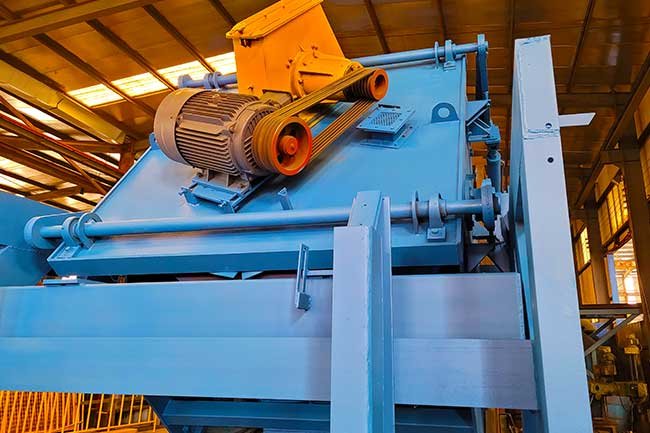
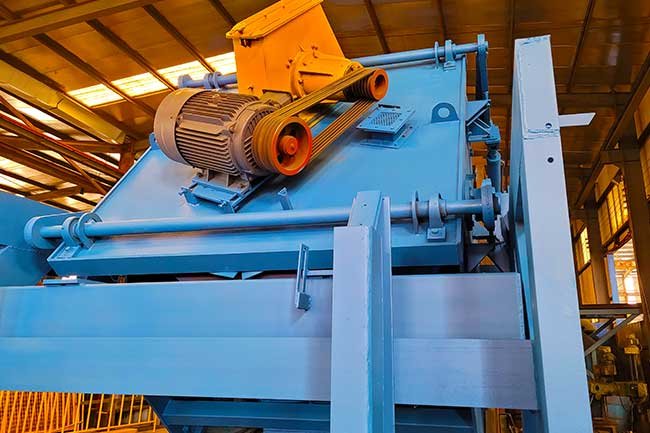
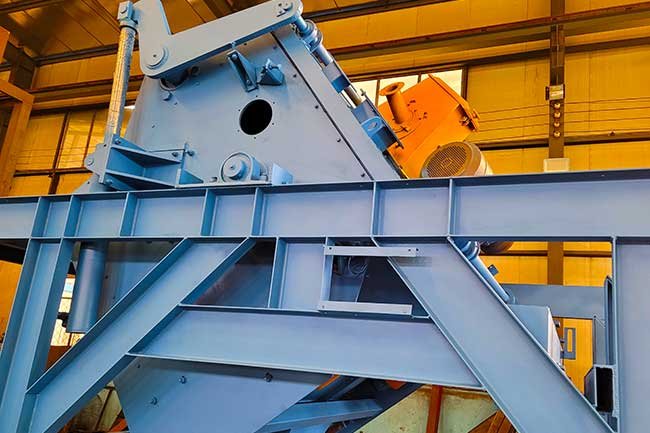
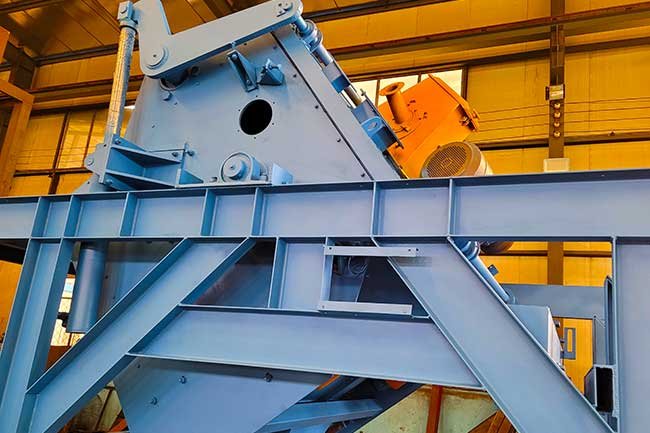
5. Advantages of Using Barrel Blasting Machines
Why should you care about a barrel blasting machine? Simple — it makes life easier and work faster. Here’s how:
Saves Time
Imagine scrubbing each part by hand. Now imagine that you never have to do that again. That’s what these machines do. They cut the cleaning process down to minutes, not hours.
Consistent Results
Because the parts are constantly tumbling, every surface gets cleaned evenly. There’s no guesswork or missing a spot — just clean, consistent results every time.
Versatility
From rust removal to deburring, these machines do it all. Whatever your metal parts need, they’ve got you covered.
Barrel Blaster High Capacity
If you’ve got a ton of parts to process, these machines won’t even break a sweat. With larger models, you can load up batch after batch and keep things moving.
Unmatched Durability and Easy Maintenance!
Concerned about the longevity and upkeep of your equipment? Our barrel shot blasters are built with high-quality materials for unmatched durability. Plus, our comprehensive maintenance plans ensure your machines stay in top condition, minimizing downtime and maintenance costs.
Call us today at +86 135 8931 7685
6. Batch Type Barrel Shot Blasting Machine
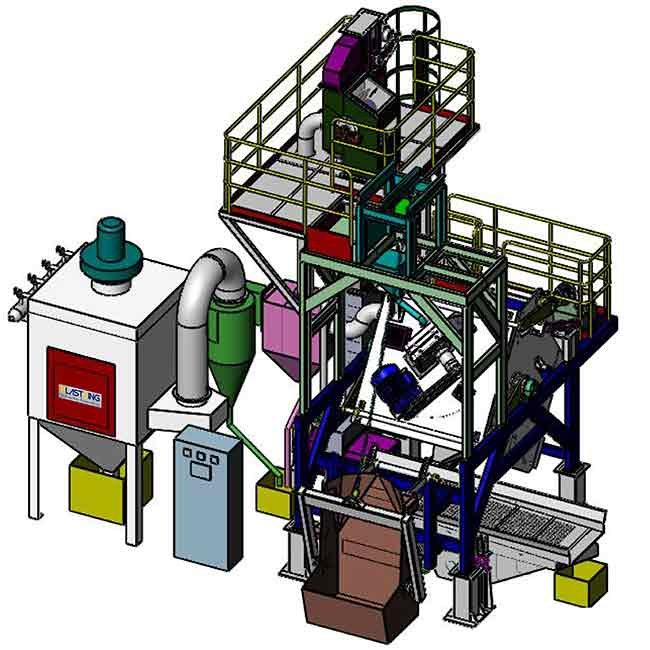
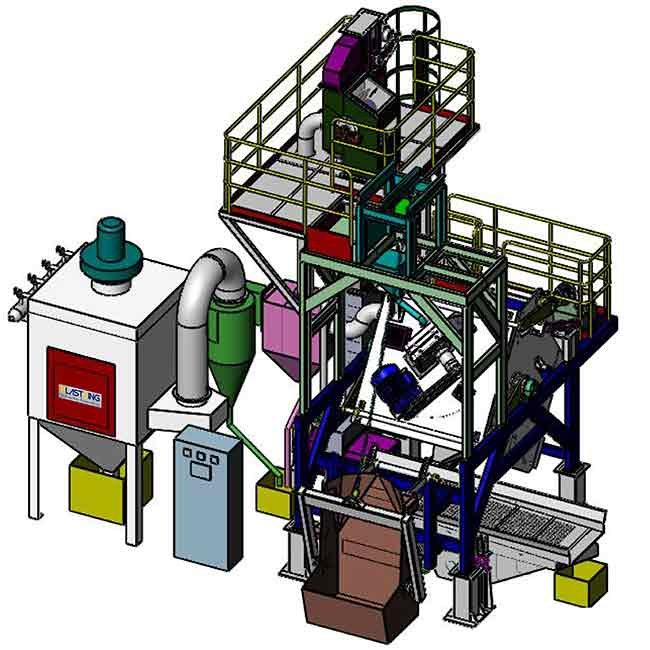
This machine is like the Swiss Army knife of shot blasting—it’s got everything you need. Picture a tilting barrel that rotates your workpieces, a cleaning body, a blasting turbine that works like a charm, and even a dust removal system to keep things tidy. It’s like the machine runs its own little cleaning crew!
Now, here’s the fun part: it uses some serious 3D computer smarts to position the blasting turbines just right. No wasted steel shots flying off into the distance! Everything hits exactly where it needs to, making sure your barrel liner doesn’t take a beating and your steel shot is used efficiently. That’s what we call getting the most bang for your buck!
And don’t worry, safety’s front and center too. The door has a travel switch, meaning it only opens and closes when it’s supposed to. The whole thing is welded together with strong steel sections and plates, so you won’t have to deal with a flimsy or warped door anytime soon.
It’s built to last, work hard, and make your life a whole lot easier—what more could you ask for?
7. Working Video
8. FAQs (Frequently Asked Questions)
Q1: What are barrel type shot blasting machines used for?
Barrel-type shot blasting machines are like the unsung heroes of metal finishing. These specialized machines tackle the tough jobs of cleaning, deburring, descaling, and surface finishing for small to medium-sized metal components. If you’ve got parts that can handle a bit of tumbling without risk, these machines are perfect for batch processing.
Here’s how it works: you load the components into a rotating barrel or drum. As it spins, the parts tumble around while abrasive media is shot at them at high speeds. It’s like a high-energy car wash for your metal pieces. The tumbling and blasting combo ensures every surface gets a uniform treatment, stripping away scale, rust, and any other stubborn contaminants. By the end of it, you’ve got a clean, roughened surface—ideal for whatever comes next, whether it’s painting, coating, or assembly.
Industries like automotive, aerospace, and metalworking swear by these machines for prepping everything from gears and bolts to castings and forgings. Take BlastKing’s barrel blasting machine, for example. It’s built to handle a variety of materials and part sizes, offering flexibility and high productivity. Plus, its solid construction and cutting-edge blasting tech make it a beast when it comes to continuous use in tough industrial settings.
In short, barrel-type shot blasting machines are game-changers when it comes to surface prepping. They don’t just clean; they get your components ready to perform better and last longer.
Q2: How does a barrel type shot blasting machine work?
The barrel-type shot blasting machine is like the ultimate cleaning crew for small to medium-sized workpieces. Picture this: you load your parts into a rotating barrel or drum, and as it turns, the pieces tumble around, making sure every surface gets its fair share of the blasting action.
Inside the machine, high-velocity abrasive media is fired by blast wheels straight at the tumbling parts, knocking off rust, scale, and other stubborn grime. The continuous spinning and tumbling guarantee that every part gets a nice, even finish—perfect for prepping them for painting, coating, or whatever’s next in line.
One thing that sets BlastKing’s barrel blaster apart is its ability to handle large quantities without breaking a sweat. It’s like having an automated workhorse that takes care of the dirty work for you, cutting down on manual labor and boosting productivity. Plus, it’s smart! It separates the cleaned parts from the abrasive media, which means you can recycle the media and easily retrieve your freshly cleaned workpieces.
On top of that, the machine is built for long-lasting use and smooth operation. It’s equipped with dust collection systems to keep your workspace clean and safe, and its rugged design ensures it can take a beating without wearing down too soon.
Q3: What types of abrasive media are used in barrel shot blasting machines?
Barrel shot blasting machines, use a variety of abrasive media to clean and finish metal parts effectively. The choice of abrasive depends on the material of the workpieces and the desired surface finish.
Here’s a quick rundown of some common abrasive media:
-
Steel Shot: Think of it as the smooth operator—spherical steel particles that are perfect for cleaning, peening, and polishing metal surfaces. It leaves a smooth finish and can be reused multiple times.
-
Steel Grit: More aggressive than steel shot, steel grit is like the heavyweight champ of rust and paint removal. It’s angular and great for creating a rough texture, perfect for coating adhesion.
-
Stainless Steel Shot: This is your go-to for non-ferrous metals or stainless steel parts when you don’t want to risk ferrous contamination. It cleans thoroughly without messing with the dimensions of precision parts.
-
Cut Wire Shot: Imagine tiny cylinders of steel wire—cut to the wire’s diameter. Available in carbon steel, stainless steel, aluminum, and zinc, cut wire shot delivers consistent results for both peening and finishing.
The BlastKing Barrel Blast Machine is built to handle all of these abrasive types like a pro. Its tumbling action ensures that every part gets evenly exposed, giving you a consistent clean and finish every time. By choosing the right abrasive, you can fine-tune the process to match your exact needs, whether you’re deburring, descaling, or prepping for a fresh coat of paint.
-
Q4: How long does the shot blasting process take?
The duration of the shot blasting process varies based on factors such as the type of equipment used, the material of the workpieces, and the desired surface finish. When using the BlastKing’s Barrel Blasters, the process is designed for efficiency and consistent results for small to medium-sized components.
The BlastKing’s Barrel Blasters are a batch-type tumblast machine that cleans workpieces by tumbling them in a barrel while blasting media is propelled onto their surfaces. This method ensures all parts of the workpieces are uniformly treated. Typically, a shot blasting cycle can range from 5 to 20 minutes per batch. The exact time depends on several factors:
- Material Composition: Tougher materials or heavily corroded pieces might need more time to clean thoroughly.
- Surface Condition: If your parts are covered in rust, scale, or old coatings, they’ll need extra attention.
- Desired Surface Finish: Going for a smooth, refined look? That might take a bit longer.
- Blasting Media: The type of media you’re using—its size and hardness—can also impact how fast things move.
BlastKing’s Barrel Blasters are designed to move quickly without cutting corners on quality. They’re built for continuous operation, so whether you’re in automotive, metalworking, or a foundry, you can keep things moving smoothly and efficiently.
In short, shot blasting with the Barrel Blaster usually takes 5 to 20 minutes per batch, but it’s all about the specifics of your job. If you want more detailed advice for your setup, the operational guidelines or a quick chat with BlastKing will point you in the right direction!
Q5: What maintenance is required for barrel type shot blasting machines?
Keeping your barrel-type shot blasting machine, like BlastKing’s Barrel Blast Machine, in tip-top shape is crucial for getting the most out of it. A little maintenance goes a long way! Here are some key things to keep an eye on:
1. Inspection of Wear Parts:
Think of this like checking your car’s tires. Regularly inspect wear-prone parts like blades, liners, and seals. If they’re looking worse for wear, replace them ASAP—waiting too long could hurt your machine’s efficiency or even cause damage.2. Blast Wheel Maintenance:
The blast wheel is the heart of the operation. Make sure the wheel blades, control cages, and impellers are in good condition. Worn parts can mess up the blasting pattern, which means less effective cleaning. And who wants that?3. Abrasive Media Management:
Keep an eye on those abrasive media levels. If the quality drops or there’s too much contamination, your performance will take a hit. Keep the media clean and top it off when needed.4. Dust Collection System:
Nobody likes a dusty mess! Make sure the dust collector filters are cleaned or replaced regularly. A clogged filter can lead to a dirty workspace and could affect your machine’s components over time.5. Lubrication:
A well-oiled machine is a happy machine. Follow the manufacturer’s guidelines and regularly lubricate moving parts to reduce friction and wear. This simple step can extend the life of your machine’s components.6. Electrical System Checks:
Give the electrical connections, switches, and control panels a once-over. Check for signs of wear and make sure safety interlocks and emergency stops are working properly. Better safe than sorry!7. Barrel and Conveyor Inspection:
For machines like BlastKing’s Barrel Blaster, check the barrel or conveyor for any signs of wear or damage. You want a smooth rotation and no blockages that could slow things down.8. Safety Features Verification:
Make it a habit to regularly test all safety features. Whether it’s doors, sensors, or guards, everything should be in top working order to keep you and your team safe.9. Calibration and Settings:
Every now and then, check your machine’s settings and calibration. Make sure everything is fine-tuned to match BlastKing’s specifications for the best performance.10. Documentation and Scheduling:
Keep good records of your maintenance activities. A scheduled maintenance plan will help you stay ahead of any issues and allow you to replace parts before they fail.By sticking to these maintenance tips, you’ll keep your Barrel Blast Machine running like a champ, minimize downtime, and get a long life out of it. And, of course, always refer to the manufacturer’s manual for specific instructions and schedules tailored to your machine.
Q6: Are barrel type shot blasting machines environmentally friendly?
Barrel type shot blasting machines, like BlastKing’s Barrel Blast Machine, are the go-to solution for cleaning and prepping small to medium-sized metal components. Using high-speed steel shot or grit, they efficiently remove rust, scale, and other surface contaminants. But there’s more to these machines than just power—they’re designed with the environment in mind.
Environmental Considerations:
- Dust and Emission Control: Nobody wants a cloud of dust hanging around, right? That’s why modern machines like BlastKing’s come equipped with top-notch dust collection systems. These systems trap the dust and debris generated during blasting, keeping the air cleaner for both the workers and the planet.
- Media Recycling: One of the coolest things about BlastKing’s machines is their ability to recycle blasting media. They’re designed to separate usable media from dust and waste, making sure that nothing goes to waste. This means you’re not only saving resources but also cutting down on the garbage pile-up.
- Energy Efficiency: Let’s talk energy. BlastKing’s Shot Blaster uses advanced tech to keep energy use in check. Compared to older models, these machines are like the fuel-efficient cars of the blasting world—getting more done with less energy, which helps lower your carbon footprint.
- Noise Reduction: We all know that shot blasting can get pretty loud, but BlastKing’s machine has built-in features to keep the noise down. Thanks to sound-dampening materials and smart engineering, the noise is reduced, making the workspace a lot more bearable.
- Compliance with Environmental Regulations: BlastKing doesn’t just talk the talk when it comes to environmental responsibility—they walk the walk. Their machines meet international environmental standards, so you can rest easy knowing you’re working with equipment that’s safe and compliant.
- Minimal Chemical Use: Here’s a bonus—unlike some other surface preparation methods, shot blasting doesn’t rely on harsh chemicals. That means no nasty chemical runoff polluting the ground or waterways. It’s just clean, efficient blasting.
Conclusion:
BlastKing’s Barrel Blast Machines aren’t just powerful—they’re environmentally conscious, too. With features like dust control, media recycling, energy-saving tech, and noise reduction, these machines are designed to minimize their environmental impact. While no industrial process is completely without its footprint, BlastKing is leading the charge toward more sustainable surface preparation.
Get A Strong Partner at Your Side Now!
Consult your dedicated surface preparation equipment experts to make your business succeed!
Call us today at +86 135 8931 7685